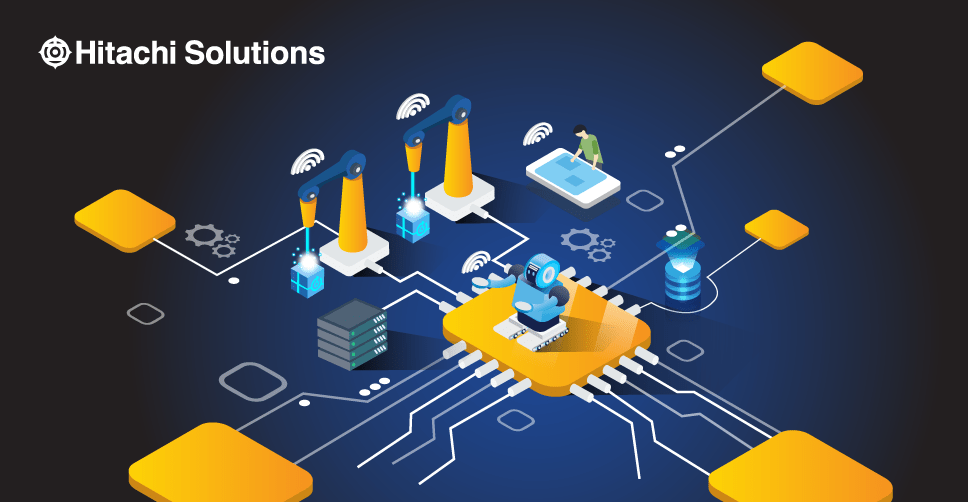
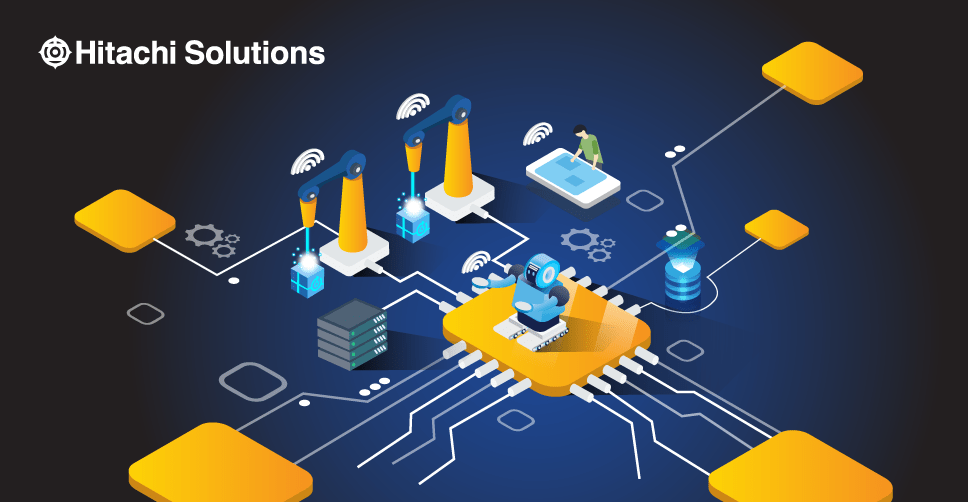
The term “Industry 4.0” is used to signify the beginning of what’s considered the fourth industrial revolution — the previous three being mechanical production, mass production, and the digital revolution. For the past few years, manufacturing’s relation to Industry 4.0 has been about making systems and processes smarter, more efficient, and more precise through the application of innovations in connectivity — such as the Internet of Things (IoT), AI and machine learning, big data analytics, cloud computing, and advanced robotics.
However, if Industry 4.0 was about generating greater value through connected factories and operational chains, then the future looks to be about reintroducing human touch into the process. This so-called “Industry 5.0” is a step-change in focus, involving technology and processes like collaborative robots (cobots) and augmented reality to enable greater human machine integration (HMI).
For those looking to stay on pace with Industry 4.0 and anticipate the evolution of smart manufacturing and digital technologies, here’s an overview of the current state of the industry and recommended steps on how to realize your own digital transformation.
What is Industry 4.0?
Outlined in the book The Fourth Industrial Revolution by Professor Klaus Schwab, Industry 4.0 encompasses “new technologies that combine the physical, digital and biological worlds, impacting all disciplines, economies and industries.” The term has mostly been used to refer to technologies that enable communication and collaboration through the internet to improve efficiency.
Industry 4.0 has had a significant impact over the past few years; manufacturers have seen the growth of automation and data technologies powered by the Internet of Things (IoT), the cloud, and robotics. The seamless integration of software, equipment, and people has brought about the rise of smart factories and made “as-a-Service” business models viable for more manufacturers.
As it has matured, Industry 4.0 has become much more attainable for small- to medium-sized manufacturers. The technology for capturing and processing data, integrating it with information from your ERP, and using it to drive efficiencies and insights to your shop floor, is much more accessible. Businesses of all sizes are now able to get hands-on experience with a much lower investment in time, attention, and money.
Today, there’s a move to go beyond the pure efficiencies of the Industry 4.0 model, a realization that automated smart factories still need to be human-centered. There’s a push for a consideration of how technological and social systems can work in harmony to realize increased personalization, greater sustainability, and improved resiliency. The push toward an Industry 5.0 is meant to place humans back at the center of industrial production to make more effective use of their problem-solving, creative, and critical thinking skills.
Industry 4.0 Manufacturing Technologies
Connectivity, automation, and optimization continue to drive the Industry 4.0 digital impact wave. While this transformation is made possible through new technologies within smart factories, the full potential of Manufacturing 4.0 and the HMI promise of Industry 5.0 can only be realized when people and technology can work together. An essential enabler for these elements to work together is through the metaverse —specifically the industrial metaverse.
There are three categories of the metaverse: consumer, commercial, and industrial. The industrial metaverse brings together how manufacturers design, build, and operate via connections between the physical and digital world. By gathering data through sensors, and processing the information to large-scale repositories, manufacturers can display digital replicas — or digital twins — of any manufacturing process, supply chain, product, or logistics process.
This enables everyone, from line workers to department heads, to design and test concepts before they’re built, optimize the creation of products across production lines, see real-time operational outputs, and run real-time simulations. These digital representations make it easier to optimize predictability and reliability, reducing downtime and energy costs.
These technologies are making a big impact on the quest to digitize manufacturing and operations:
- Industrial Internet of Things (IIoT): IIoT allows for the interconnectivity and collaboration of data, machines, and people in the world of manufacturing. Essentially, it takes IoT — sensors, machines, and data all connected and interfacing seamlessly — and applies it to manufacturing processes. Every element of the manufacturing operation can be connected with IOT components, and capturing data that can be leveraged into optimizing efficiencies across the shop floor.
- Artificial Intelligence (AI): Tools enhanced with machine learning promise next-level results for an Industry 4.0-enabled smart factory. AI companies can use the data generated from a connected factory to optimize machinery operations, adjust workflow in real time, and monitor operations to predict problems and schedule maintenance before the failure impacts customer orders.
- Big Data & Analytics: Because every function of the manufacturing operation is being monitored and generating data, there is an exponential amount of data to sift through. Fortunately, big data analytics systems can utilize advanced cloud-based data stream tools to efficiently process data and give decision-makers the information they need to make improvements throughout the vale chain.
- Cloud Computing: Analytics at this scale and speed require burstable processing capacity and flexible storage options. Cloud-based information stores enable this capacity and flexibility, while providing a single source of truth across the company. Cloud-based systems also make it easier to provide remote access and monitoring of all data and machine operating systems, giving great visibility into operations and efficiencies.
- Visualization: After collecting, storing, and processing data to generate insights, it’s time to create visualizations that help everyone on the team see the same insights in a consistent manner. Cloud environments, combined with shop-floor interfaces, bring advanced visualization techniques such as mixed reality —combining virtual reality constructs with augmented reality overlays — to create digital twins of operations and processes.
- Simulations: By combining today’s advanced mixed-reality simulations with machine learning AI models, it’s easier than ever for both factory and field personnel to run simulations. Before the digitization of the factory, changing over a product line and optimizing its speed and production was somewhat guesswork and always imperfect. With today’s Industry 4.0 technology, manufacturing operations can more accurately optimize machinery for product runs, reduce costs and waste, and save time and money on production.
- Cybersecurity: As every touchpoint on the floor is connected and digitized in Industry 4.0, there is an extra need for robust cybersecurity. Manufacturing machinery, computer systems, data analytics, the cloud, and other connected systems need to be protected. And for many end markets, manufacturers are expected to comply with increasingly stringent standards.
Industry 4.0 Digital Transformation Outcomes
Industry 4.0 continues to have an international impact in the way it’s transforming our global economies. Microsoft COO Judson Althoff explained that the key beneficial outcome of Industry 4.0 and the industrial metaverse is the capability to build “better products more effectively, more efficiently, with lower carbon footprint, lower water utilization, more sustainably than ever before.”
These advantages can be seen in a study by McKinsey, which found that companies that adopted Industry 4.0 digital transformation saw KPI improvements across five areas essential to growth: sustainability, productivity, agility, speed to market, and customization.
Here are six of the biggest and most noteworthy benefits manufacturers can expect from Industry 4.0.
- Optimized Processes: All the Industry 4.0 connectivity — sensors, IoT, AI, digital twins, etc. — services one primary purpose: optimizing manufacturing processes. Automation allows manufacturers to work faster, data analytics empowers leadership to make data-driven decisions to increase efficiency, predictive maintenance means less downtime for machines, and monitoring systems provide real-time yield optimization across the operation.
What does optimized processes and maximized efficiency mean to a manufacturer? In the case of Industry 4.0 and digital transformation, it translates to revenue increases and improved customer service. When manufacturers can get the most out of their production with sensor-monitored machines, all while giving personalized attention and fast service to customers via AI and field service, they can truly see the benefit of the connected factory. - Greater Asset Utilization: Industry 4.0 allows for greater flexibility across the manufacturing operation, which translates to better asset utilization and therefore a potential for revenue increases. Think of automation — autonomous mobile robots (AMR) can handle menial tasks such as product transportation, leaving skilled human workers to do more higher-value tasks.
- Higher Labor and Productivity: When employees feel more secure on the job, they can focus better and accomplish more tasks during the day. Worker safety is one of the biggest benefits of IoT solutions on the manufacturing floor – sensors on site and worn by workers are monitored constantly to ensure a safe and healthy work environment.
Industry 4.0 is also expanding the skills repertoire of many manufacturing workers. As new technologies come into the operation, workers are learning new skills that improve operational efficiency and their skillset. Think of cobots working alongside people in manufacturing workflows to maximize efficiencies, deliver greater personalization, improve quality control, and enhance safety. - Supply Chain Visibility: IoT-enabled sensors and data analytics give manufacturers insight into the entire supply chain and production process. This level of visibility combined with AI and machine learning capabilities means that supply chain optimization can be achieved in real-time.
Some are even calling this next step in supply chain operations Logistics 5.0. Enhanced visibility is a long-term investment that not only allows companies to reduce uncertainties and account for disruptions, but empower their workers and minimize environmental impacts via a “collaboration of digitization and human effort without compromising or neglecting competitiveness and profitability in their businesses.” - After-sales Service: The predictive analytics, virtual reality, and remote monitoring that are pillars of Industry 4.0 also translate to the consumer space after manufacturing. While this doesn’t directly impact a manufacturer, if they create goods that are capable of IoT connectivity, they can drastically improve customer and field service offerings.
Top-notch customer service is a competitive differentiator for many companies and connected equipment in field service is helping to improve the levels of customer satisfaction. With connected devices, manufacturers can monitor product performance, scheduling maintenance before an issue arises and therefore preventing any sort of customer dissatisfaction. - Sustainability: When processes are simulated within the metaverse via the cloud, the reduction in required physical materials and even travel greatly reduces the carbon footprint. Digital models of factories can be used to precisely plan out construction and renovations to minimize environmental impacts. Visualizations of processes and operations can help engineers more easily identify energy and water waste to develop greater efficiencies.
Barriers to Industry 4.0
For manufacturers looking to complete their digital transformation into Industry 4.0, there are a host of potential challenges associated with incorporating these new technologies and processes. Some of these are technical, some are operational, and others are cultural. Here are some of the most common challenges that manufacturers face when adopting the technologies associated with Industry 4.0:
- Integrating Operational Technology (OT) and Information Technology (IT): The largest barriers impeding a successful Industry 4.0 transformation are typically the connectivity and interoperability of legacy equipment. Building the ability to secure the data inputs you need requires a consideration of all the elements of a build out — from the hardware and the infrastructure to the connectivity and the security — which can be a costly and time-consuming undertaking. Older equipment doesn’t provide you with all the necessary data points that you want, and adding new sensors brings additional costs.
- Lack of Financial Resources to Implement Technology and Infrastructure: The second biggest barrier is cost — how expensive will it be to retrofit legacy plant operations, and will the ROI be worth the effort? That’s a question that brings a lot of unknowns, and without effective use cases, it’s hard to predict both what will be needed for an Industry 4.0 transformation and what the long-term return will be.
There are ways to mitigate some of the expected costs. Choosing a cloud-based or software as a service (SaaS) platform means that the provider assumes the costs otherwise borne by your own IT to build and maintain infrastructure. Advances in modern hardware are also helping to bring down the costs of sensors and batteries, making IIoT less of an investment. Advances in communication tech, such as 5G connectivity, eliminates some of the expense of installing cabling or wiring. - Managing Cybersecurity Risks: No cybersecurity protection is perfect, as every system is prone to unseen vulnerabilities and human error.As cyber-attacks threaten to become more and more sophisticated, businesses need the capability to react fast to proactively prevent data breaches or to mitigate data loss. That level of protection can be a heavy burden on both your budget and your IT department. Having a cloud-based service provider that manages your cyber-security measures can do a lot to relieve that burden and better protect your Industry 4.0 technology investment.
- Lack of Training and Skills to Operate and Maintain Technology and Processes: There is a lot of added functionality and features that come with Manufacturing 4.0 operations, but you need to ensure that your personnel have the training and support to fully utilize the processes and technologies.This includes not just the employees on the factory floor, but also field workers who work remotely and the higher-level executives responsible for strategic decisions.
- Overcoming Cultural Resistance to Change: An important first step of training is getting everyone to buy in to the transformation. The impulse to stay with “tried and true” operations can delay the adoption of more efficient and effective processes. The best way to get support from your team involves establishing expectations early, clearly demonstrating the purpose and benefits of the investment in Industry 4.0 technology, and then being open and transparent throughout the implementation process.
- Developing Actionable Use Cases: Part of the challenge of overcoming concerns about budget, training, and adoption is the lack of appropriate use cases. The move toward advanced Industry 4.0 or even 5.0 processes is still novel for many industries — which leaves a lot of unknowns:
- What are you trying to understand from the data?
- Where are the processes where you can find value?
- Even if you have good data, how do you effectively use it?
- What are the returns one, three, or five years into the future?
- What are we getting out of the investment that will justify the ROI?
- Not all use cases are applicable across industries and every company has its own unique set of challenges to achieve a successful Industry 4.0 transformation. That’s why the most effective way to understand your challenges and to plan the is to find a partner that knows the way forward.
The Journey to Industry 4.0 in Manufacturing
How can manufacturers meet these challenges to ensure a smooth transition to Industry 4.0 — or even beyond to Industry 5.0? At Hitachi Solutions, our approach to a modern digital transformation starts with a data-first strategy that is flexible and scalable for any manufacturer to find and define value.
We start by going through your processes to assess your readiness, determine how to build and apply use cases, and then show you some ways forward to manage the large number of processes, templates, and integrations that must be improved and then deployed at scale. Here are the steps for your journey toward a modern industry transformation:
- Create a data model that represents the way you need to run your business
- Redesign your business processes and look at more efficient ways of doing work
- Leverage your enterprise data for additional business insights
- Start delivering business outcomes on your data through low-code applications
- Create outcome-based applications that can be released quickly in sprints
The root of Industry 4.0 is realizing the benefits of connected devices and people, powered by robust technology solutions and data analytics. For companies looking to begin their digital transformation, we work directly with you to bring the value of business insights early into the process of your digital transformation.
Our full suite of manufacturing products, from the IoT Service Hub to Dynamics 365, is built specifically for manufacturers looking to stay competitive in their newly digitized industry. Our model is designed to accelerate your migration from your existing legacy system to maximize your time-to-value and ROI.
Contact our team today to get started.