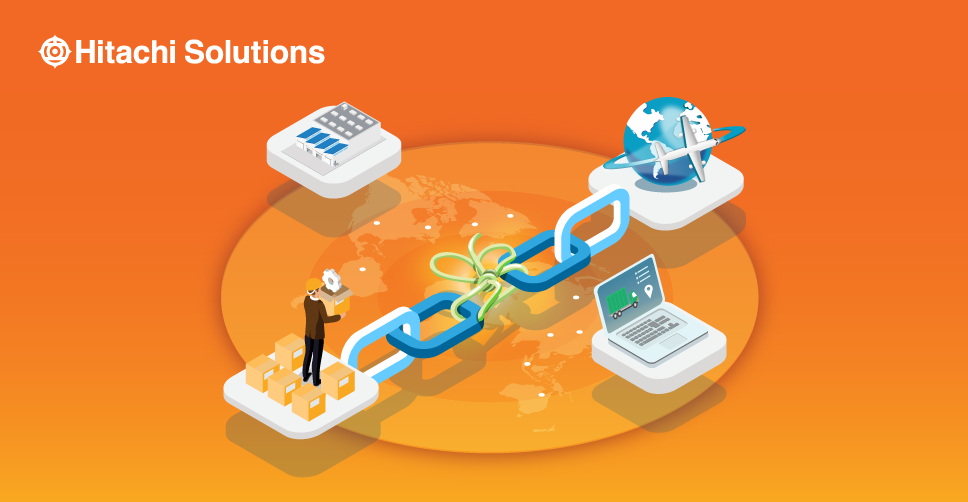
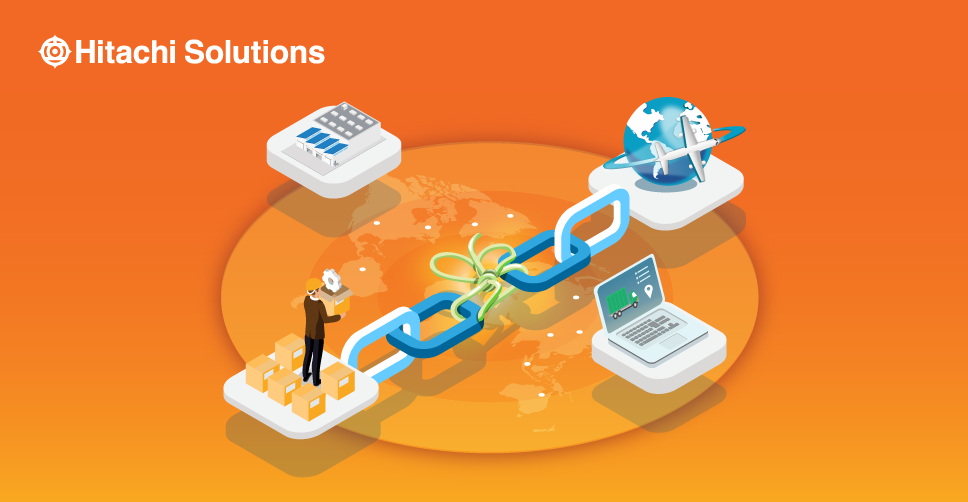
Supply Chain Transformation Workshop
Envision what your future supply chain looks like
Download the OfferThe coronavirus pandemic has exposed significant global supply chain vulnerabilities: With nationwide lockdowns and factory closures in major supplier locations, such as China, manufacturers have had to scramble to find alternative sourcing for raw materials. That said, while COVID-19 may be a once-in-a-generation pandemic, supply chain disruption of this magnitude is nothing new. From geopolitical events to natural disasters, there are any number of scenarios that can introduce risk to — and destabilize — the global supply chain.
Given the many variables at play — some of which manufacturers can reasonably prepare for, and others that can occur without warning — it’s imperative that manufacturers develop adaptive strategies with supply chain resilience in mind.
Supply Chain vulnerabilities & risks to be aware of
As mentioned at the top of this article, there are a number of events and scenarios that can contribute to supply chain disruption. Let’s look at a few real-world examples to illustrate their impact:
Geopolitical Events: The United Kingdom’s withdrawal from the European Union — an event more commonly known as Brexit — sent shockwaves through the global supply chain, especially for UK manufacturers with close ties to EU-based suppliers.
Though the UK and the EU successfully negotiated a free trade deal known as the EU-UK Trade and Cooperation Agreement (TCA) after a roughly three-year transition period, Brexit continues to have a significant impact on “every stage of the logistics process, from transport fees and new limitations to restrictions on imported goods.” And, according to research from Vuealta, a supply chain solutions provider, 50% of UK decision-makers believe that Brexit uncertainty has negatively affected their supply chain in the last five years.
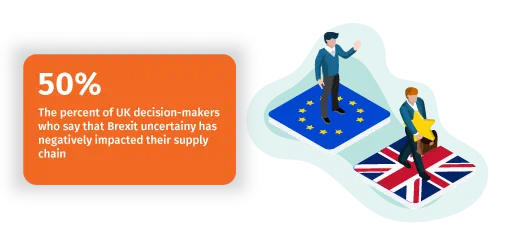
Bringing things stateside, the U.S.-China trade war has dominated headlines over the past few years, in large part due to its impact on the global supply chain. With two of the world’s largest economies locked in a bitter trade dispute, many manufacturers sought to divert trade, find workarounds for tariffs such as transshipment, scale production, and reallocate personnel. The U.S.-China trade war has also led many manufacturers to consider multisourcing as a means of building supply chain resilience and has brought new life to the reshoring movement.
Though a new U.S. presidential administration means new trade relations, according to the Carnegie Endowment for International Peace, “The impact of these decisions on global supply chains will take years to materialize, in potentially unexpected ways.”
Legislation & Regulation: The logistics and manufacturing industries are subject to numerous laws and regulations, many of which can impact the flow of goods and materials throughout the supply chain. A few recent legislative examples include the Coronavirus Aid, Relief, and Economic Security (CARES) Act and the aforementioned TCA.
The CARES Act — an economic stimulus package designed to provide emergency funding for Americans during the COVID-19 pandemic — included multiple provisions that had a direct impact on supply chains, including:
- $350B–$500B in loans for businesses
- $10B in loans for the USPS to support last-mile logistics
- A directive to create a task force to evaluate and address American supply chain vulnerabilities
- $7B for cargo airlines in order to increase capacity in the air freight market
- $60M in funding to help manufacturers respond to COVID-19
The TCA covers a number of different areas in the interest of promoting new “economic and social partnership,” including a Free Trade Agreement. Per this agreement, there are to be zero tariffs and zero quotas on all trade between the UK and the EU, provided that all goods “comply with the appropriate rules of origin.” Despite these seemingly amenable terms, the TCA has, in fact, led to an unprecedented rise in trade barriers, resulting in less trade, economic loss, and supply chain disruption.
Cyberattacks: In our increasingly digitized world, it is, perhaps, unsurprising that cyberattacks have become one of the leading supply chain vulnerabilities. According to CPO Magazine, the supply chain has become a popular target for hackers due to the fact that “vendors often have access to the company’s sensitive data, or have enough access to their network to provide an opening that allows for privilege escalation.”
In 2018, suppliers for Airbus — one of the world’s largest airliner manufacturers — were subject to a series of cyberattacks, in which hackers gained access to classified documents containing schematics for military transport planes and passenger jets, as well as one vendor’s VPN.
More recently, the SolarWinds hack — which introduced trojanized software to the popular SolarWinds Orion IT performance monitoring platform — compromised the private data of as many as 18,000 customers, including Cisco Systems, VMware, and the U.S. Treasury and Justice departments. Similar to the Airbus attack, the SolarWinds hackers manipulated the company’s supply chain, using its third-party vendors’ systems as a point of entry.
Attacks of this nature are becoming increasingly common, exposing significant vulnerabilities within supply chain cybersecurity.
“You can’t assume that [supply chains] defend themselves,” said Chris Inglis, former deputy director of the National Security Agency. “That’s the principle failure that we’re observing in SolarWinds.”
In order to ensure supply chain resilience, as well as the safety of both their and their customer’s sensitive data, it’s imperative that manufacturers proactively invest in cybersecurity.
Natural Disasters: From hurricanes and tornados to snowstorms and tsunamis, natural disasters have long been a bane to supply chains around the world, leading to port closures, cargo flight cancellations, supply shortages, capacity constraints, and more.
For evidence of this, look no further than Hurricanes Harvey and Irma, both of which hit the Gulf Coast in 2017 in the span of just two weeks, leaving a trail of destruction in their wakes. These two hurricanes — which made landfall in Texas and Florida, respectively — had damaging effects on local supply chains.
According to a survey of supply chain managers that the Institute of Supply Chain Management (ISM) conducted in the immediate aftermath of Hurricane Harvey:
- 67% believed that input materials pricing would be somewhat negatively impacted over the next three months
- 27% expected that prices would be negatively or very negatively impacted
- 56% believed supplier deliveries would be at least somewhat negatively impacted over the next three months
- 19% expected that delivery would be negatively or very negatively impacted
- 56% expected that at least some negative impact on prices would continue six months out
At the time, the ISM also cautioned manufacturers that there would likely be raw materials shortages, including fuel, plastic resins, electronic components, and polypropylene, amongst others. These issues were further compounded by the arrival of Hurricane Irma, which caused a series of transshipment hub closures and shipping vessel cancellations and delays.
Natural disasters remain one of the leading supply chain vulnerabilities and, given rapidly changing weather patterns, could become an even bigger risk in the coming years, which leads us to our next item…
Climate Events: The impacts of climate change pose a significant risk to supply chains, adding strength to otherwise ordinary weather events. Take, for example, the ONE Apus incident, in which a container ship encountered severe weather conditions — including gale-force winds and large swells — during a trans-Pacific voyage from Yantian, China, to the Port of Long Beach, California. The incident resulted in the loss of 1,816 containers, including 64 dangerous goods boxes, with total losses evaluated at over $200M.
Though container losses of this magnitude are relatively rare, research from the World Shipping Council (WSC) would suggest that climate events could lead to more severe weather patterns, making them a more frequent occurrence. According to one recent WSC report, 2,567 shipping containers were lost at sea over a two-month period, from November 30, 2020, to January 21, 2021.
And changing weather patterns aren’t the only risk incurred due to climate events. Research from the United Nations Development Programme (UNDP) indicates that rising temperatures in certain parts of the world — particularly tropical locales — could have adverse effects on workers, especially those operating in non-climate controlled environments. All told, the UNDP estimates that the economic impact of climate change on labor productivity could reach $2.5 trillion in global losses by 2030.
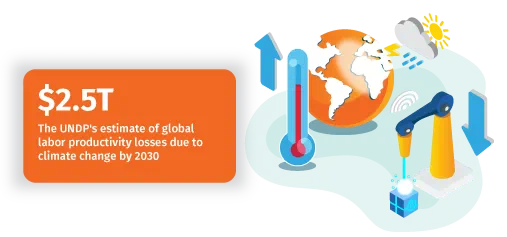
Global Health Events: If there’s one thing that the COVID-19 pandemic has made explicitly clear, it’s that public health crises can wreak havoc on the global supply chain. COVID-19 certainly isn’t the first event of its kind — the 2003 SARS epidemic, the 2009 H1N1 flu pandemic, and the 2014 Ebola outbreak, amongst others, all had devastating effects on supply chains around the world.
Any of these disruptive events has the potential to waylay the global supply chain, causing everything from capacity constraints and sky-high freight rates to material shortages and shipping delays. Given the severity of the situation, the importance of supply chain resilience cannot be overstated.
The characteristics of a resilient supply chain
Now that we’ve defined some of the supply chain vulnerabilities and risks to be aware of, let’s talk about what supply chain resilience is and what it actually looks like.
The concept of supply chain resilience traces its origins to the work of C.S. Holling, a Canadian ecologist who coined the term “ecological resilience” — that is, “The ability of an ecosystem to maintain its normal patterns … after being subjected to damage caused by an ecological disturbance.” In much the same respect, supply chain resilience refers to a supply chain’s ability to adapt to sudden change and unexpected risk.
The experts at Supply Chain 24/7 posit that true supply chain resilience consists of two complementary components:
- Resistance Capacity: The ability to mitigate damage caused by a disruptive event by either avoiding it entirely, or by reducing the period of time between when the event takes place and when the supply chain starts to recover from its effects.
- Recovery Capacity: The ability to return to a supply chain’s original state in the wake of a disruptive event. The recovery process, itself, consists of two phases — stabilization and return.
Though there are many different schools of thought around how to build resistance and recovery capacity, it’s almost universally agreed upon that true supply chain resilience requires preparedness, responsiveness, cross-channel transparency, and — most importantly — supply chain flexibility.
10 strategies to enhance supply chain resilience
- Build redundancy into your supply chain. For every Plan A, have a Plan B, Plan C, and even Plan D in place so that you’re never caught off guard. There are any number of ways to build redundancy into your supply chain — holding additional inventory, working with multiple different suppliers, hiring extra workers, and so on. Whichever route you choose, be sure to consider how the overhead costs required for redundancy will affect your overall spend and be mindful not to introduce unnecessary complexity into your supply chain. If, at any point, redundancies start to interfere with efficiency, look for ways to lean operations.
- Create buffers. Not all disruptive events occur on a macro scale — from employees calling out sick to essential shop floor equipment breaking down, variability is a fact of life for all manufacturers and should factor into supply chain resilience planning. To that end, it’s important to create buffers and make them a part of your process; this is also a great way to build redundancy into your supply chain. There are three primary types of buffers, as shown in the image below:
- Diversify your manufacturing network. This simply refers to the practice of adding new and backup suppliers from a number of different locations to your existing network. Supply chain diversification became a hot topic in the early days of the COVID-19 pandemic when China — one of the world’s leading suppliers of raw materials and manufactured parts — locked down on January 23, 2020.
Forced to come to terms with their dependence on China’s supply chain, many manufacturers began to look to other countries, including Mexico, Vietnam, and even the United States, in order to expand their network. This event should serve as a cautionary tale for all manufacturers, one that underscores the importance of diversification for supply chain resilience. - Consider multisourcing and nearshoring. As mentioned earlier, the U.S.-China trade war has led many manufacturers to turn to multisourcing and nearshoring (or reshoring) as a means of mitigating supply chain disruption. Simply put, multisourcing refers to the practice of partnering with multiple suppliers for procurement, and nearshoring describes the practice of moving business operations to locations that are geographically closer.
Both offer distinct benefits; multisourcing, for example, enables you to work with a larger pool of suppliers, which can help build redundancy into your supply chain, reduce dependence on individual suppliers, and incentivize more competitive pricing among vendors. Nearshoring allows for shorter delivery windows and greater inventory control and can enhance collaboration between manufacturers and suppliers by eliminating time zone and language barriers. - Design standardized processes. Developing standardized, repeatable processes and implementing them across your business makes it easier to onboard and train new employees in a pinch. Additionally, using interchangeable and generic parts and components, where possible, can offer you access to a broader network of suppliers should your supplier of choice fall through, as well as enable you to switch production between facilities in relatively short order.
- Develop ecosystem partnerships. As important as supply chain diversification and evaluating different sourcing options is, not every manufacturer has the ability to rapidly scale up or pare down operations on a moment’s notice. Manufacturers that find themselves in this situation might want to consider partnering with a third-party logistics (3PL) provider to achieve the level of diversification they require. 3PLs typically offer more favorable cost structures, an existing transportation network, better service levels, and access to warehouse management technology, making them an attractive option for manufacturers looking to increase supply chain resilience and flexibility.
- Maintain consistent communication with employees. Train employees on how to react in the face of different disruptive events well before they have the chance to take place. Should a disruptive event come to pass, keep employees in the loop by providing them with access to relevant company data so that they can make informed decisions and routinely updating them on next steps.
- Stress test your supply chain strategy. As good as your supply chain strategy might look on paper, it could contain hidden supply chain vulnerabilities. Stress testing is essential to expose these vulnerabilities and to identify the necessary steps for mitigation. McKinsey recommends a stress-test model that quantifies supply chain resilience based on five factors: industry attractiveness, customer exposure, operations exposure, supply chain exposure, and corporate resilience.
- Expect the unexpected. Although it’s impossible to anticipate every single supply chain risk, data — combined with predictive and prescriptive analytics — can be a valuable tool for identifying potential supply chain vulnerabilities and building strategies to accommodate for them. Be sure to closely monitor potential risk factors and disruptive events as they develop and to partner with a consulting firm that has the data science expertise to contextualize different data sets and provide much-needed foresight.
- Stay nimble. The fact of the matter is that supply chain disruption can and will happen — it isn’t so much a matter of if as it is when. Creating multiple contingency plans can help mitigate the effects of disruptive events, as well as allow for the supply chain flexibility and adaptability required for true resilience.
Build a more resilient supply chain with Hitachi Solutions
From inventory availability to demand forecasting, supply chain resilience starts with better visibility. Hitachi Solutions offers a wide range of industry-specific systems that leverage the latest in business intelligence and data analytics. Our custom-built solutions — all of which utilize the entire Microsoft stack — deliver up-to-the-minute reporting and provide you with a comprehensive view of supply chain activity, including potential bottlenecks and vulnerabilities, so you can make smart, data-driven decisions.
There’s no time like the present to start planning for the future — contact Hitachi Solutions today to take the first step.