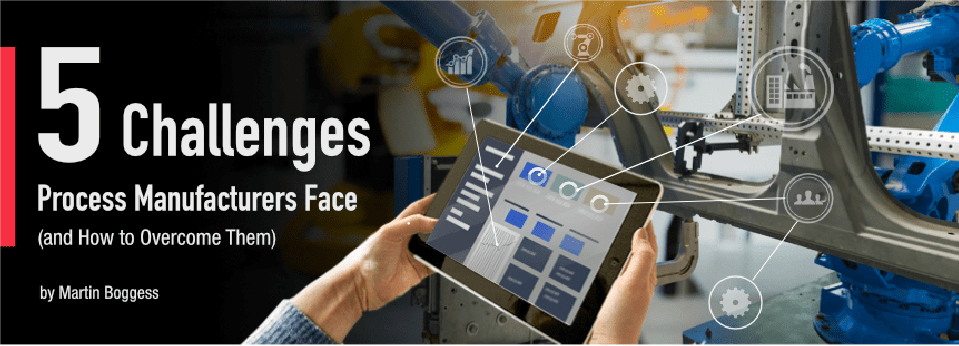
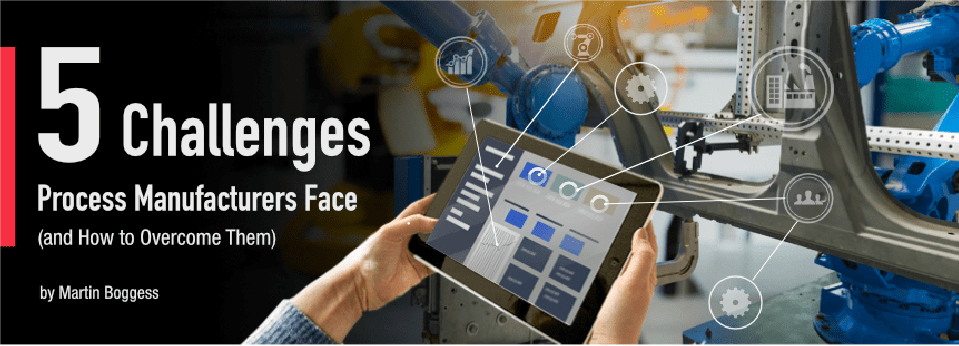
In today’s process manufacturing industry, organizations are expected to streamline operations, reduce costs, regularly update product formulas, drive supply chain efficiencies, increase employee productivity, maintain business relationships, adapt to new legal and regulatory requirements, delight consumers, and more — all while trying to improve their position in an increasingly competitive market. With expectations as high as these, process manufacturers can’t afford to run into any issues that might interfere with productivity.
In this blog post, we’ll look at five common challenges process manufacturers face and how an enterprise resource planning (ERP) system can help you work more productively and profitably than ever.
1) Strict Industry Regulations
Process manufacturers are subject to regulation from the Food and Drug Administration, the Environmental Protection Agency, and other similar organizations. These regulations are designed to protect consumers and the environment from potential biohazards and, if violated, could result in severe fines and irreparable damage to a process manufacturer’s brand reputation. For this reason, it’s vitally important that process manufacturers conduct regular quality control checks to ensure that all raw materials, equipment, processes, and finished products are up to code.
Process manufacturing ERP software has the ability to build quality control and assurance into the production and distribution lifecycles, making it easier to identify and resolve quality issues as they arise. By automating quality control management, process manufacturing organizations not only ensure that their goods and materials are regulatorily compliant, but also save time and effort by streamlining a key business process.
2) Product Inconsistencies
Consumers expect goods from a specific brand — be they chemicals, food, pharmaceuticals, or any other material produced via process manufacturing — to be of equal quality and value every time they make a purchase. This product uniformity is important not only for brand consistency, but for safety as well; unintended deviations in a product’s formulation or recipe could pose serious health risks and have dangerous consequences.
That’s why checking (and double-checking) for product inconsistencies is an essential part of quality control management. As mentioned above, a process manufacturing ERP has the capability to automate quality control testing to identify potential inconsistencies before goods ever leave the production line, thus ensuring that consumers receive the high-quality products they expect and providing manufacturers with peace of mind.
3) Wasted Materials
Waste — often as a result of poor planning or recipe or formula changes — is an unfortunate but inevitable part of any process manufacturing production cycle. That said, it’s in a process manufacturer’s best interest to reduce the amount of material wasted in order to stem profit losses, avoid high overhead, and increase overall efficiency.
With a process manufacturing ERP, organizations can use equipment data to more closely monitor the production lifecycle and identify opportunities to eliminate waste and reduce equipment downtime. Process manufacturers can also use ERP software to create detailed production plans to increase operational efficiency and ensure that perishable ingredients are used prior to their expiration date.
4) Environmental Consciousness
Today’s consumers are more environmentally conscious than ever before and expect the same level of commitment to eco-friendly practices from the brands they patronize. Process manufacturers — especially those who work with chemicals — must be mindful of the affect their ingredients have on the environment and must actively look for ways to reduce emissions and manufacture green products.
Process manufacturers can use ERP software to pull data from manufacturing and supply chain systems and track their carbon footprint, energy consumption and emissions, and environmental compliance metrics. Certain process manufacturing ERPs even support eco-friendly supply chain strategies via environmental sustainability dashboards and accounting templates.
5) Lack of Supply Chain Transparency
Process manufacturers play an integral role in the supply chain, transforming raw materials from suppliers into batches of good, which are then delivered to consumers by distributors. This supply chain should run like a well-oiled machine; if there are issues at any stage, even in supplier or distributor’s facility, it could disrupt the entire production lifecycle, resulting in a loss in profits, as well as potential safety hazards.
For this reason, process manufacturers need to ensure that the raw materials and ingredients that go into their products come from reputable suppliers, and that their distributors deliver goods to customers on-time and in the condition promised. Process manufacturing ERP software provides end-to-end visibility across the entire supply chain, tracks supplier and distributor performance and business relationships, and uses data analytics to provide qualitative insights and drive more informed decision-making.
Hitachi Solutions has decades of experience providing process manufacturers with innovative, industry-specific solutions — including ERP software — built on the Microsoft Dynamics 365 platform. Talk to one of our manufacturing specialists today to find out how a Hitachi Solutions system implementation can improve your existing processes, quality control, and workforce productivity, all while increasing the reliability and profitability of overall operations.