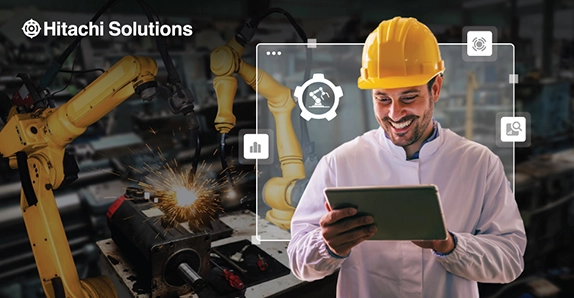
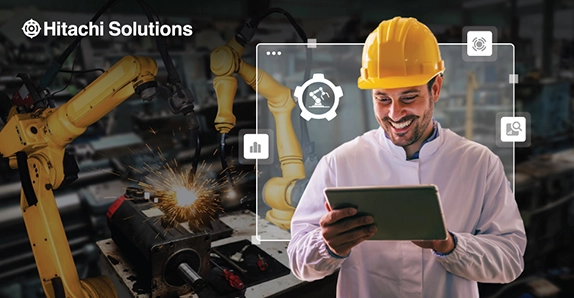
How to Manage Data to Drive Better Decisions
Harness the power of the information that runs your business.
Download the EbookWhat is Digital Transformation in Manufacturing?
The term “digital transformation” started gaining widespread use in the late 1990s and early 2000s, as the Internet began to fundamentally change business operations and customer relations. It became more prevalent with the rise of digital technologies such as cloud computing, big data, and social media and now has come to represent the ongoing process that involves the integration of digital technologies into all areas of a business, driving fundamental changes in operations and delivering value to customers.
Unfortunately, it is difficult to pinpoint an exact date or instance when the term was first used. The concept evolved over time, gaining more specific connotations as new digital technologies emerged and developed.
In contrast, Industry 4.0, representing the fourth industrial revolution, has come to represent our current era in the industrial sector, characterized by interconnected smart factories that utilize technologies like IoT, cloud computing, and AI. The term “Industrie 4.0” (German spelling) was first famously introduced to the world in at the 2011 Hannover Fair in Germany. It was part of a strategic initiative by the German government to digitize manufacturing.
By 2013, stakeholders from companies, trade unions, and politics formed “Plattform Industrie 4.0,” advancing this digital transformation. Germany’s aim was to maintain its manufacturing competitiveness while globally influencing the understanding of digitalization, data, and connectivity’s crucial role in industrial development.
Since then, the concept of “Industry 4.0” has taken off around the world, inspiring many companies, associations, and event governments to take action. As an example, the U.S. launched several initiatives to stay in step with the fourth industrial revolution.
The 2011 Advanced Manufacturing Partnership (AMP) sought to rejuvenate U.S. manufacturing via a multi-sector collaboration, which matured into AMP 2.0 by 2013. This effort, bolstered by the 2014 Revitalize American Manufacturing and Innovation Act and the establishment of Manufacturing USA, was focused on developing a strong national manufacturing research and development infrastructure.
What is the Vision of Industry 4.0?
The original German vision of Industry 4.0 is to pioneer a new age of industrial production that utilizes the power of digital technologies to create smart, autonomous systems. This concept envisions factories where machines, raw materials, and products communicate within an “Internet of Things” (IoT) environment, optimizing manufacturing processes. These interconnected systems would enable real-time adjustments and decisions, leading to significant improvements in efficiency, productivity, and resource management.
Since its original inception, the vision of Industry 4.0 has expanded beyond just manufacturing and Germany’s borders, becoming a global paradigm for all sectors and industries. The initial focus on automation and digital connectivity has broadened to include aspects like cybersecurity, advanced data analytics, machine learning, and artificial intelligence. These technologies have been integrated to provide predictive insights and facilitate decision-making, driving process optimization and customization.
Beyond just production optimization, Industry 4.0 has transformed traditional business models, leading to the creation of new revenue streams. A shift from product-centric to service-centric models, often referred to as “servitization,” has become prominent. Companies now offer comprehensive solutions that combine products and services, often leveraging data gathered by IoT devices to provide predictive maintenance, remote monitoring, or optimization recommendations.
Data itself has become a valuable asset. The capability to collect, process, and analyze large volumes of data has led to data-driven business models, where insights gained can be monetized directly or used to add value to existing offerings.
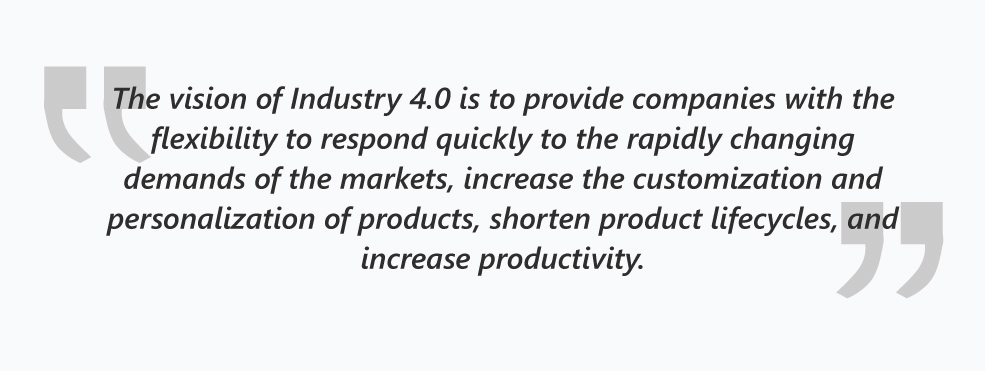
The Tools for Digital Transformation in Manufacturing
Technology adoption typically isn’t within a manufacturer’s core competency, which usually revolves around creating physical products through standardized and controlled processes. Embarking on a digital transformation journey requires the mastery of new skills, new knowledge sets, and a breadth of experience that many manufacturers do not normally possess.
Examples of the skills required include:
- Data science — for interpreting the vast amount of data generated by digital systems
- Cybersecurity — to protect against increasing digital threats
- Change management — to handle organizational shifts
- Agile project management — to oversee technology transformation initiatives
- UI/UX design — to ensure usability of digital tools
Knowledge-wise, manufacturers need to understand concepts like cloud computing, IoT, artificial intelligence (AI), machine learning (ML), and blockchain technology, which are all crucial components of Industry 4.0. Experience is also required in understanding the manufacturing industry, including business operations, production processes, inventory management, demand forecasting and planning, IT and OT, field service, distribution and channel sales models, and more.
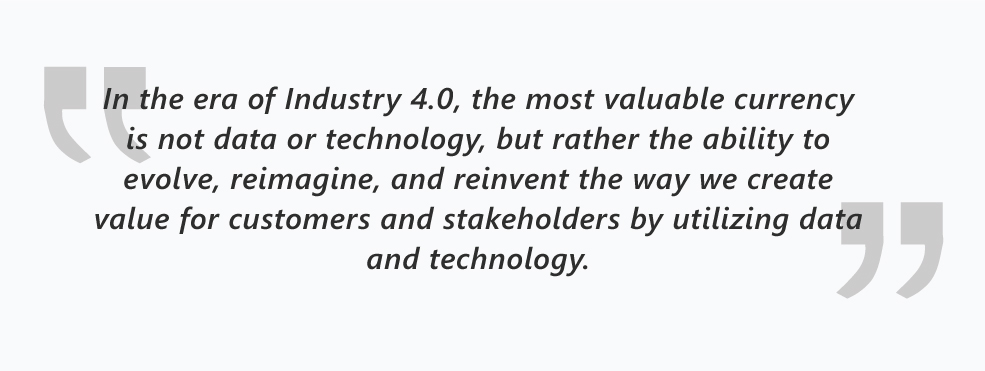
Connecting with a company that specializes in digital transformation within manufacturing can make or break the difference between optimization and a truly transformative initiative. Digital transformation is no small undertaking, but with the right partner who has the experience and expertise, it can be made as painless and seamless as possible.
At Hitachi Solutions, we have been helping organizations of all kinds complete their business and technology modernizations in a way that fits their operation and their industry. We are equipped in understanding the unique needs and challenges facing today’s manufacturers because our company belongs within one of the world’s leading manufacturing ecosystems. In fact, Hitachi is the 24th largest manufacturer in the world with more than 140,000 manufacturing employees in over 400 manufacturing sites.
Hitachi Omika Works — a fellow Hitachi subsidiary — is one of the 132 (as of January 2023) factories in the World Economic Forum’s Global Lighthouse Network, which is a “community of manufacturers [that] shows leadership in using Fourth Industrial Revolution technologies to transform factories, value chains and business models, for compelling financial and operational returns.”
The World Economic Forum acknowledged Hitachi Omika Works in Japan as a Lighthouse in January 2020 for its exceptional use of technology, resulting in significant operational improvements. The factory has cut the lead time for main products by 50 percent without compromising quality, employing solutions like digital-enabled operator and equipment performance management, IoT-based control systems, digital twin customer system simulations, and energy management systems. These solutions utilize a mix of industrial IoT technologies and data analytics across engineering, production, and maintenance.
Value of Digital Transformation in Manufacturing
The value of transforming your manufacturing operations can be found in many places. Yes, you can and should expect a return on your investment, but to get a holistic picture of the value of digital transformation, ask yourself: “Why am I updating my operations?” Odds are there are many reasons and many stakeholders who will benefit — therein lies the value.
Having a solid understanding and strategy for realistically scaling Fourth Industrial Revolution technologies across production networks is critical — and, according to lighthouses, the main obstacle (as opposed to non-lighthouses who view “lack of leadership commitment and investment” as the primary challenge).
But this difference in viewpoint leads to a significant difference in scaling outcomes, per the World Economic Forum: “88 percent of lighthouse organizations report to be on or ahead of their schedule for scaling Fourth Industrial Revolution to at least half of their production network, while only 60 percent of non-lighthouses run on schedule and none ahead of schedule.”
McKinsey reports the key enabler for successfully scaling Industry 4.0 technology, according to Lighthouse manufacturers, is people. To understand the many ways a manufacturing operation benefits from digital transformation, it helps to understand how different groups will utilize these new technologies and enhanced capabilities.
- Business Owners/Shareholders — Business owners see value in increased revenues, profits, and capital efficiency.
- Earnings growth: Directly influenced by improvements in day-to-day operations of a company, optimized using digital capabilities to increase efficiencies. Using advanced data analytics, manufacturers can identify areas where they can enhance value through improved operations, resulting in less waste and more earnings.
- Capital efficiency: Data from the manufacturing floor can also identify working capital opportunities. Manufacturers can more accurately predict demand and forecast upcoming production schedules, driving down inventories and making operations as efficient as possible.
- Employees — Employee engagement drives the company’s success. When armed with the right digital tools, your employees will have everything they need to do their jobs well. When manufacturers invest in their operations, they are taking the steps necessary to keep employees engaged, motivated, and purpose driven. What’s more, when employees use programs that make their jobs easier, it also makes them more productive.
- Customers — Digital transformation shouldn’t just improve your back-end operations; it can also revolutionize your customer service capabilities. Technology and process modernization allows manufacturers to provide the optimal customer experience, with improved communication, personalized offerings, and self-service capabilities. And with greater insight into customer behavior, manufacturers can continue to improve based on real customer opinions and feedback.
Digital Transformation is Not One-Size-Fits-All
The term “digital transformation” is often spoken of as if it’s a monolithic, one-size-fits-all endeavor. However, the reality is far from that simplistic notion. Digital transformation is an intricate process that varies greatly among organizations, dependent on their unique needs, scale, and objectives. There is no single technology, product, or company that serves as a panacea. Instead, it’s all about crafting the right ecosystem tailored to your organizational goals.
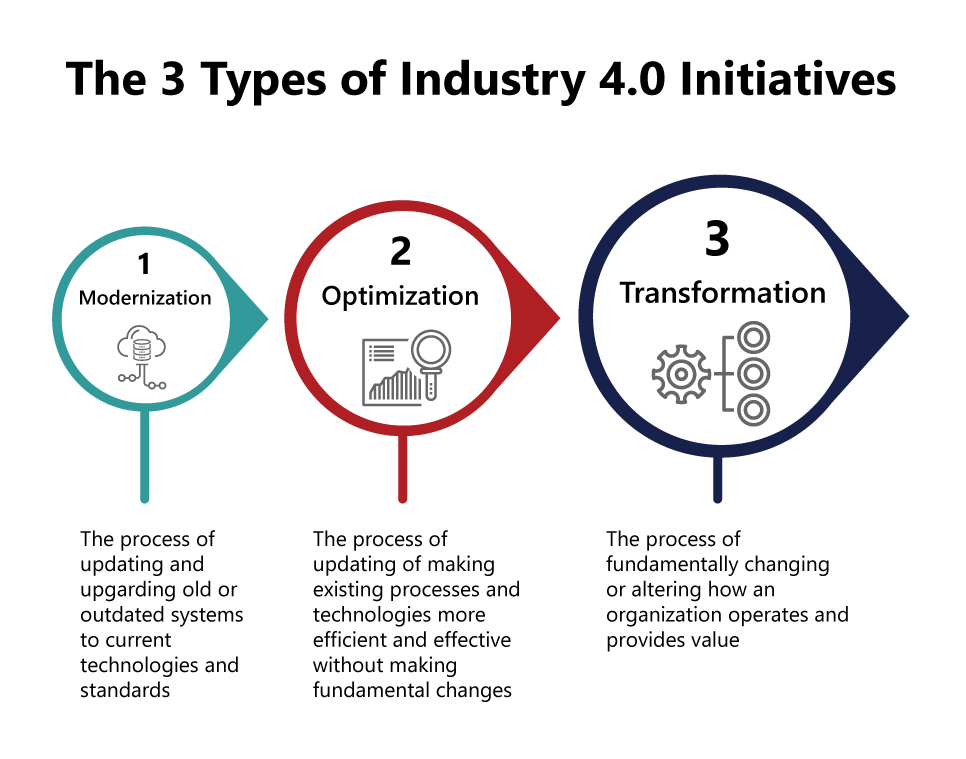
Selecting which technologies to deploy for what purpose at what time is more an art than a science. From AI for data analytics to blockchain for supply chain management, each technology plays a specific role in the digital transformation journey. Integration is key; disparate technologies need to mesh seamlessly for the ecosystem to function as a cohesive unit. Enterprises often collaborate with a range of vendors, consultants, and internal teams to ensure that all platforms and products interoperate flawlessly.
As organizations ascend the maturity scale of Industry 4.0, the return on investment (ROI) amplifies substantially. Advanced digital solutions bring not only cost-efficiency but also innovative features that provide a competitive edge. These high-level implementations often require customized solutions that perfectly align with an organization’s specific operational nuances. As a result, not only does the ROI become more attractive, but the value delivered to customers also sees a significant uptick, further strengthening market position.
How Hitachi Solutions Can Help
Whether you are looking for modernization, optimization, or complete transformation, successful projects all start with the same things — an expert partner and industry-leading technology solutions. At Hitachi Solutions, we have been providing both to our manufacturing customers for years.
We understand digital transformation is never standard. We will take the time to learn about your organization and your people to ensure the best outcomes and smoothest transition possible. To learn more about how Hitachi Solutions can help you get to the next level in your Industry 4.0 journey, reach out to our experts today.