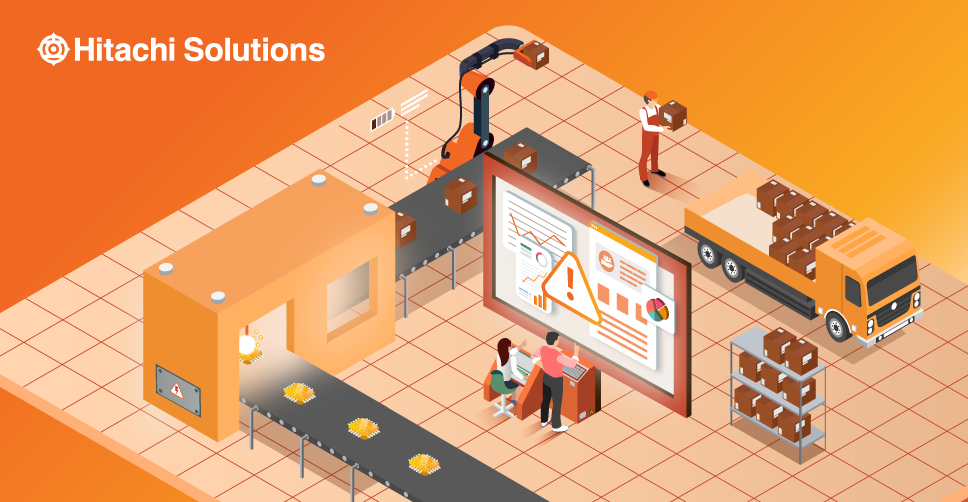
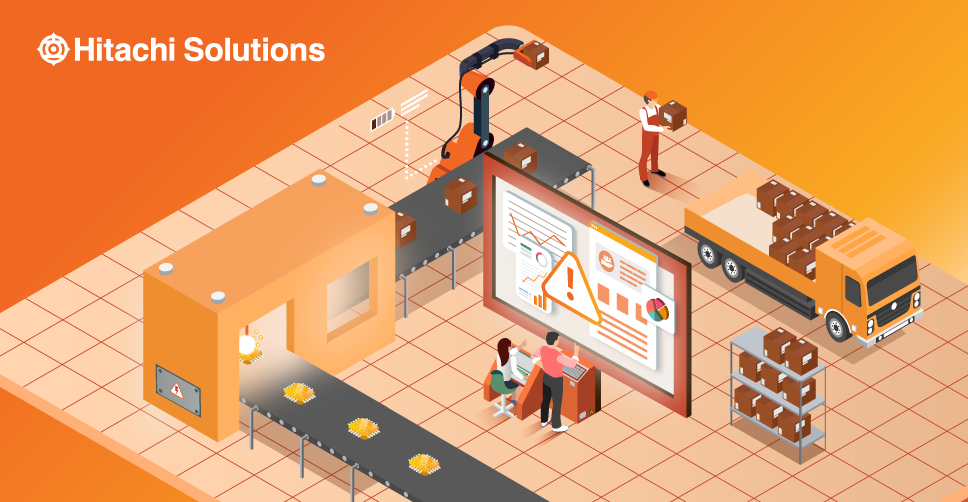
Maximizing the Retail Supply Chain
How to revolutionize your brand approach to create a truly frictionless retail customer experience
Download the WhitepaperThe supply chain is the gas that makes the motor run for manufacturing and retail. Without it, you have no product to sell, no inventory to stock, and no revenue to earn. Unfortunately, there will always be disruptions to the supply chain that throw everything out of whack and force both retailers and manufacturers to scramble to pick up the pieces. In a Gartner survey, only 21% of respondents stated they had a highly resilient network, though more than half expected to be “highly resilient” within a few years. That’s a positive sign, but what exactly can be done to get ahead of those supply chain risk factors?
Proper supply chain risk management enables businesses of all shapes and sizes to take advantage of tried-and-true strategies that mitigate risk and set them up for success. Implementing a comprehensive supply chain risk management plan ensures you’re prepared for both expected and unexpected disruptions. In order to develop your own risk management strategy, it helps to first understand what supply chain risks you might face.
What Are Some Supply Chain Risks?
Supply chain risk management refers to the process by which businesses take strategic steps to identify, assess, and mitigate risks within their end-to-end supply chain. Leveraging supply chain risk management software can give businesses a significant advantage by providing enhanced visibility and real-time data. There are both internal and external risks that can disrupt your supply chain, so it’s helpful to understand the difference between the two.
External Supply Chain Risks
As the name implies, these global supply chain risks come from outside of your organization. Unfortunately, that means that they are harder to predict and typically require more resources to overcome. Some of the top external supply chain risks include:
- Demand Risks: Miscalculating product demand often results from a lack of insight into purchasing trends or unpredictable demand, compromising your supply chain strategy.
- Supply Risks: Occur when the raw materials your business relies on aren’t delivered on time or at all, causing disruption to the flow of products and parts.
- Environmental Risks: Issues such as socio-economic, political, governmental, or environmental factors can affect the timing of any aspect of the supply chain.
- Business Risks: Arise whenever unexpected changes occur with one of the entities you depend on, such as the purchase or sale of a supplier company.
Enhancing end-to-end supply chain visibility helps in managing these risks by providing real-time updates on supply chain conditions.
Internal Supply Chain Risks
This refers to any risk factors within your control, identifiable through supply chain risk assessment software, robust analytics programs, and IoT capabilities. Although internal supply chain risks are more manageable, they’re still — to some extent — unavoidable. Here’s what to look for:
- Manufacturing Risks: The possibility that a key component or step of your workflow could be disrupted, causing operations to falter.
- Business Risks: Disruptions to personnel, management, reporting, and other essential business processes can impact operations.
- Planning and Control Risks: Caused by inaccurate forecasting and assessments, these risks highlight the need for an effective supply chain risk management plan.
- Mitigation and Contingency Risks: Arise if your business lacks a contingency plan for supply chain disruptions.
Familiarizing yourself with potential issues that might arise puts you in a better position to implement supply chain risk management strategies.
Supply Chain Risk Management Strategies
In today’s connected and digital world, supply chain risk management can be difficult due to globalization and potential cyber interference. That said, there are measures you can take to reduce your business’ exposure to risk:
- Leverage the PPRR risk management model. The PPRR risk management model is a popular global supply chain risk management strategy and is used by businesses around the world. This approach is a key part of a comprehensive supply chain risk management plan. The “PPRR” stands for:
- Prevention: Take precautionary measures for supply chain risk mitigation.
- Preparedness: Develop and implement a contingency plan in case of an emergency.
- Response: Execute on your contingency plan in order to reduce the impact of the disruptive event.
- Recovery: Resume operations and get things running at normal capacity as quickly as possible.
- Manage environmental risk in your supply chain. This is more important than ever given that the COVID-19 pandemic exposed gaps in global retail and manufacturing supply chains that leave them prone to disruption. Back in December 2019, many retailers were forced to re-evaluate their vendor relationships because many of their suppliers and manufacturers were based in China, which was, at the time, the epicenter of the outbreak. With a significantly reduced workforce, retailers struggled to process and get shipments out on time, and there were questions about whether certain shipments would need to undergo quarantine before they could be delivered. As a result, some retailers decided to move from a single-sourcing to a multi-sourcing model, an essential component of a robust supply chain strategy, which would provide them with a contingency plan should their primary supplier become unavailable.
Others opted to change their business model entirely in order to adapt to drastic changes in product seasonality and viability — for example, breweries and distilleries across the United States started to produce hand sanitizer on a massive scale, and Ford announced plans to produce ventilators for coronavirus patients at one of its facilities in Michigan. Although there’s no way to prevent environmental risk in your supply chain, you can plan for it by leveraging supply chain technology.
Supply chain risk assessment software enables you to take a proactive approach to risk management by providing you with greater visibility into the structure of your supply chain, supporting end-to-end supply chain visibility. With such a solution, you’ll be able to identify weak points in your supply chain and receive data-driven insights into how you can strengthen them. It’s also important that you develop a contingency plan — something that’s come up a few times now. Consider these strategies for improving supply chain resiliency:
- Multisource – multiple sources mean multiple ways around a problem. Categorize your suppliers not just by what you’re spending, but also by potential impact if there’s a disruption. Search for additional suppliers that you can do business with, or work with a supplier that produces out of multiple locations.
- Nearshore – look to find suppliers and distributors closer to your center of operation and/or the endpoint of your supply chain to reduce cycle times for product development and delivery. Regional suppliers can be more expensive, but by shortening the travel time, you can also reduce potential risks, enhancing overall supply chain risk management.
- Stress test often – mapping your supply chain network is just the first step. Comprehensive and recurring stress tests are the best way to check for vulnerabilities, some of which may lie hidden deep within the supply chain.
- Build buffers for inventory and capacity – this is an added expense, but smart planning can make it worthwhile. New product launches and expansions into new areas are perfect times to create buffer capacity. To reduce climate-related environmental risks, consider stockpiling products during known periods of high risk (such as hurricane season).
- Invest in product and plant harmonization – the use of identical technology for different components allows greater flexibility in case of a disruption. Using the same software throughout your network, especially cloud-based architecture, reduces the inefficiency of siloed data and allows for better communication between systems, bolstering supply chain strategy.
- Improve your cyber supply chain risk management. For many businesses, the Internet of Things and other digital technologies play a major role in optimizing supply chain operations, but they also leave businesses exposed to cybersecurity threats, such as malware, ransomware, phishing, and hacking. Environmental risks can further compound these vulnerabilities. To strengthen your cybersecurity defenses, try implementing the following supply chain risk management strategies:
- Establish compliance standards for all third-party vendors, including manufacturers, suppliers, and distributors.
- Define user roles and implement security controls to restrict who is able to access your system and what level of clearance they’ve given.
- Perform a thorough vendor risk assessment prior to signing any contracts.
- Implement data stewardship standards that define who owns certain data and what they’re to do with that data.
- Provide comprehensive training for all employees about cybersecurity protocols.
- Implement a software solution that provides you with total visibility into your supply chain, so you can quickly identify unusual activity.
- Work with vendors in your supply chain network to develop a unified disaster recovery plan to ensure business continuity.
- Establish backup controls to safeguard your data backups.
- Regularly update your company’s anti-virus, anti-spyware, and firewall software solutions, as well as look into more advanced cybersecurity measures, such as DNS filtering and network access control.
- Look for ways to improve supply chain visibility. More information can be beneficial, and a better understanding of all parts of your supply chain can alert you to issues before they become problems. Greater visibility into your supplier’s financial stability can assist you with selecting partners. Certain major credit rating agencies offer predictive financial stability reporting on thousands of potential suppliers in order to reduce the external business risk that comes with dealing with third-party vendors. Although this won’t help you with existing vendors, it can help you develop more secure business relationships and reduce your vulnerability to supply chain risk.
Look into supply chain technology that will allow for greater product and shipment visibility so you can keep your customers updated on delivery times and/or take action earlier to avoid costly delays and missed customer expectations. Service portals, IoT sensors on containers, automated reports on inventory levels, and more can help keep you informed and updated in real-time, providing comprehensive end-to-end supply chain visibility. This is especially vital during the “last mile” of delivery, where third-party services can take over, and you can lose insight over that stretch of the customer journey experience.
- Track the right freight carrier metrics. Manufacturers need to achieve dependable delivery to clients to build their reputation, while retailers rely on merchandise arriving at the right place at the right time in order to make selling windows. Regardless of where you are in the supply chain, it’s important that you partner with a freight carrier that can deliver consistent results. Unfortunately, not every carrier is up to the challenge, and even a single late delivery can disrupt your entire supply chain. When evaluating new freight carriers — or even re-evaluating your current freight carrier — be sure to consider the following metrics to support supply chain risk management:
- Transit Time: This refers to the number of hours or days it takes for a shipment to arrive at the customer’s location after leaving your facility.
- Number of Stops & Average Stop Time: The more stops a freight carrier takes en route to delivering a shipment, the longer it will take your product to reach your customer. Even if a route only includes a few stops, a long average stop time could still jeopardize on-time delivery and disrupt your supply chain. These metrics are important to monitor for the sake of supply chain efficiency. [Note: It’s important to look for a low number of stops and low average stop time while still being mindful of drivers’ legally regulated hours of service.]
- Average Loading Time: This refers to the amount of time it takes to load a carrier with freight, as well as fill out any necessary paperwork, once it has arrived at the loading dock. Like the previous item on this list, this is a key indicator of supply chain efficiency.
- Route Optimization: It’s important to consider how field carriers optimize routes for fuel usage and travel time because these have a direct effect on supply chain costs and efficiency. If a business has its own fleet, it can monitor this metric closely; if it partners with a third-party carrier, it can monitor this metric through costs charged for shipping.
- Maintenance Schedule: A freight carrier with a consistent maintenance schedule is less likely to break down, which can prevent unnecessary supply chain disruption.
- Implement a logistics contingency plan. Similar to an emergency response plan, it’s imperative that retailers and manufacturers have a logistics contingency plan in place to ensure business continuity in the event of supply chain disruption. The need for a solid contingency plan — or, preferably, multiple contingency plans — has become especially pertinent in light of the COVID-19 crisis, which caused supply chain disruption on a global scale, demonstrating the importance of a robust supply chain strategy. Some tips when creating a contingency plan for supply chain risk mitigation:
- Map out your supply chain to get a clear understanding of which entities are most vulnerable to risk.
- Perform a full assessment of suppliers based on factors such as political risk, geographic risk, and economic risk.
- Diversify your supplier network so that you aren’t reliant on a single supplier.
- Audit logistics providers based on their disaster plans.
- Establish a crisis response team to make critical decisions in the event of an emergency.
- Develop solid communication channels so that your employees know what their responsibilities are in the event of supply chain disruption.
- Carefully document all processes and create a single source of truth that employees can refer to when executing your contingency plan.
- Stay up to date on current events and adapt your contingency plan accordingly.
- Create a Plan B, Plan C, Plan D, and so on.
- Conduct internal risk awareness training. Management isn’t the only area of your organization that can assist in supply chain risk mitigation. In fact, building a risk-aware culture requires buy-in at all levels of your business. The easiest way to achieve this is to conduct risk awareness training for your entire workforce. Training curriculum should include the following:
- Common supply chain management risks and challenges
- Risk management best practices
- Computer and internet best practices to improve cybersecurity awareness
- Supply chain risk assessment software training to encourage end-user adoption
- Consistently monitor risk. This might seem like a given, but consistently monitoring supply chain risk factors really is the key to protecting your operations. Many organizations assume that they’re secure once they’ve implemented a supply chain risk mitigation framework, but the work doesn’t stop there. Every level of the supply chain should be carefully observed for potential risk indicators.
The easiest way to do this is to invest in a scalable supply chain technology solution that automates monitoring for various aspects of your supply chain. This will not only provide you with security and peace of mind but also valuable intel into how you can streamline business operations.
- Use data to model key risk event scenarios. Imagine being able to predict a risk event well before it ever happens. Technology hasn’t brought us there just yet, but thanks to data science, predictive analytics, and data modeling, we’ve come pretty close. Big Data has opened up a world of opportunities for businesses, including using data science and predictive analytics to create advanced models for potential risk event scenarios.
By using data models to forecast what could potentially happen during a worst-case scenario, you can develop more comprehensive contingency plans that will better prepare your business for when disaster strikes. Curious about how this “intelligent” supply chain works? Read our white paper on how you can compete and win with an Intelligent Supply Chain.
- Consolidate your data for easy access. Too many solutions in your software ecosystem can gum up the works, especially if you store business data in multiple disparate systems. In order to make it easier to leverage data science, predictive analytics, and data modeling, invest in a comprehensive retail solution that keeps all of your data within a single, centralized, and well-organized repository. This consolidation aids in effective supply chain risk management, ensuring smoother operations and enhanced supply chain visibility.
How Hitachi Solutions Can Help
Need supply chain management support? Hitachi Solutions can help. We’ve been building and implementing custom programs for retailers and manufacturers looking to improve all facets of their operations, including risk management, for 30 years. Our analytics and data science technologies help organizations like yours monitor supply chain activity, identify weaknesses, and make data-driven improvements. Contact us to digitally transform your business today.