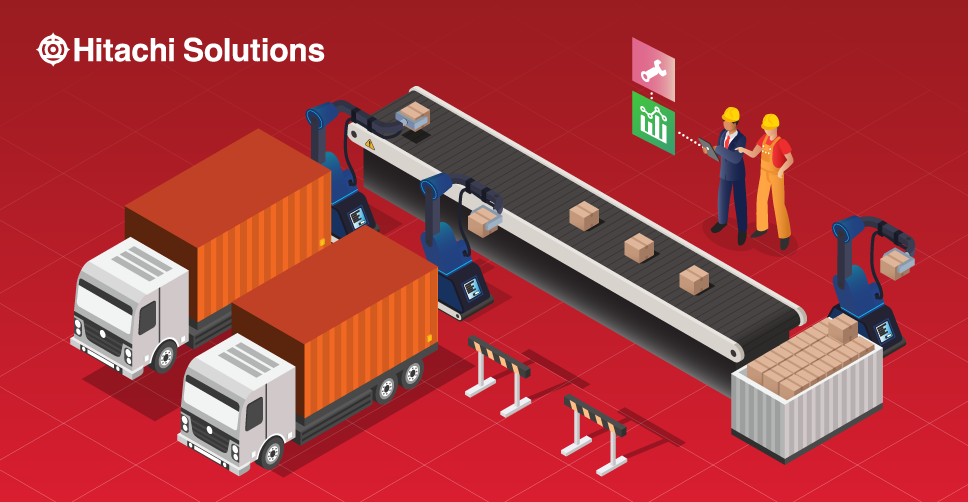
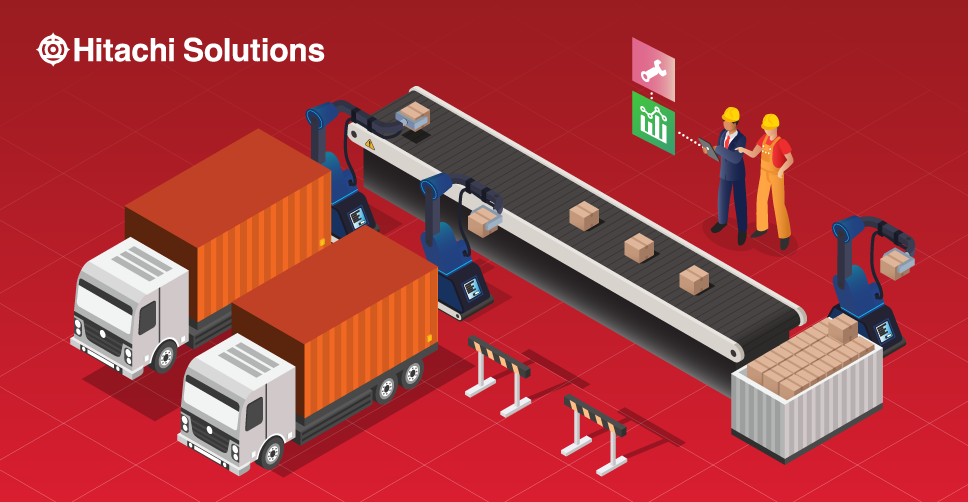
Supply Chain Transformation Workshop
Envision what your future supply chain looks like
Download the OfferAutomation has been an integral element of standard warehouse operations for some time now and plays a key role in powering the global supply chain. In fact, according to market research, the warehouse automation market is projected to reach $27 billion by 2025.
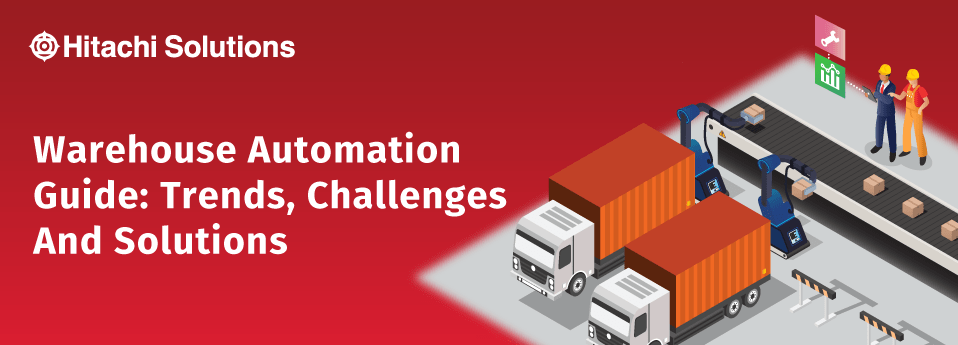
But what is warehouse automation, exactly?
It’s a question without a single, conclusive answer because the definition for warehouse automation varies widely depending on who you ask. That’s because warehouse automation is, itself, incredibly varied and can be applied to any number of use cases, whether that’s sorting inventory or gathering data.
For the sake of simplicity, let’s separate the different types of warehouse automation into two basic categories: process automation and physical automation. Process automation, also known as system automation, refers to the digitization of manual processes; warehouse management systems (WMS) are a common example of process automation. Physical automation, on the other hand, refers to the mechanization of physical processes — think robotic arms removing goods from shelves or driverless vehicles.
Warehousing Challenges
Warehousing is not without its challenges, many of which can be solved using automation. Let’s take a closer look at a few:
- Inventory Turnover: It’s in your best interest to keep inventory moving in and out of your warehouse because the longer an item sits on a shelf, the less viable it becomes, to the point where you may even need to offer a promotion or discount to move it. One of the advantages of an automated warehouse is that automated systems can maximize your inventory turnover rate by gleaning insights from data about how product moves through your warehouse. Based on these insights, warehouse automation software can provide customized recommendations on how to change your current processes and procedures to optimize the flow of inventory.
- Hazardous Materials: Certain materials have federal mandates on how they must be stored and transported. Any product made with such materials must be clearly labeled — or, in some cases, given specialized labels — and stored separately from other products within your warehouse in order to maintain compliance with these mandates. Therefore, it’s imperative that retailers be aware of the different criteria placed upon different materials.
Automated warehouse transportation systems can move such materials from the loading dock to the appropriate storage space back to the outbound shipping dock with minimal risk to employee safety or the integrity of other inventory. These systems can also automatically generate labels upon arrival, so hazardous materials are always clearly marked and compliant.
- First in, First out: First in, first out (FIFO) refers to the freshness of inventory. For items that are serial or batch-tracked, retailers need to be able to pull the oldest items — that is, those that were first in — for shipping in order to avoid write-offs due to expiration. FIFO picking can be challenging because warehouse staff are more likely to pick newer items that sit toward the front of the shelf as opposed to older products that have been pushed to the back. An automated storage and retrieval system is useful not only for moving items in warehouses that have a high volume of loads, but also for FIFO picking because they can be programmed to pull older items first rather than just retrieve those that are closest.
- Traceability: Traceability is essential for any goods that are tracked by serial number, lot, or batch. For businesses that manufacture their own products, if a supplier were ever to notify you that there was an issue with their batching process, you’d need to be able to track down any products made with those raw materials and either dispose of them or remanufacture them. Similarly, if you’re a retailer that sells premade goods, if a supplier were to notify you of a product recall, you’d need to be able to quickly locate that inventory within your warehouse and pull it off the shelves.
Fortunately, warehouse automation makes it easier for retailers to monitor goods moving in and out of their warehouses and to track materials through their lifetime by tracking them via serial number. Should you need to pull items for any reason whatsoever, automation allows for earlier detection and removal, thereby mitigating potential risk to customers or to your brand’s reputation.
The Advantages of an Automated Warehouse
In addition to those listed above, there are numerous benefits to implementing process automation or physical automation within your warehouse, including:
- Increased productivity and efficiency
- Improved inventory control and accuracy
- Fewer issues as a result of human error
- Reduced operating expenses, such as labor, equipment, and maintenance costs
- Lower environmental impact as a result of reduced energy consumption
- Better workplace safety conditions
- Higher workforce retention rates
- Better utilization of warehouse floor space
- Expedited fulfillment process
- Fewer shipping errors
- Increased customer satisfaction
The Top 9 Warehouse Automation Trends
Although disruption has shaped the evolution of warehouse automation, so, too, has innovation. Listed below are some of the leading trends in warehouse automation today:
- Warehouse Robotics: “Warehouse robotics” is sort of a catch-all term used to describe any systems, software, or robots designed to optimize warehouse operations; popular examples include artificial intelligence and autonomous mobile robots (more on those in just a moment). Warehouse robotics is easily one of the fastest-growing segments in warehouse automation, valued at $6.12 billion in 2019 and projected to reach $25.8 billion by 2025.
- AGVs and AMRs: Short for “automated guided vehicles” and “autonomous mobile robots,” AGVs and AMRs are two of the most exciting developments to come out of the warehouse automation market. As their names imply, AGVs and AMRs are entirely self-guided and are capable of completing many of the tasks typically done by warehouse workers, thereby significantly reducing labor costs.The key difference between an AGV and an AMR is that the latter is more sophisticated. Where AGVs typically operate along fixed routes, AMRs contain onboard computers and sensors that make them more adaptive and responsive, and therefore more suited to work alongside people in dynamic environments. Examples of AGVs include automated guided carts, unit load handlers, and heavy burden carriers; examples of AMRs include picking robots, inventory robots, and unmanned aerial vehicles.
- Mobility: Mobility is nothing new, given that handheld scanners have long been standard equipment in warehouses around the world — however, the mobile technology of today looks a little different than what we’re used to seeing. Rather than have warehouse staff carry around clunky scanner guns, a growing number of retailers are looking at moving scanning functionality to sleeker devices, such as tablets and smartphones. Part of the appeal is that mobile devices are capable of doing much more than just scanning: Workers can also use these devices to clock in to and out of their shifts, receive specific instructions for work-related tasks via text, and so much more. Best of all, if you invest in a mobile enablement software solution, you may even be able to implement a bring your own device policy, thereby saving on equipment costs.
- Voice Picking: Thanks to the marvels of modern technology, warehouse employees can now use voice picking systems to pull inventory without ever having to lift a finger. The way it works is this: A worker puts on a wireless headset and states the name or serial number of a product. The accompanying system — typically an AGV or AMR — hears that voice command and automatically pulls the item requested from the shelf. It’s that simple.Automated picking isn’t the only way voice-enabled technology is gaining traction in the warehouse: Warehouse managers can also use wireless headsets to communicate with their employees from opposite ends of a warehouse, and the software systems that accompany this technology are capable of using analytics to monitor and report on employee performance in real time.
- Automated Data Analytics: The primary goal of warehouse automation is to increase efficiency wherever possible; using data analytics automation to identify problem areas and come up with innovative solutions is a natural extension of that. Data analytics enables retailers to leverage the massive quantities of warehouse data they generate on a daily basis in order to find opportunities to further streamline operations. From automating data preparation to data validation to reporting, there’s no limit to what data warehouse automation can achieve.
- IoT: Visibility into everything — from which shelves inventory is located on within the warehouse to where items are in transit — is critical to the success of any retail operation. But achieving a high degree of visibility is often easier said than done. Or, at least, it was prior to the advent of the internet of things (IoT).Some examples of the many ways you can use IoT in your warehouse:
- You can use IoT-enabled sensors, such as Radio Frequency Identification tags, to monitor the movement of goods in real time throughout your warehouse.
- You can leverage IoT technology to receive automatic updates about inventory levels; aggregated over time, this data provides valuable insight into demand and can enable more accurate forecasting, so you know which items always need to be in stock.
- IoT powers AGVs and AMRs, many of which rely on sensor technology to navigate their way through complex warehouse floors.
- Inventory Reservation & Allocation: Even with a high degree of inventory visibility you may, from time to time, find yourself low on stock for a particular item and unable to satisfy customer demand. The good news is that warehouse automation can also help with inventory reservation and allocation. If you are unable to satisfy a customer’s order in full, you can automatically notify them that only certain items within their order can be delivered immediately, and that the rest will arrive in just a few days. You can then automatically reserve those items from your incoming restock shipment, allocate them to the customer in question, and send them to that customer as soon as they arrive to your warehouse. The customer will receive an automated notification that the items they ordered are back in stock and on their way. It’s that simple.
- Cross-docking: Thousands of goods move through your warehouse each day; it’s incumbent upon you to ensure that they move as quickly as possible. We mentioned earlier the challenge of inventory turn and how too often items are allowed to collect dust on shelves and become non-viable. Cross-docking attempts to resolve that challenge by unloading materials from an incoming shipment directly onto an outbound freight carrier (be it a truck, trailer, or rail car) in order to reduce or eliminate entirely the amount of time those materials spend in storage.Although cross-docking, as a strategy, has been commonplace for years, automating the cross-docking process is still a relatively recent innovation. From using an automated unloading system and conveyor belts to AGVs and AGRs, there are any number of ways to automate cross-docking so that goods are out the door and en route to their final destination that much faster.
- Same-day Shipping: Call it the “Amazon effect” — customers around the world now expect same-day shipping from all retailers. It’s a tall order, one that requires impeccable warehouse management, but with warehouse automation, it’s far from impossible. After all, from unloading and racking to picking and packing, every aspect of an automated warehouse is primed for efficiency, meaning you can move goods from your warehouse to your customer’s doorstep faster than ever before.Solutions such as Dynamics 365 have advanced warehouse capabilities that provide retailers such as yourself with key warehouse management metrics, visibility into inventory across all locations (including consignment), and even sophisticated allocation and reservation functionality. These solutions can also integrate with automated warehouse execution solutions to provide additional functionality, such as robot picking.
Dynamics 365: A Fully Automated Warehouse System
Looking to automate your warehouse operations? Microsoft Dynamics 365 offers a wide variety of features and functionality for automated warehouse management, from maintaining detailed inventory records (including product variants) to generating data-driven insights to support distributed order management. Best of all, Hitachi Solutions can make a D365 implementation fast and efficient and customize it to meet your unique needs.
Even if you already have warehouse automation software, we can help extend your existing functionality using solutions from the Microsoft ecosystem, such as Power Apps for custom workflows and reporting and Azure for metrics, modeling, and data-driven insights. Even small changes can lead to significant savings.
Don’t hesitate — contact Hitachi Solutions today to get started.