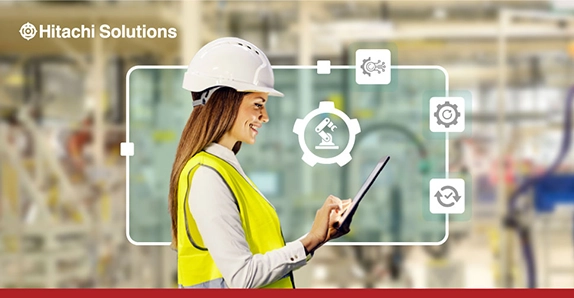
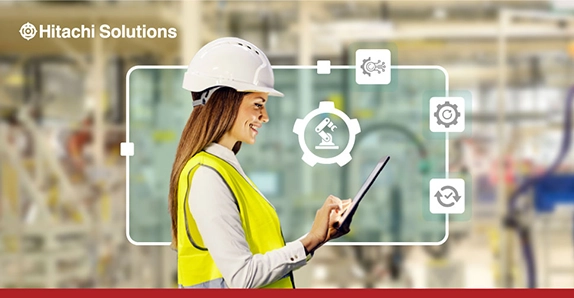
Recently, I moderated a panel at the International Society of Automation (ISA) conference. The topic is something I am very passionate about — advancing manufacturing through Industry 4.0 technologies.
The panel was a platform to showcase the latest industry thought leadership and what lies ahead, but also offered a roadmap to help businesses navigate their own digital evolution. From servitization to data-driven manufacturing, the discussion was invaluable for businesses seeking a competitive edge in the smart manufacturing landscape. I just thought It would be helpful to share some of the insights gleaned from the panel for those who weren’t able to attend:
Companies often categorize their smart manufacturing initiatives broadly under labels such as “Industry 4.0” or “digital transformation.” In reality, though, there are three distinct and sequential types of projects that contribute to these overarching goals.
- Modernization
This initial phase involves upgrading older systems and technologies to current standards, acting as a foundational step in the digital transformation journey. The goal is digitalization and the adoption of Industry 4.0 principles to align processes with modern technologies and capabilities. Examples include replacing manual record-keeping with cloud-based ERP systems, upgrading machinery to digitally controlled equipment, and migrating from on-premise servers to cloud-based systems for enhanced scalability and accessibility.
- Optimization
The optimization phase revolves around making existing processes and technologies more efficient and effective without undergoing fundamental changes. The objective is to use existing (ideally modernized) resources optimally, reducing waste, improving productivity, and increasing profitability. This involves implementing predictive maintenance software, employing data analytics tools to streamline supply chain management, and applying machine learning algorithms to enhance quality control processes.
- Transformation
The transformation phase represents a fundamental shift in how an organization operates and delivers value, often driven by disruptive technologies or changes in market demand. The aim is to create new value for customers and the organization, often leading to entirely new business models or innovative ways of working. Examples include creating digital twins for simulation and analysis of manufacturing operations, implementing IoT for smart factories with autonomous coordination, and using augmented reality or virtual reality for remote training and assistance.
Together, these three processes form integral elements of the overall digital transformation journey, enabling manufacturing businesses to evolve and thrive in the digital age by embracing modern technologies and innovative approaches.
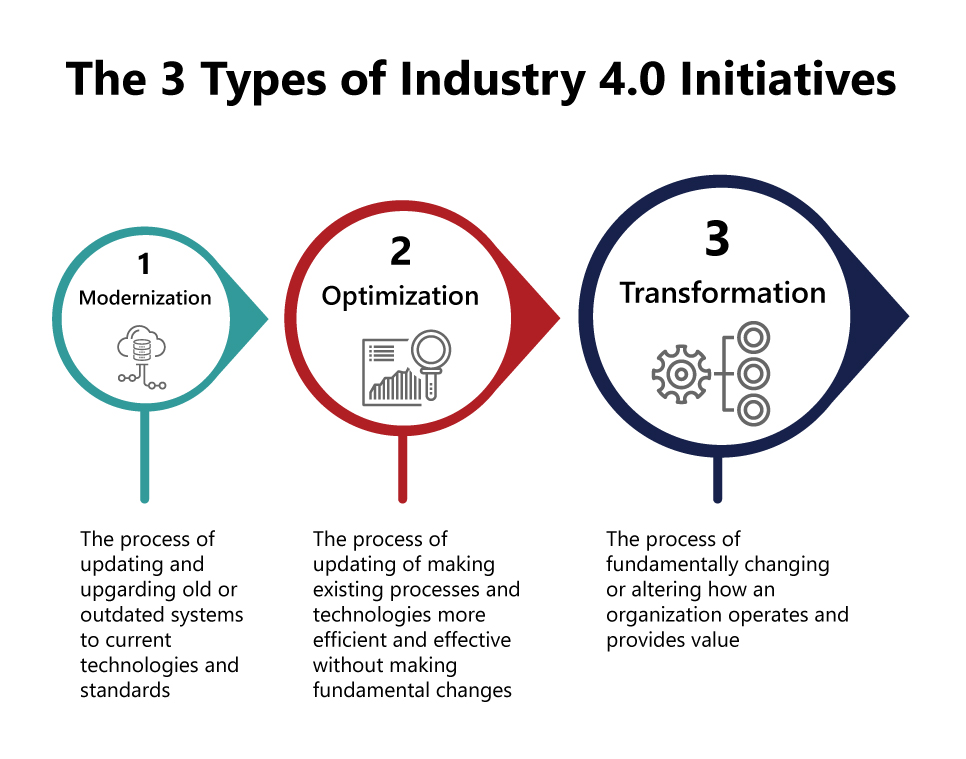
Looking Ahead with Hitachi Solutions
Hitachi Solutions strives to stay on the bleeding edge of Industry 4.0 and ready to help you embrace the next era of digital evolution.
As a technology partner, our deep industry expertise and extensive experience in all things digital transformation includes innovative technologies such as AI, IoT, machine learning, and cloud computing. We offer end-to-end solutions that facilitate intelligent manufacturing and smart factories, helping manufacturers achieve greater operational efficiency, improved productivity, and enhanced product quality.