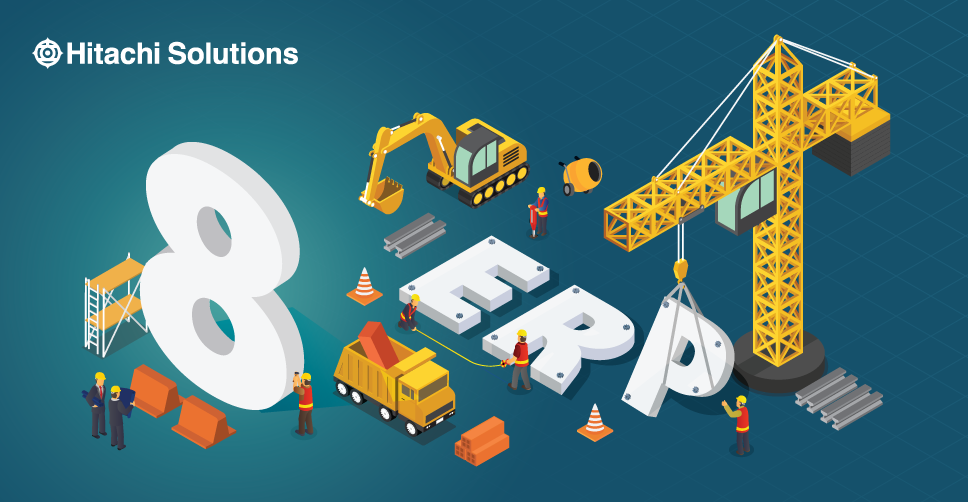
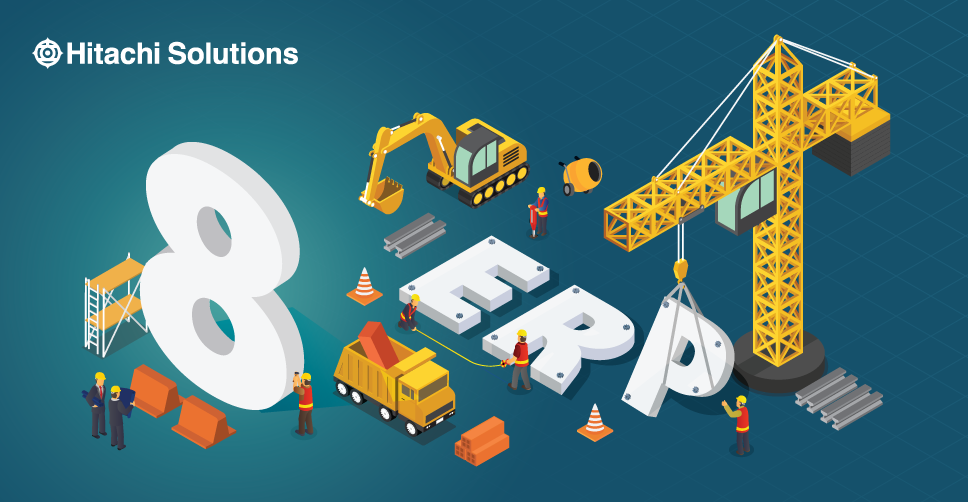
Use Cases in Construction
We’ve uncovered 10 construction use cases where applying one or more technologies can help solve a construction-related problem. Learn more.
Download the EbookEvery construction project consists of many moving parts that must be carefully coordinated to ensure that work is completed on time and on budget. That’s a tall order for any construction firm, especially given the many moving parts on the back end. This includes subcontractor management, asset, and procurement management etc.
Fortunately, in today’s digital-first world, company leaders no longer need to rely on manual processes to manage business-critical operations. Instead, they can leverage technology, such as enterprise resource planning (ERP) software with specific construction industry capability, to manage the resources and information they need to be successful.
What Is an Enterprise Resource Planning System?
An enterprise resource planning (ERP) system is a software solution at the heart of all companies’ financial reporting and critical functions. These systems are designed to help businesses automate, orchestrate, and manage core processes to enhance operational performance. ERP systems in the construction industry support full project lifecycle management and, as a result, are intended to better unify business functions across all departments, including finance, human resources, purchasing, engineering, project operations, and so on.
Common ERP for construction capabilities include:
- System Integration: ERP systems integrate with other mission-critical systems across departments to allow for the seamless flow of data from one system to another. This breaks down data silos, enhances visibility, and creates a reliable, single source of truth that business leaders can use to make company-wide and project-level decisions.
- Process Automation: ERP software for construction have the ability to automate traditionally manual processes, such as invoice creation, revenue forecasting, payroll processing, and more, saving firms time and money.
- Data Analysis: As noted, ERP systems in construction create a single source of truth for company-wide operations. Company leaders, project managers, and supervisors can easily pull this data to run financial analyses and gauge the status of various projects in progress.
- Real-time Reporting: Most ERP systems include dashboards featuring real-time reporting data of sales activity, job progress, resource scheduling, incident alerts, budget spending, equipment availability, and more. This instant access provides a truly holistic view across the business and supports data-driven decision-making. In many cases, project managers can even customize their dashboard view so that they have everything they need in one place, without unnecessary distractions.
- Financial Management: By streamlining processes, consolidating data, and supporting data analysis, an ERP makes it easier for construction firms to generate quarterly financial reports, forecast revenue, manage cash flow, conduct financial audits, and more.
- Workforce Management: ERPs enable construction companies to keep their field crews safe and productive using mobile devices that capture time and activity, update equipment maintenance records, specify requisition materials to be sent to the job site, and record any injuries or incidents that require instant notification.
Real-time data and reporting enables project managers to fully understand each project’s requirements and what labor resources are available to them. Forecasting capabilities enable firms to plan and staff future projects, dynamically scheduling crews so that the right people are available for the job at the right time. - Project Management: By providing a 360-degree view of ongoing projects, assets under management, labor resources, financial data, and more — often across multiple job sites — construction ERP platforms help project managers stay organized and coordinate all activity in order to meet deadlines.
- Supply Chain Management: Construction firms can use ERP systems to automate most supply chain management processes, including demand planning, cost estimating, materials procurement, inventory tracking, and relationship management with manufacturers, suppliers, contractors, subcontractors, and crew.
- Human Resources Management: From real-time employee performance data and administrative automation to digital timekeeping functionality and direct payroll system integration, ERP software for construction eliminates much of the complexity typically associated with human resources management.
- Sales Enablement: CertainERPs include built-in tools that track opportunities through the creation of projects and compare similar projects to new opportunities. This capability enables sales teams to improve their forecasting, determine which opportunities to bid on, assess risk, and generate more accurate quotes.
How Construction Companies Can Benefit from a Modern ERP System
By investing in ERP software for construction, firms can:
- Optimize workflow visibility. By gaining a holistic view of each project and its dependencies, as well as available resources across each job site, project managers can confidently navigate the entire project lifecycle, coordinating end-to-end business processes in support of project goals.
- Enhance cross-departmental collaboration. Thanks to system integration and database consolidation, data silos become a thing of the past. With ERP software for construction, all stakeholders throughout the value chain have access to up-to-date, accurate information and are incentivized to work more closely with managers in other departments.
- Improve risk management. In the construction industry, risk can take many forms, from job site safety hazards and labor shortages to contract disputes and equipment failure. Through data consolidation, real-time reporting, and business analysis, firms can identify and assess potential risks earlier on and engage in proactive risk management, creating contingency plans for all eventualities.
- Engage in data-driven decision-making. ERP software for construction has the ability to pull data from various systems across different departments and store it within a single, centralized location. With all of that information in one place, firms can run data analytics, generate reports, and extract actionable insights that inform key business decisions.
- Supervise asset usage and conditions. Construction companies can integrate their ERP systems with field service management solutions to access real-time data on asset performance and availability. Armed with this information, firms can more accurately determine the timeline for projects and schedule preventative maintenance, thereby ensuring that each piece of equipment runs at peak efficiency.
- Support job site mobility. ERP systems can help project managers stay productive regardless of whether they’re in the office or at a job site through mobile device enablement. This capability enables project managers to access ERP functionality through their smartphone or tablet, so that they can capture all on-site operations — including time and expenses, job service requests, and job procurement — in real-time and make effective decisions while in the field.
- Ensure crew safety and productivity. ERP software for construction can integrate with safety management solutions, enabling team leads to create and maintain detailed incident records, set up automated reporting, build customized dashboards that enhance visibility, and monitor job site conditions and worker behavior to proactively identify and address potential safety risks.
- Monitor project scope and health. With end-to-end visibility across all job sites, teams, and assets, project managers can more accurately gauge the status of different deliverables and the progress of the overall project against stated goals. Project managers can then take proactive measures to ensure that everything stays on time and on budget.
8 Things to Consider When Choosing an ERP for Construction
For construction companies that want to optimize operations and more effectively manage the entire project lifecycle, ERP software isn’t just a “nice to have,” it’s a “need to have.” But not all ERPs for construction are made alike — when evaluating potential solutions, take these 8 factors in consideration:
- Which features do you require? While “all of them” is certainly the easy answer, it isn’t necessarily the best one. An ERP system is a sophisticated and, in some cases, complex piece of technology, which means implementation can take some time to complete, especially if you’re deploying multiple advanced capabilities at once. ERP software for construction can also come with a bit of a learning curve; to make training more manageable for your project managers, team leads, and crews, it’s best to roll out a few features at a time.
To that end, consider your immediate and anticipated business needs and which features align with those needs and prioritize accordingly. The good news is that with the right ERP system, you can work with your solution provider to add new features and capabilities over time based on your evolving needs.
This is also an important question because not every construction ERP offers the same set of features and capabilities — for example, many ERPs do not include built-in equipment asset management capabilities, which can pose a problem for firms that own or rely on heavy equipment assets for their projects. By determining which features you actually need, you can engage in a more targeted search for the right software. - What are your dependencies? In order to get the most out of your ERP investment, you need to be able to set up dependencies within the system to ensure that you have the necessary resources to complete various tasks and that all stages within the project management lifecycle follow the proper order of operations. Before investing in ERP software for construction, take time to identify and clearly define project dependencies so that you can set up your system according to your exact business requirements and hit the ground running after implementation.
- Do you require a Tier 1, Tier 2, or Tier 3 system? Most ERP systems belong to one of three categories:
- Tier 1 systems are designed for enterprise-scale construction firms that typically generate over one billion in revenue each year, employ over 1,000 people, and have complex, global business processes. ERP systems in this category tend to have longer implementation timelines — generally a year or more — and require a substantial project budget.
- Tier 2 systems are well-suited for mid-size construction companies that generate anywhere from $100 million to $one billion in annual revenue, employ 50 to 1,000 people, and have less complex business processes and limited geographic coverage. Systems in this category can have implementation timelines ranging from three months to a year and tend to be less expensive than Tier 1 implementations.
- Tier 3 systems are intended for small construction companies consisting of 50 employees or fewer or for firms that provide niche services; these companies typically do not have complex business processes to manage but can still benefit from the data consolidation and operational insights ERP software offers. Tier 3 systems typically have relatively short implementation timelines — just a few months — and are the most affordable option.
Which ERP tier your firm needs depends entirely on its size, budget, and the complexity of the processes you need to manage; it’s important to choose the appropriate tier of solution to ensure that your company’s needs are fully met.
- Do you require a horizontal or a vertical system? Deciding between Tier 1, Tier 2, and Tier 3 ERP systems is just the beginning — you’ll also want to figure out whether you’d benefit from a horizontal or a vertical solution. For context, a horizontal ERP is more of a general platform, designed to support a wide variety of industries, while a vertical ERP is designed to support the specific needs of a single industry or even a vertical within an industry.
- As a result, vertical ERP systems typically include a more specialized set of features than their horizontal counterparts; for example, a vertical ERP for construction might include project bid management and mobile timekeeping capabilities. For their part, horizontal ERPs offer broader functionality and tend to be more sophisticated than vertical ERPs.
- A growing number of solution providers are attempting to bridge the gap between horizontal and vertical ERPs by offering a horizontal ERP but working with a wide network of partners to deliver more niche, construction-specific capabilities.
- What is your preferred deployment method? When implementing an ERP for construction, most solution providers will offer one of two deployment options: an on-premise or cloud-based model.
- With an on-premise deployment, your firm purchases a software license for each user, and the solution provider installs the ERP software directly onto your company’s servers. This can allow for a greater degree of control over your system — and the data within it — and more consistent connectivity. However, on-premise ERP systems can also be more expensive to maintain and put your firm completely on the hook for data security and system upgrades.
- With a cloud-based deployment, your firm pays to use the ERP on a subscription basis; all of your data is stored within the cloud, and you can access the system from anywhere in the world using any device connected to the internet. Cloud-based ERPs for construction offer lower IT costs, are easier to upgrade, and are highly scalable, which is good news for rapidly growing companies. On the other hand, since they’re hosted by another company, cloud ERPs offer less visibility into how and where your data is stored and secured.
Considering a move from an on-premise to cloud ERP? Read this eBook, first >
- What systems do you need your new ERP to integrate with? An ERP for construction is only as good as its integrations, as it relies on these to ensure the seamless flow of information from one system to the next and to create an end-to-end view of your organization. When evaluating ERP solutions, be sure to ask potential vendors whether they have prebuilt connectors to other platforms in your software ecosystem and, if not, whether they’d be willing to set up custom integrations.
- What does your desired future state look like? Your construction firm’s “desired future state” is essentially your ideal business outcome once your new ERP system is fully operational. Determining what your desired future state looks like before evaluating ERP solutions and providers can help clarify your goals and refine your search.
- What are you looking for in an implementation partner? Which solution provider you choose is every bit as important as which system you choose. Some solution providers take a paint-by-numbers approach to implementation and move on as soon as your new ERP system is live. While there isn’t anything inherently wrong with this approach, such a provider probably isn’t ideal if you’re looking for a more hands-on partner to help you custom-configure your solution and innovate for the future.
When evaluating prospective partners, ask the following:- How long has your company been implementing ERP software for the construction industry
- How will your ERP system meet our firm’s business requirements?
- Do you have a standard implementation roadmap for your ERP system?
- Which third-party systems can your ERP integrate with? Can you offer custom integrations?
- How will your ERP system evolve over time to meet the future needs of our firm?
- Do you have any current clients in the construction industry I can speak to?
Today construction companies are able to implement modern ERPs with desired industry capabilities. With Microsoft Dynamics 365 for Finance and Operations, Hitachi Solutions’ Engage for Construction enables you to manage the entire lifecycle of complex engineering and construction projects both effectively and productively — from preconstruction through closing. Contact us today to learn more about Engage for Construction, or how Hitachi Solutions can support your other industry-specific needs.