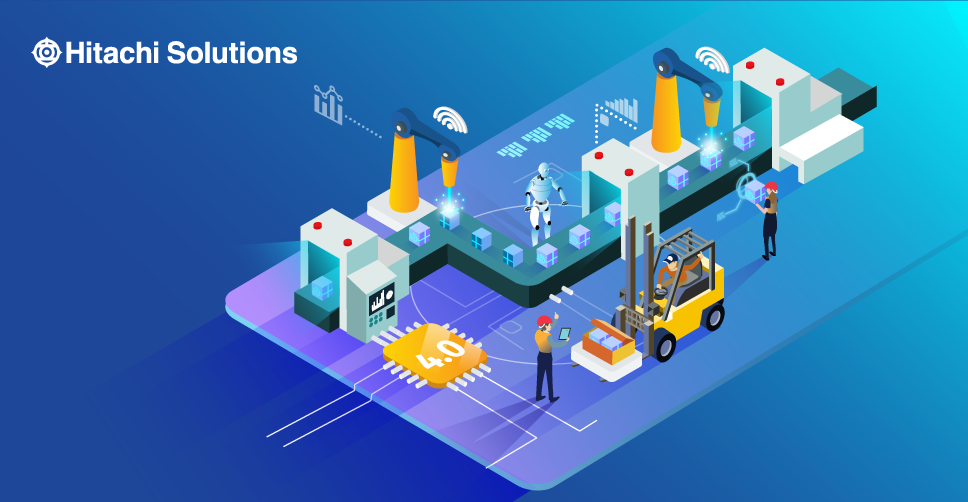
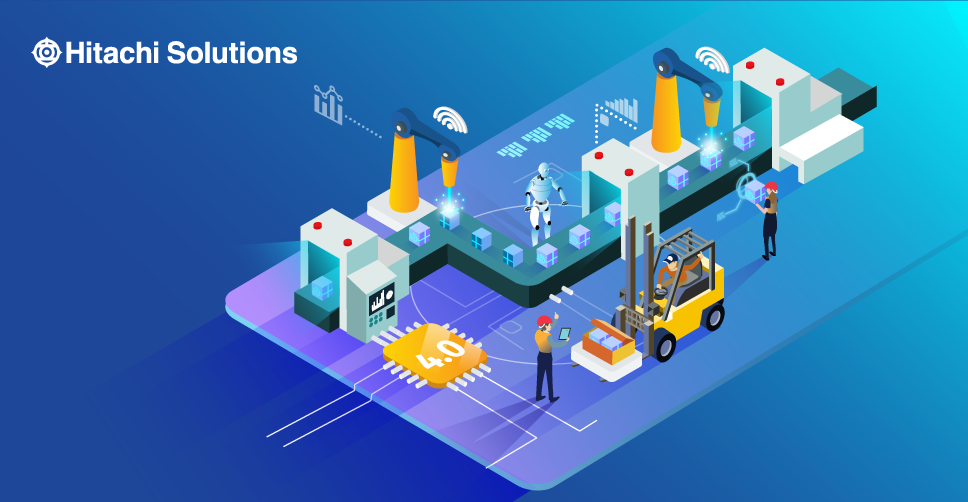
What Do Connected Products Really Mean?
Learn the key components of a connected product, and how to avoid common challenges
Watch the On-Demand WebinarThe implementation and use of the internet of things (IoT) has transformed how industries operate, communicate, and utilize data— and it’s only continuing to grow. It is estimated that by 2025, over 75 billion devices will be connected via IoT.
In manufacturing, those changes have also come at a rapid pace, and an industry that was once slow to evolve is now digitizing at lightning speed. The IoT in the manufacturing market in 2021 value stood at an estimated $62.1 billion, and it will increase to $200.3 billion by 2030, at a 13.9% compound annual growth rate between 2021 and 2030.
Consequently, today’s manufacturers must be agile across all facets of operations to be competitive in the modern marketplace. This need for speed, combined with the advancement of IoT technologies, has sparked another movement in manufacturing — the industrial internet of things (IIoT).
IIoT is the next level of IoT technology and is unique in the way its application has completely transformed manufacturing. Manufacturers that are looking for competitive advantage need look no further than the capabilities that IIoT affords — the benefits impact everything from line maintenance and supplier logistics to employee workflows and offering Product as a Service.
To implement your own IIoT solution, you must first understand industrial IoT and the way it is transforming manufacturing operations.
What is Industrial IoT (IIoT)?
IoT technologies exist all around us – all those interconnected devices we use like wearable technologies and virtual assistants are made possible by IoT. Industrial IoT, then, is taking the digital interconnectivity we’ve come to depend on and applying it to massive manufacturing operations, where the risks are higher, but the payoff is greater.
According to TechTarget, IIoT can be formally defined as “the use of smart sensors and actuators to enhance manufacturing and industrial processes.” As the manufacturing industry transitions from the automated features and connected systems of Industry 4.0 to the enhanced personalization and cognitive computing of Industry 5.0, IIoT can be thought of as a more human-centered approach to manufacturing.
This approach, also referred to as smart manufacturing, is the capability of operators to make better decisions that are informed by Big Data insights gathered by IIoT solutions. For this to happen, manufacturers must invest in the widespread digitation of their operations. There are four primary pillars that support a fully IIoT-enabled operation:
- Smart machines equipped with sensors and software that can track and log data.
- Robust cloud computer systems that can store and process the data.
- Advanced data analytics systems that make sense of and leverage data collected from systems, informing manufacturing improvements and operations.
- Valued employees who are trained to put these insights to work and are supported in ensuring proper manufacturing function.
IIoT Adoption in Manufacturing
Embedded industrial IoT is understood to be an essential part of manufacturing’s future, powering revenue generating strategies like data monetization and new commercial models like Equipment as a Service. Gartner predicts that by 2023, 20% of industrial equipment manufacturers will make use of remote Industrial IoT capabilities, a sizable increase from a 2021 base of near zero.
So, what can manufacturers expect from today’s industrial IoT solutions? These are 8 of the biggest benefits of adopting a fully connected IIoT manufacturing operation.
- Increased efficiency
The biggest benefit of IIoT is that it gives manufacturers the ability to automate, and therefore optimize their operating efficiency. Robotics and automated machinery can work more efficiently and accurately, boosting productivity and helping manufacturers streamline their functions.
Additionally, physical machinery can be connected to software via sensors that monitor performance on a constant basis. This enables manufacturers to have better insights into the operational performance of individual pieces of equipment as well as entire fleets.
IIoT-enabled data systems empower manufacturers to improve operating efficiencies by:
- Bypassing manual tasks and functions and implementing automated, digital ones
- Making data-driven decisions regarding all manufacturing functions
- Monitoring performance from anywhere – on the manufacturing floor or from thousands of miles away
- Shorter Time to Market
Greater operational efficiencies also allow for a faster and more efficient manufacturing process. Industrial IoT solutions enable direct communication from network components to employees, which:- Enables faster decision-making in reaction to market fluctuations
- Provides greater insights into supply chain operation and improves response time to disruptions
- Identifies inefficiencies in the product cycle time, allowing for better optimization in different lines
- Reduced Errors
Industrial IoT empowers manufacturers to digitize nearly every part of their business. By reducing manual process and entries, manufacturers are able to reduce the biggest risk associated with manual labor – human error.
This goes beyond just operational and manufacturing errors. IIoT solutions also can reduce the risk of cyber and data breaches caused by human error. According to the World Economic Forum’s Global Risks Report, 95% of cybersecurity threats have been traced back to human error. AI and machine learning-enabled programs and machinery can do much of the required computing themselves, eliminating the potential for someone to make a simple mistake and put the manufacturer’s data at risk. - Predictive Maintenance
Nothing negatively impacts a manufacturing operation more than machine downtime. Experts estimate that the average manufacturer experiences 800 hours of equipment downtime a year, which adds up to an industry-wide cost of $50 billion a year in unplanned expenses. What could be causing such drastic issues that manufacturers cannot operate? The answer is simple — lack of proper and predictive maintenance.
When maintenance in the manufacturing world is reactive rather than proactive, manufacturers are stuck trying to identify what the issue is, how it can be repaired, and what it will cost. With predictive maintenance powered by industrial IoT solutions, all of those issues are alleviated.
When machinery performance and function are monitored consistently, manufacturers can create a baseline. This baseline and the corresponding data empowers companies with the information they need to see any issue before it occurs. They can then schedule maintenance prior to downtime, which benefits them in that they:- Have the parts required for the job
- Know the cost of the project beforehand, and can budget for it
- Move production to another area of the facility, so the product quotas are unaffected
- Ensure that machinery is operating at maximum efficiency
- Improved Safety:
All of the data and sensors required of a fully functioning IIoT manufacturing operation are also helping to bolster workplace safety. “Smart manufacturing” is turning into “smart security” when all of the IIoT sensors work together to monitor workplace and employee safety.
Integrated safety systems are protecting workers on the floor, on the line, and in distribution. If an accident occurs, everyone in the facility can be alerted, operations can cease, and company leadership can intervene and make sure the accident and incident is resolved. This incident can also generate valuable data that can help prevent a repeat occurrence in the future.
A newer option some manufacturers are utilizing is the use of wearable technology among their employees. Wearables have been part of IoT since its infancy, and it are just now being utilized in industrial IoT operations.
Wearables help leadership keep tabs on things like employee posture and the surrounding noise levels, and they can then improve work conditions and potentially improve performance. They can also alert employees when they aren’t following proper workplace safety procedures, so they can correct their actions and stay safe on the job. - Line Optimization
If the initial utilization of IIoT during Industry 4.0 was about individual machine optimization, today’s Industry 5.0 is now more focused on optimizing the entire manufacturing process. IIoT solutions allow for the standardization of work output across an entire production line, making it easier to optimize operations across entire plants.
For example, say you have six plants, each with different capabilities and production lines. Industrial IoT provides the capability to look at the manufacturing process across each plant, allowing you to review factors like machine capabilities, current capacity, and overall availability. These insights make it easier to determine the most efficient place to make a specific product across all sites and how to enable operation efficiencies across different processes in multiple locations. - Digital Twins
Digital twins refer to exact virtual copies of physical objects made possible by IoT, AI, machine learning, and cloud computing. With virtual copies of equipment and spare parts, engineers and managers can simulate numerous processes, conduct experiments, discover issues, and achieve needed results without risking or damaging physical assets.
Digital twins also allow a look at the bigger picture across the entire production line while it’s in operation, for a better review of efficiency and performance. Through digital recreations, you can take a deep dive into a representation of a single machines or step back for a larger view of the entire process. This enables you to see where any performance bottlenecks may be occurring. For example, if your feeder is slow, a review of digital representation of the production line could reveal an inefficiency with the packaging system. - Reduced Costs
Knowledge is power, and the knowledge provided to manufacturers via IIoT solutions is giving them the tools they need to reduce costs and generate more revenue. Data-driven insights into operations, production, marketing, sales, and more can steer businesses in a profitable direction.
All of the aforementioned benefits of IIoT – predictive maintenance, fewer errors, improved quality control, and maximized efficiencies – will all boost profits for a manufacturer. Industrial IoT also offers arguably the most valuable tool for leaders of a manufacturing company – insights from anywhere, anytime.
Remote monitoring of manufacturing operations is now possible 365 days a year, 24/7, from anywhere in the world. This 360-degree view into the entire manufacturing process, and the follow-up service provided to customers in their buying journey, is an invaluable asset.
Dimensions of IIoT Impact
IIoT isn’t limited to one area. IoT solutions for manufacturing allows for the tracking and asset optimization of all areas, from the start of the supply chain to product delivery. Here are the major areas into which IoT can provide improved visibility:
- The Shop Floor — When implemented correctly, IIoT allows for the continuous monitoring of production conditions, allowing operators to make instant data-driven decisions to maintain the equipment in working order and improve product quality. Real-time updates can also aid managers in tracking the health conditions and location of industrial workers operating in hazardous environments and improve their safety levels. Thanks to greater insights into the production line, IIoT can aid in capacity and production planning.
- Field Operations — In the field, IIoT enables operators a better look at big-picture elements like fleet performance, which can provide greater insights into the entire roll-out of a product rather than just data relevant to individual product performance. IIoT also enables features like predictive maintenance, which is a key component in providing managed services to customers. Other features like virtual equipment monitoring makes it easier for field service workers to be fully aware of a product’s location and condition, reducing response time to service calls and increasing customer satisfaction.
- Supply Chain — The past few years have emphasized the importance of being more aware of supply chain disruptions. With IIoT devices installed at important points throughout the supply chain, you are better able to monitor the movement of supplies and goods to prepare for potential disruptions. IIoT devices also provide the ability to see detailed information on items in warehouses or control the conditions (temperature, humidity) under which products are stored or transported, ensuring a quick response time to any potential problems.
- Remote and Third-Party Operations — The more third-party services and vendors you engage with, the more complicated it can be to optimize production. IIoT allows for the monitoring of all distributed and outsourced processes through a centralized platform. This is the best way of ensuring that all contractors observe the correct processes and that all produced goods comply with set standards.
Components of IoT
Enabling an IoT solution requires a few essential components, which mainly consist of the connected devices, the connection itself, the software platforms, and your personnel:
- Connected products — These are interconnected individual elements like devices, security components, application software, controllers, etc. You’ll need to decide what is out in the field or on the shop floor that’s collecting data. You’ll also need to determine what data is being collected, what sensors are used to collect the data, and the AI algorithms that are driving the devices.
- Digital communication infrastructure – That data isn’t doing any good if it’s trapped within a device. There needs to be a means of transmitting that data via either wired or wireless connections. Whether sent across a closed network or through the internet, the transmission needs to be consistent, reliable, and done in real-time.
- Software and analytics — Where is that data going, and what happens after you’ve collected it? You need scalable software platforms capable of Big Data storage that can manage and analyze defined elements to deliver specific insights. Having a robust, adaptable, and connected platform will help define your managed service capabilities.
- Personnel – Don’t overlook the engineers who are creating the devices and developing the AI or the people who are responsible for making the decisions based on the received data, insights, and reports. You’ll need ensure that everyone is appropriately trained to operate and understand the system.
Understanding what comprises an industrial IoT system is just the beginning — implementing and realizing the benefits will require addressing some challenges.
Challenges of Industrial IoT Adoption
One way we understand the challenges of IoT implementation is by looking at the different areas where manufacturers we’ve worked with have hit a wall or run into difficulties.
- Deciding on the device(s) — At a fundamental level is the decision of which device or devices will be collecting data. Is it an entirely new device, or is it an existing device that will be updated with new sensors? It sounds like a simple decision, but various factors from logistics to budgets can make it complicated.
- Establish how to collect data — Once you’ve settled on the device(s), you’ll need to determine how you will collect the data. If you need to add sensors to a device, how will they work? What are the algorithms that determine which types of information are collected? If there are no existing electronics or available power, how can you enable the device in a manner that’s secure, protected, and reliable?
- Enable communication — After you’ve added sensors, how do you enable communication? How can you transmit the data if there’s no Wi-Fi enabled nearby, or the device is locked within a metal box? You’ll need a means of collecting and analyzing information and tracking serialized data.
You’ll also need to prioritize security and safety by implementing efficient protection for your data. Manufacturing is a primary target for hackers, and each connected item is vulnerable to cyberattacks, including sabotage and IP theft. - How will you manage the data — Once you have the ability to collect the data, you need to know you’ll manage it. Is the system scalable? How does the system manage updates or address problems without an interruption in service? If you’re used to working with on-prem systems, how can you move to utilizing cloud services?
There must be standardization across all devices. Machines from different vendors are likely to have different information, outcomes, metrics, etc. Because there are no universal standards, too often it’s difficult to break down silos based on the vendor or equipment.
It can be very challenging to create a centralized model and a single viewpoint that meets your needs, especially when integrating with legacy systems. How do you create data modelling that accounts for the variances of the different equipment types without data losses and security inconsistencies? - Understand what you are you using the data for — Most companies struggle with this step. Essentially, you’ve done all the work, but now how do you monetize the data? The initial impulse is often to sell the data, but that’s a short-sighted solution. Your data can be used to open new markets, cross-sell other products, or even change your entire business model. Ask how can you use that collected data to create value for your customer?
To secure buy-in across the company there has to be an understanding of the value provided by industrial IoT. Too often companies get stuck on solving the technical problems and focus entirely on the investment into hardware (sensors, gateways, etc.), connectivity, cloud storage, administrative labor, technical support, and more. To accurately consider IoT solutions and effectively implement them in a manner that can generate a good ROI, you need to reach that understanding of value — both to the company and your customers.
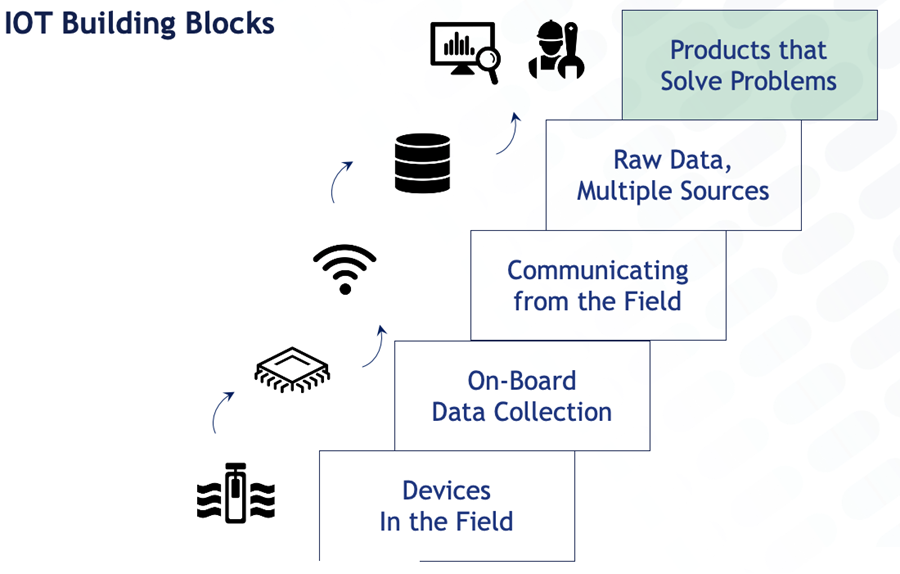
Reaching the point where you understand the value you can create with an IIoT solution is an important victory, though there are issues that need to be addressed. While some are technical, others based on company culture may be more difficult to overcome.
Examples of IIoT in Manufacturing
We’ve worked with a few manufacturing companies that have seen the successful utilization of connected products.
You’d expect a provider of smart fire trucks to enable common smart fleet management services, such as proactively flagging vehicles for needed service to reduce downtime. However, the trucks also included connected devices to the fire suppression gear and rescue equipment. This only enabled predictive maintenance it also simplified certain aspects of the firefighter’s job — such as adjusting water pressure and controls. That way, jobs on the truck that would normally take three firefighters could be managed by one, freeing up manpower to fight the fires. That’s a level of added value that can actively save lives.
Another example came with an alternative transportation fuel provider that was driving toward integrating a touchless maintenance program. With around 560 unmanned fueling stations and 160 technicians located cross-country, extended downtime was an increasingly an issue. The company needed to implement a system that allowed them to instantly communicate with these unmanned systems to ensure they were running efficiently, to go from alert to repair in a shortened timeframe, and even identify issues before they could cause the station to fail. By working with Hitachi Solutions to implement their touchless system, the company was able to maximize its headcount — ensuring that problems could be solved on the first call and helping to generate better efficiency and greater value.
See more of the details of how we evolve your operations and services through connected products in this on-demand webinar.
Hitachi Solutions & IIoT Solutions
Industrial IoT is digital transformation on the grandest scale, and at Hitachi Solutions, we have the expertise to lead such a transition. We’ll work with you through this process in three steps:
Build and Find Value
We start by employing our enterprise knowledge to assist you in building and defining what will be your IoT value. This goes beyond considerations of infrastructure; it’s a partnership in understanding how to develop business cases and models to build a value case for investing in IoT for all stakeholders and accelerating its adoption.
Support IoT Infrastructure with Empower
Our enterprise-class Empower data platform provides Analytics as a Service to support you in overseeing the orchestration and operations of your data analytics. Empower handles much of the heavy lifting of data acquisition, mapping, modeling, and cataloging data, enabling you to have complete control over your information to get the full value of your IIoT infrastructure.
Focus on Action Outcomes
We employ our expertise in enterprise asset management, enterprise machine learning, and AI solutions to help you build action systems so that you can achieve desired outcomes with your data. We’ll work with you on developing systems like predictive maintenance models, asset management, and connected field service to convert your IoT data into actionable solutions so that you’re getting the full value from your investment.
If you would like to start implementing enterprise IoT solutions or would like to learn more about Hitachi for manufacturing, please contact our team.
IIoT FAQs
What are the essential steps for implementing IIoT?
Walk through the five building blocks of determining the devices, establishing how you’ll collect data, how will that data be communicated, platforms for data management and then — most importantly — what is the value that will be derived from that data.
One often overlooked element is who will own (and thus have the rights) to that data. If the legality of the data isn’t settled early on, it can be a nightmare down the line if it’s sold or utilized by third parties.
What are the software requirements for IoT development?
While your platform of choice can vary, understand that there is a massive amount of data that is streamed from your products in the field. All elements need to be able to easily scale, so the use of cloud native services is essential. Platforms like Azure Databricks, Azure Data Lake Storage, and Azure Data Warehouse are important parts of the software architecture.
How do we get value from IoT?
The best way to determine how IoT can deliver value is to talk with your customers. This conversation should include discussing their needs and pain points so that you can move them in the right direction for data collection. It can also highlight potential “as-a-Service” features they’d be interested in subscribing to.
How can I move from manual use of IoT data to machine learning AI?
Machine learning AI draws upon established models to determine how it will “learn.” The way to train AI models is to use your existing history of inputs and outcomes. If you don’t have an existing history to draw on, then you’ll need to build your own models.