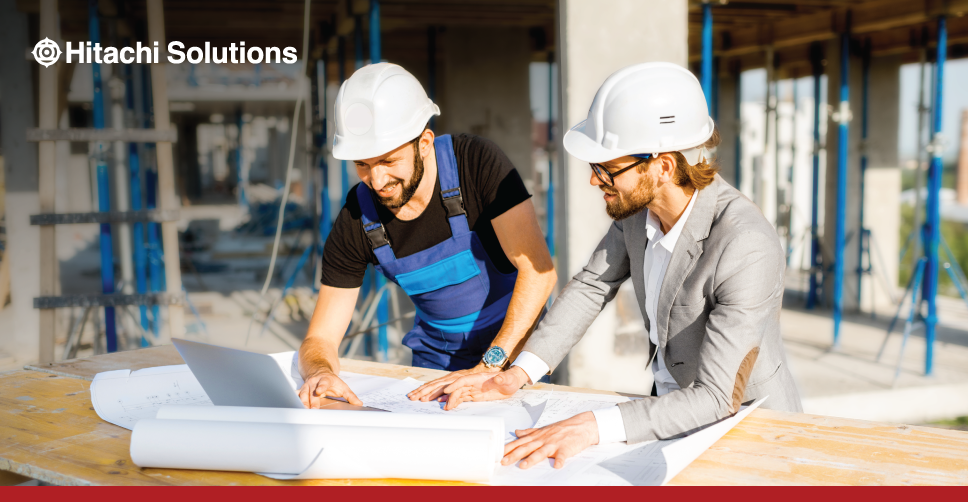
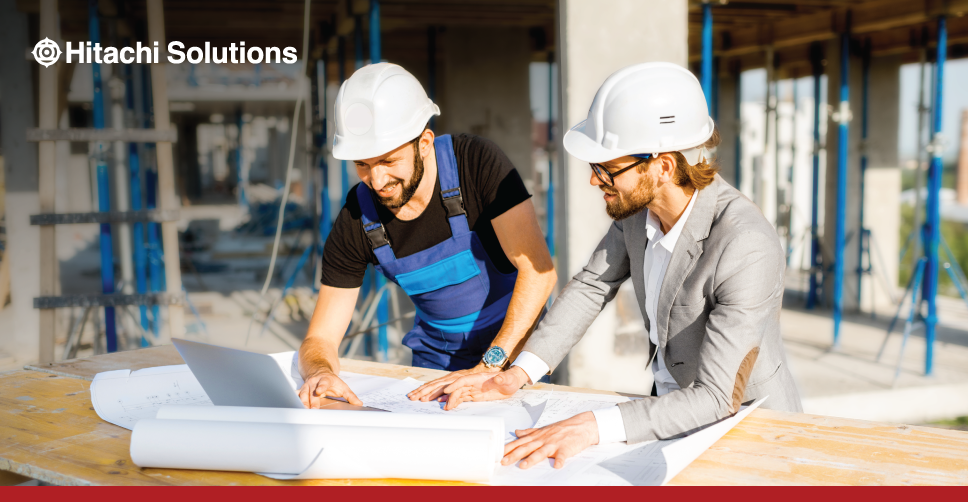
Safety, collaboration, adoption….
I recently sat down with Hitachi Solution’s AEC industry experts Jon Loring and Mike Oster to pull back the curtain on all things AEC, specifically the ways companies are looking at data and collaboration and how technology can be best used to make them more efficient, productive and cost effective.
Jon is the new AEC Strategy Director, and Mike is our VP for the AEC industry. Together, they’re always looking for innovation in applications, investigating how to use data from different angles, and sharing the expertise gained from their combined decades of hands-on experience.
So, grab a hard hat and a cup of coffee; here’s the insightful highlights from that conversation (edited for readability).
DH: When I think of architecture, engineering, construction (AEC), I’m seeing power drills, hammers, lots of noise, maybe some AutoCAD thrown in there. But how does technology actually fit into the picture today?
JL: There’s a real focus on those areas that traditionally have not had a lot of attention— productivity and capabilities that haven’t been considered in the industry. Better ways of collaborating and being more productive.
MO: It’s evolving. the other thing we’re seeing is the integration of things. It’s connecting all the systems together now and sharing that data in a data warehouse. And with that, new technologies such as AI and machine learning.
DH: The construction industry does seem to be lagging a little bit from a technological perspective. First of all, do you agree with that? Is AEC a bit behind the times and if so, why?
JL: In general, the industry has always been behind. There are other industries where technology has been a lot more pervasive than in construction. We’re dealing with job sites; we’re dealing with open fields where we’re putting up a building. We’re dealing with connectivity where different third parties are all coming together with different technologies. So, there’s always been the collaboration issue and the fact that where, in the case of a building, it’s something new every time and that makes it that much more difficult.
MO: Additionally, it’s not generally one company that’s coming in and building a building. You’ve got the general contractor and all the subcontractors, and sometimes even the subcontractor to the subcontractor. What system does each one use and how do they all share that information across different organizations?
DH: Because of the different companies coming together, they’ve got their own ways of working. That’s really the challenge that slows things down for the industry. Is that fair to say?
JL: I think so. It’s about looking at the productivity side and saying, hey, there’s a lot more here we can do, there’s a lot of ways in which we can be more productive.
DH: What are some of those long standing tech challenges? And, if we get a little bit more specific, what is happening day-to-day that leaders of AEC firms are racking their brains about and giving you guys a call to talk through?
MO: Adoption of technology out in the field is one of the primary things we hear about. You have to create these solutions for the people that are going to be using them and that’s one of the reasons there is still a lot of paper out in the field. We work with customers daily. Many are still using paper, Excel spreadsheets. Now that everyone is using cell phones, it’s helping bring the industry along because folks in the field can use technology because they all have a cell phone. If you make it an acceptable user experience, the adoption happens.
DH: Yeah, in the advisory services world, adoption is probably the number one driver in. When I first have a conversation with an executive, I’ll ask questions like tell me about your workforce. How many are actually in the field? Are any of them in remote locations? Tell me about your demographics and the conversation often starts with: “Well, they’re going to adopt it because we’re going to tell them they’re going to.”
MO: But it never works.
DH: Yeah. I actually had a conversation last week with a client and it was that very same talk track. We were talking about change management and he said I don’t think this is going to be an issue. And then they realized most of their workforce is on the brink of retirement. This (change) might push them there and then we have a different problem on our hands. And so, we talked about making sure the solution incorporates their feedback into the process, identifying how they learn best, tailoring training programs to ensure adoption, and bringing those employees along rather than forcing them into early retirement. Is this spot-on Mike?
MO: Let me give you an example. We have a customer who developed the system in the office and then pushed it out to the field. What they found was the adoption was terrible and quite frankly, they didn’t develop a system that their users were efficient in using. So, they brought it back in and created a center of excellence within their company, incorporating people from the field and now they use this center of excellence to make sure that it’s going to add value for the folks that are using the system. And it’s been a wildly accepted and just a huge, huge change for them in a positive way.
DH: We often say people buy what they help create, and that’s a perfect story for it.
JL: It’s not just employees, it’s all the partners that are collaborating together (that have to adopt). On a job site it could be the plumbers, electricians, the different trades coming together to solve the problem using technology. There’s a real need to make sure that whatever’s used is easy and simple and contributes productivity.
DH: Slow adoption, or lack of adoption, is a challenge. Is there anything else, Jon, in terms of coordinating work processes, or collaborating electronically? Is what’s being shared or communicated using cell phones or spreadsheets and email?
JL: Great question. I think the number one thing we see is coordination with drawings and specifications that needs to happen— making sure everyone is operating with the same versions, and that the information is timely. And that hasn’t always been there. Traditionally, it’s been internal solutions, large files like drawings that have been difficult to share over a wide area network. The ability for that type of coordination and productivity is going to go through the roof and there’s a lot of investment money going into it.
DL: When we’re talking drawings and model files are those very large? Is that hundreds of megabytes? Is that gigabytes?
JL: It’s hundreds of megs. Those models and they can be very large.
MO: We’re talking about drawings, AutoCAD, or a lot of photographs taken on the job site as well. Those are the largest files.
DH: What do those solutions typically look like then?
JL: Behind the scenes, there’s a lot of technology that determines file changes, for example, not having to upload the whole thing every time, caching locally, and uploading the delta. We need to be more efficient in how we handle these files. And those tools have gotten better and better, especially as hardware has gotten more powerful.
DH: Are there any issues with sharing files or working with CAD drawings, model files, et cetera, different platforms? Or is it usually pretty consistent?
JL: There’s a standardization, but the underlying technology is different based on how they were created. When you get into a shared medium, it tends to be PDF.
DH: And so, you could leverage things like SharePoint, OneDrive, to share files out. Can I assume the emergence of Microsoft Teams may be a boon for the AEC industry as well. Is that fair to say?
MO: It’s been a game changer. To be able to talk to all the people that are involved in, say a building, there could be 20,000 people! And to be able to have them all have a Teams account, and look at data and collaborate remotely is a huge advantage.
DH: I imagine security might also be a pressing issue for the industry. Is that a fair assessment?
MO: Positively. I want to point out people come in and out over the course of a project— people are laying the foundation or preparing for the foundation, and then you might have plumbers and electricians coming and going all the time. Security is a concern, and not just for the data, for the job site. Heaven forbid that something were to happen on a job site, you need to be able to immediately figure out who is onsite.
JL: We have different angles of security and it comes in a lot of different fashions. You need a centralized model for physical security. Who’s coming through the gate? In a lot of cities, it’s mandated by law to know who’s coming in and out. Creative solutions are being built, and the problem is getting easier and easier to solve.
DH: Do you mean for access to data and also for physical access to the job site?
JL: Yes, we’ve seen companies combine it. When you walk through the gate, you’ll have secure access to everything you need. It’s security compliance and safety, they go hand in hand. And there are a lot of different ways that we’re becoming better at it.
MO: Safety is a critical component of any solution on a job site. It can be millions and millions of dollars in inference cost, fines for non-compliancy. We’re seeing a lot of interest in things like checklists. So, when people are clocking in or clocking out, to be able to ask them about injuries and get sign-off. A lot of focus is on safety.
DM: Are we seeing the integration of these platforms where all the certifications, safety data, is being combined into the same platform?
JL: It’s more about how the information comes together in a way that that helps everybody. Typically, we have integration between different solutions. There are many ways we tackle it.
DH: Are we seeing AEC firms leverage BI dashboards? Maybe even machine learning or AI?
MO: On the ML front, we’re seeing smart building technology, construction firms are starting to embed sensors into the buildings. As construction progresses, they’re adding these machine learning IT sensors into the building. It’s becoming a revenue stream for a lot of construction companies. They charge a service to the end customer to monitor things like air conditioning compressors or boilers
JL: The ability to surface information as a top priority. As companies are dealing with different solutions, they need to make sense of all the information that crosses different systems— the aggregation of information leading to better processes and better data quality, all surfaced in a way where people can actually respond to it in the context of what’s being shown. Products like Power BI are almost universal in every company we talk to.
MO: It’s having that single view of data from all your disparate systems on one BI analytics dashboard instead of having to log into your ERP or your CAD system— being able to bring all that together into one single view or single pane of glass.
DH: We talk about moving from being reactive to proactive, to how can we make the next job more efficient or more cost efficient. So, rolling all the different ancillary systems into a single dashboard or 360-degree view makes a lot of sense.
MO: We talked a little bit about emerging IT technology like AI. What we’re seeing is the ability to mine that past data to see where there is opportunity for improvement. If you’ve built 10 data centers and you’re planning the 11th, what went right? What went wrong? It’s about taking that data from the past and using it to improve the future.
JL: There’s also an external component to that on the engineering and the architecture side where they’re actually selling that data as a service— the ability to do better monitoring as an ongoing service. For example, water quality or wastewater treatment plants are constantly looking for optimization and a lot of that is found in data that sits behind the solution.
DH: NowI see there’s forward momentum and movement in the AEC industry. This is an exciting time to be in the world of technology. I’m going to go ahead and bring us to a close but before I do, I’m going to go quickly on Amazon. think I’m ready to order my first hard hat after this discussion.
JL: You’re going to need gloves and glasses with that, Dave.
MO: And steel toed shoes.
DH: Added it to my list!
DH: I want to highlight some things for our listeners to take home with them as we bring things to a close. What we’re seeing is integration of systems. We spoke quite a bit about data coming together from ancillary systems and being able to make proactive decisions or react, when necessary, based on historical data to make better decisions moving forward.
Second, we hit on adoption early on, making sure that any solution considers the end users as it goes through design. Often, organizations think if we just build this tool and we tell people they’re going to use it, they’re going to use it. And what we find is that it’s not the case, or the ramp up to adoption is considerably slower, costing precious time and money.
And lastly, we discussed the integration of platforms and applications that focuses on data access, even building in job site access so we know whether an individual is qualified or certified to manage tools and have access to data.
Thanks again to our listeners, and thank you for hanging around with us. Be sure to tune in next time. If you liked what you heard, go ahead and subscribe where you get your favorite podcasts and check us out at global.hitachisolutions.com.
Hitachi Solutions + AEC Industry: Proven Success
Hitachi Solutions has a proven track record of empowering construction organizations worldwide to enhance their technological infrastructures. We offer a range of solutions, from connected, cloud-based construction management solutions to project accounting solutions and onsite mobile applications. All enable construction companies to stay ahead in an ever-changing landscape. If you have any questions, feel free to reach out. We are ready to assist you in unlocking data to help you improve the bottom line.