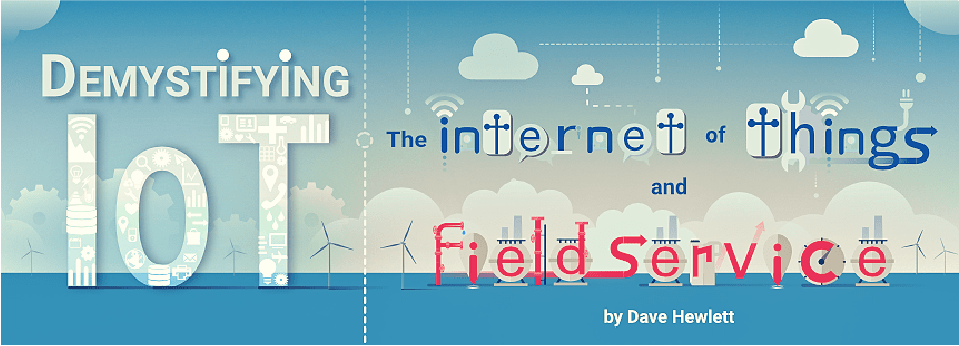
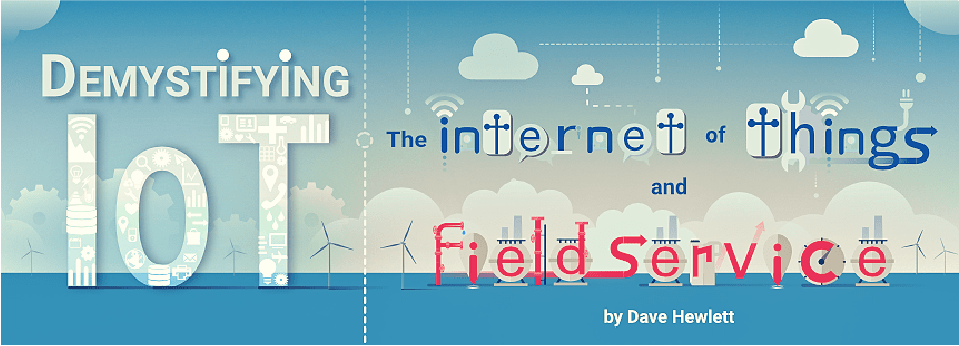
It’s no secret that the key to field service success is to deliver excellent service. Today’s tech-savvy and connected customers value time and demand immediacy and convenience from their field service providers. The quicker and more efficiently a field service organization solves their problem, the better.
To keep pace with customer expectations and remain competitive, field service organizations need to strategically embrace new tools and technologies that can help them deliver the speed and precision customers expect. For example, the Internet of Things (IoT) has emerged as a powerful foundation for field service organizations looking to increase efficiencies, profits, and customer satisfaction.
What is IoT? Put simply, IoT is a network of computing devices connected via the internet. As with any groundbreaking technology, there are quite a few misconceptions surrounding IoT for field service.
Myth #1: IoT is only about technology, not business.
Although IoT and its components are technical, IoT isn’t strictly about technology. At its core, optimized IoT is about receiving real-time data and insight to make proactive and predictive business decisions. IoT for field service isn’t solely about understanding how a machine is functioning at a given moment in time and why it’s functioning that way — it’s also about understanding how an asset will function in the future.
Savvy organizations can use IoT to generate new revenue streams by creating a service model that takes advantage of predictive asset models. The traditional service model is designed to solve a specific issue only after it has occurred, by which point the customer has already experienced disruption. Predictive maintenance capabilities, enabled by IoT, can help organizations create service maintenance offerings that cut costs and increase customer satisfaction while also creating consistent, recurring revenue streams.
This notion of “field service as a service” aims to shift the industry from revenue by reaction to guaranteed recurring revenue. For this model to work, organizations must extend the value of IoT beyond reading and reacting to live signals. Leveraging its potential “as a service” requires organizations to collect and retain data, and then use that data to fuel artificial intelligence and machine learning. Predictive maintenance is driven by data aggregated by IoT sensors, coupled with machine learning algorithms that render that data useful. These algorithms identify and analyze data patterns over time and, in turn, these patterns help predict outcomes.
Myth #2: “My organization will be fine without IoT.”
“Adapt or die” isn’t just a common phrase — it’s a fact of life in the business world. This sentiment is especially true as it pertains to technology. IoT isn’t going anywhere, and companies that invest in IoT for field service are better prepared to compete in a changing, digital-first world than companies that fail to embrace it.
By 2025, the total global worth of IoT could be as much as $6.2 trillion, according to Intel. Most of that value comes from health care devices ($2.5 trillion) and manufacturing ($2.3 trillion). IoT delivers the intelligence an organization needs not only to sustain operational excellence, but also to transform the business according to shifting industry trends and customer expectations.
Businesses that fail to invest in IoT will likely meet the same fate as those who’ve failed to adapt in the past — they’ll risk becoming defunct.
Myth #3: There is no way to measure ROI without IoT.
Some people believe that since IoT is about data aggregation and analysis, there’s no concrete, measurable return on investment (ROI) after implementing IoT. This is false.
IoT transforms organizations by helping them optimize operations. Before the advent of IoT for field service, companies simply hoped that machinery wouldn’t break down, or implemented scheduled maintenance routines to prevent catastrophic failure. When failures did occur, they caused operational downtime and safety risks and wasted resources. Each of these outcomes directly correlated to lost revenue: Downtime causes interruptions in production, wasted resources result in lost margin, and safety risks equate to higher insurance costs and lower employee satisfaction.
IoT offers a way to increase control over operations, which directly contributes to improved margin. IoT offers full insight into operations and into an organization’s most critical assets, which enables analysts to identify areas of improvement, more effectively streamline processes, and enhance overall operational efficiency. Efficiency is a significant contributor to the bottom line: When a business runs more efficiently, it runs more cost-effectively and with higher profitability.
Myth #4: “IoT is plug-and-play — we can implement it on our own.”
An IoT implementation — whether prototype or full scale — should receive expert support. An experienced IoT solution provider has the knowledge, resources, and industry partners required to steer an IoT for field service project to a successful conclusion. A qualified provider knows which devices to use, how to collect data, which pitfalls to avoid, the tools and people required at each stage of the project, and how to leverage data with machine learning processes.
If your IoT implementation isn’t handled by an expert, you run the risk of installation failure, adoption failure, a lack of departmental collaboration, and a longer, more expensive project.
Implementing an IoT strategy is a critical next step for any field service organization looking to evolve in the digital age. So it is essential an IoT provider with the industry, technical, and functional experience to ensure a successful deployment tailored to your organization’s budget, timeline, and resources.
Don’t miss out on the crucial collaboration, data organization, and data analysis opportunities an experienced IoT partner provides — reach out to the team of professionals at Hitachi Solutions to get started today.