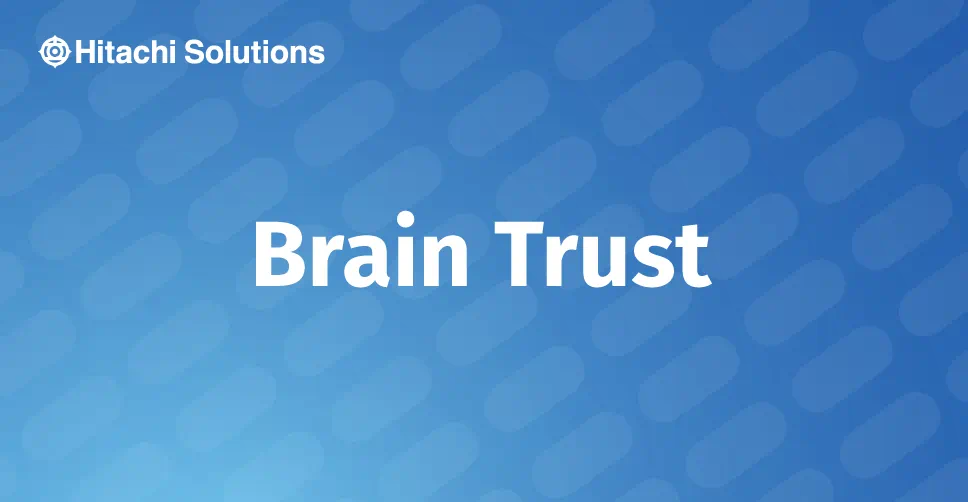
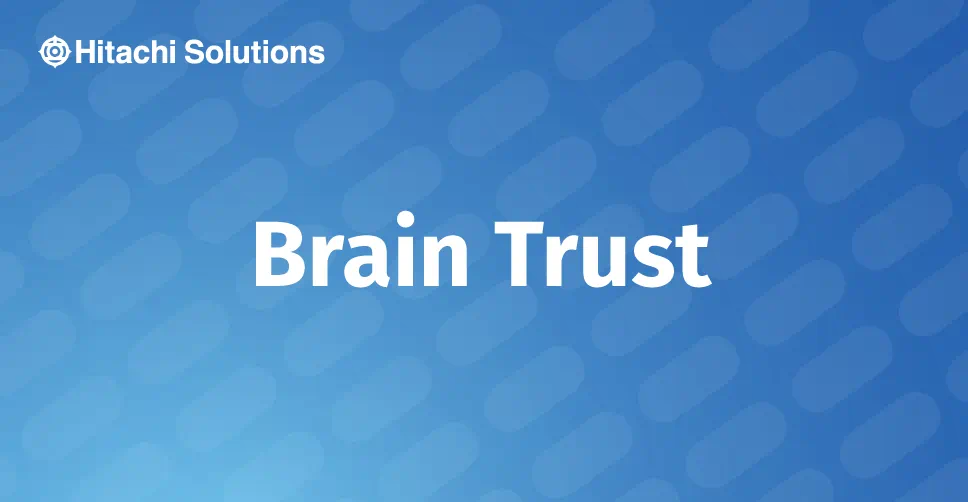
Vendor Consignment is new functionality in Dynamics 365 for Finance and Operations (D365 F&O) and is very useful for the manufacturing industries where many organizations use consignment inventory for production.
Vendor Consignment can also be used in Distribution, packaging industries, and Retail Industries where the vendor can showcase the new products in the market, introducing the existing product in market in the new sales channel.
In this scenario, the production item, which is being consigned, will be owned by the vendor and stored at the organization’s warehouse. The organization can take ownership if the items are ready to consume and then pay the vendor for the items consumed. There will not be any financial impact until the ownership is changed to the organization.
This particular functionality was not available in Dynamics AX 2012 and for this type of process, you would have to use virtual warehouse to track the consigned inventory. Once the item is ready consume, the item will be moved to the shipping/raw material warehouse and it will be sold/consumed. Now in D365 F&O, all these can be handled by using Vendor Consignment functionality with better tracking and visibility.
Parameters/Setups:
Let us look on how to set up the parameters/setups to enable the Vendor Consignment inventory in D365.
Step 1:
Vendor Collaboration field on the Vendor account record enables collaborations forms with this vendor and give access to certain pages to view consigned inventory. (Only when vendor collaboration is used)
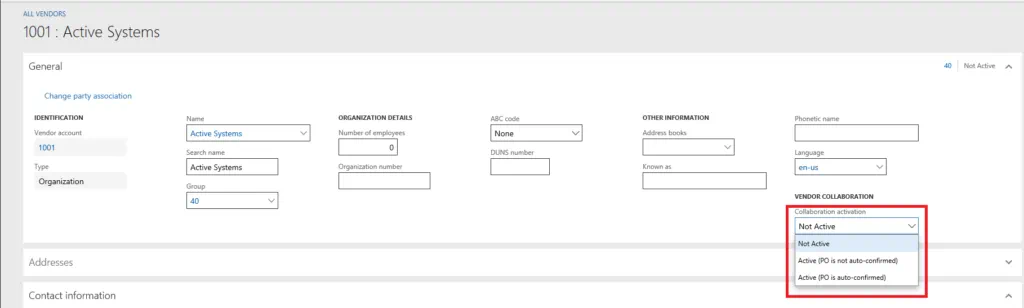
Step 2:
Create Inventory owner to track consignment inventory for the vendor.
Inventory management > Setup > Dimensions > Inventory owners
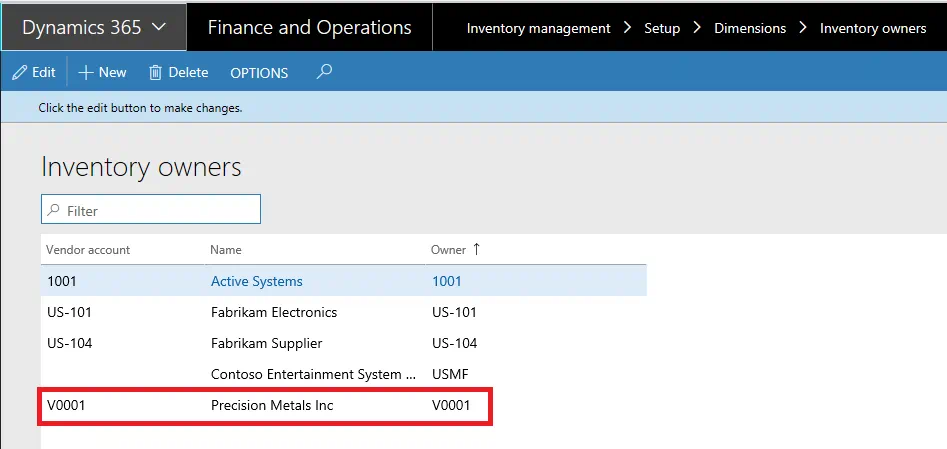
Your current legal entity will be created automatically in the Inventory Owners. For example, my current company in D365 is USMF and an inventory owner record has created automatically for USMF as shown below. This can be used for any other transactions where the inventory is not consigned.
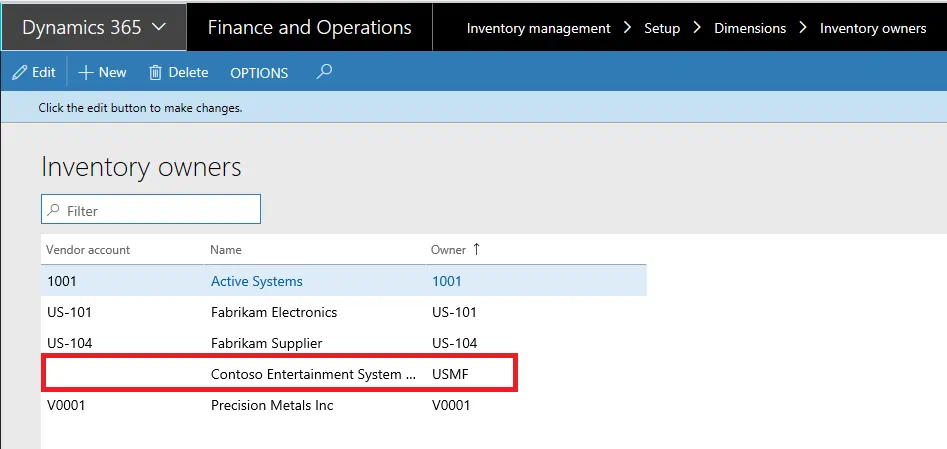
Step 3:
Create Tracking dimension group with “Owner” dimension activated. Owner tracking dimension should be assigned to the items, which will be used for vendor consignment process.
Product Information Management –> Setup –> Dimensions and variant groups –> Tracking dimension groups
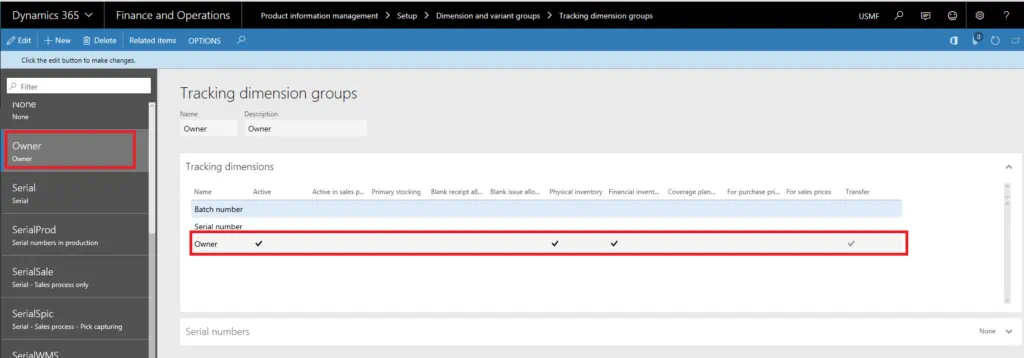
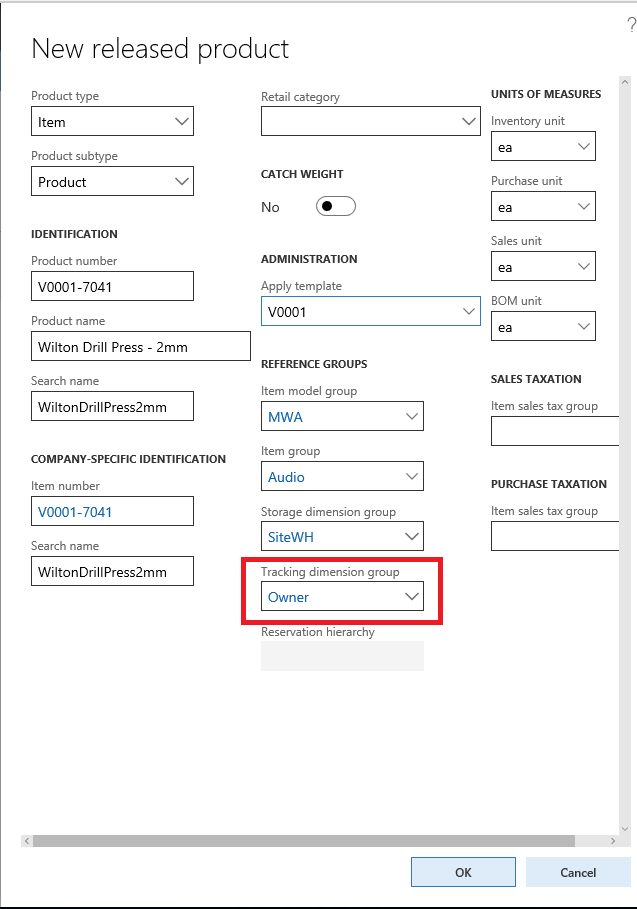
Step 4:
Create Inventory Journal name and assign the journal name in the Inventory and warehouse management parameters.
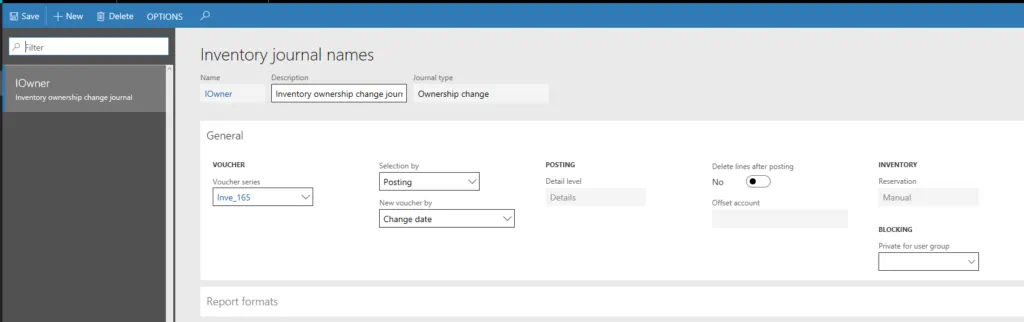
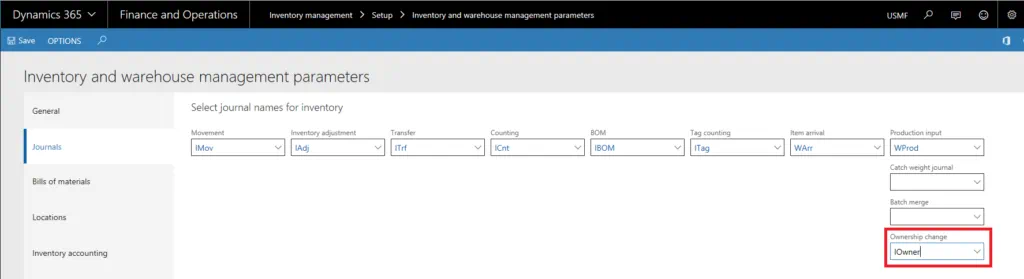
The above setups will enable to use the vendor consignment functionality in D365.
Vendor Consignment Process:
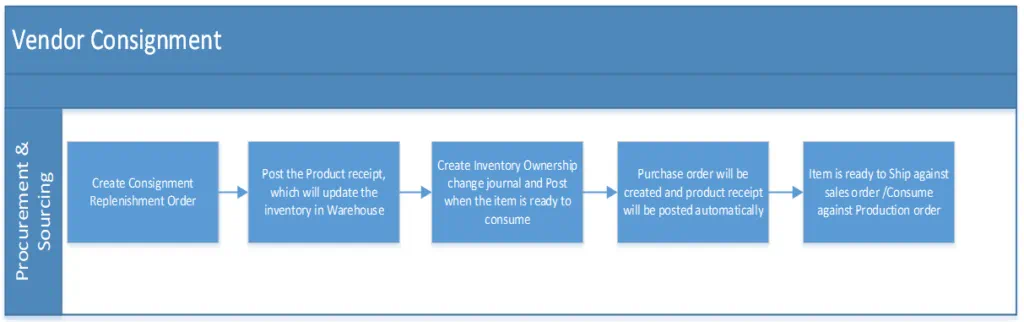
Now, let us get into the process. We need to create a replenishment order for consigned stock, when the replenishment order journal is created, the quantity (Qty) shows in Ordered in Total in On-Hand Inventory (i.e. expected to receive) and owner will be assigned automatically based on the vendor account.
Step 1: Consignment Replenishment Order
Procurement and sourcing –> Consignment –> Consignment replacement orders
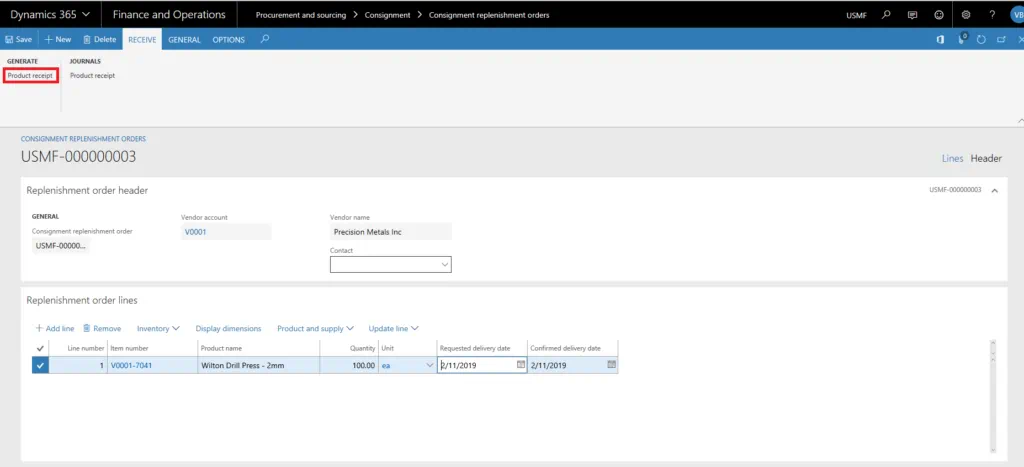
Moreover, when we post the product receipt, the Inventory will be received in the respective Warehouse.
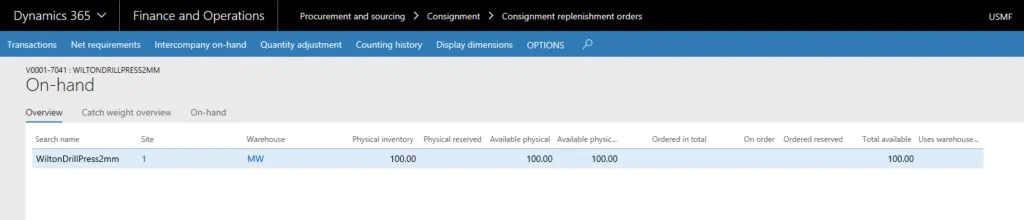
Step 2: Inventory Ownership Change
Inventory Ownership Change will be created when the organization is ready to consume the item, which has been consigned. It is used to accept the consigned Inventory and take ownership.
Procurement and sourcing –> Consignment –> Inventory ownership change
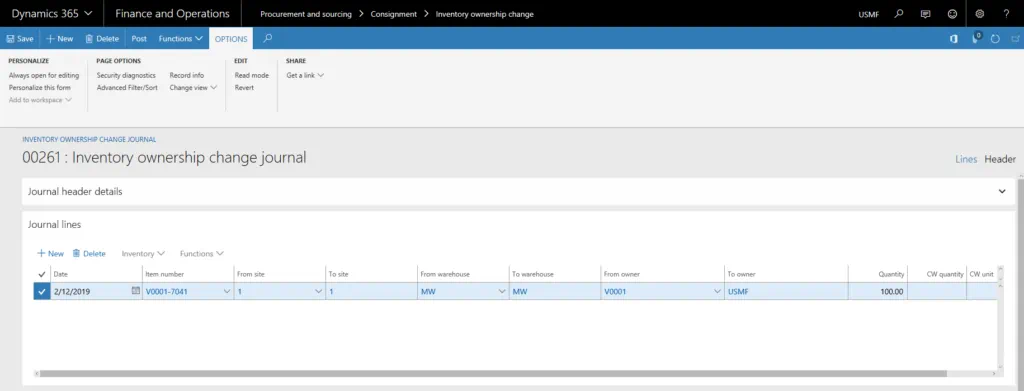
Therefore, once the journal is posted, a Purchase Order will be created and received automatically and the Origin in the Purchase Order lines will be as “Consignment”. The Owner will be automatically changed to your legal entity and further inventory transactions will be posted to General Ledger and will have inventory value. Since the Purchase Order creation and receiving is an automated process, the purchase price has to be defined for the item in Released Products or the item should have trade agreement (purchase) with active purchase price.
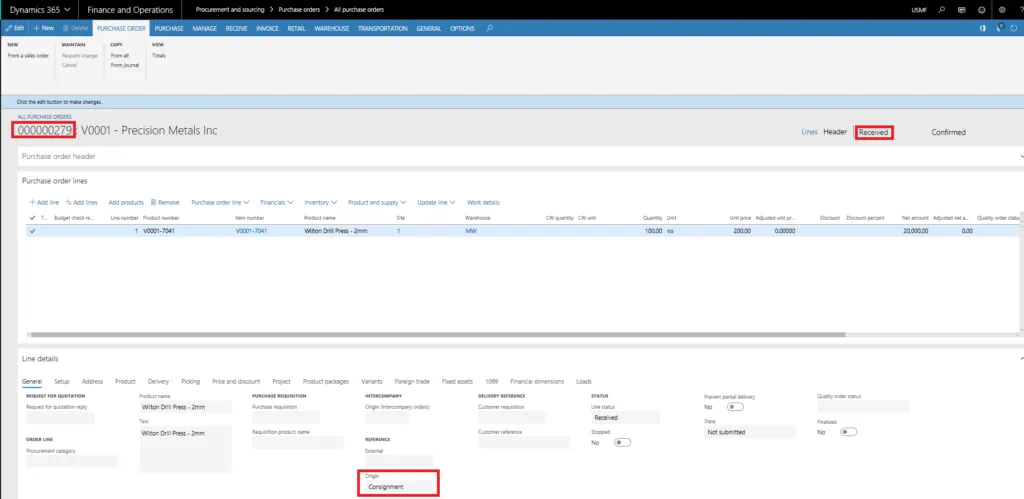
Below is the Inventory Transactions after posting the Inventory Ownership Change journal where the owner changed to the legal entity and now the item is ready to consume against Production order or ship against the sales order.
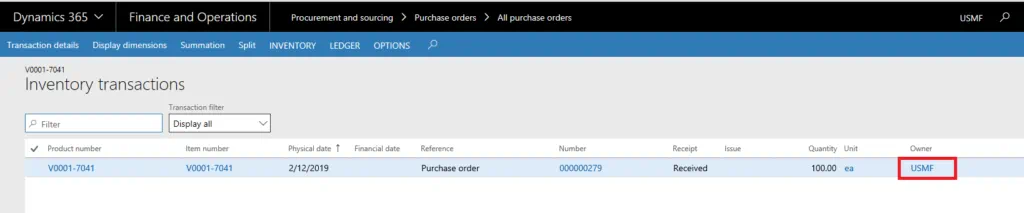
Now that we’ve walked through the parameters and how to set up Vendor Consignment in Dynamics 365 F&O, let’s conclude with an overview of the benefits and limitations:
Benefits:
- Both the Vendor and Organization will have better tracking and visibility on the consigned items.
- The overall inventory cost can be reduced by implementing Vendor Consignment.
- List of consignment purchase orders can be viewed in “Purchase order consuming consignment Inventory Page”, after the inventory ownership change journal posted.
- Receive the vendor owned items in the warehouses physically without any General Ledger transactions.
Limitations:
- The items, which will be used in this process, should have Standard cost or moving average as costing method. If the item will be only in consignment, then no need to provide the standard cost in the item since there will not be any General Ledger transactions, but it must have the standard cost before Inventory Ownership change.
- We will not be able to define the Quality association for the item, which is on Consignment.
- There is no process to update the Item Tracking dimension group at the time of Inventory Ownership Change or later.
- Vendor Consignment process does not work with Advance Warehouse Management functionalities.