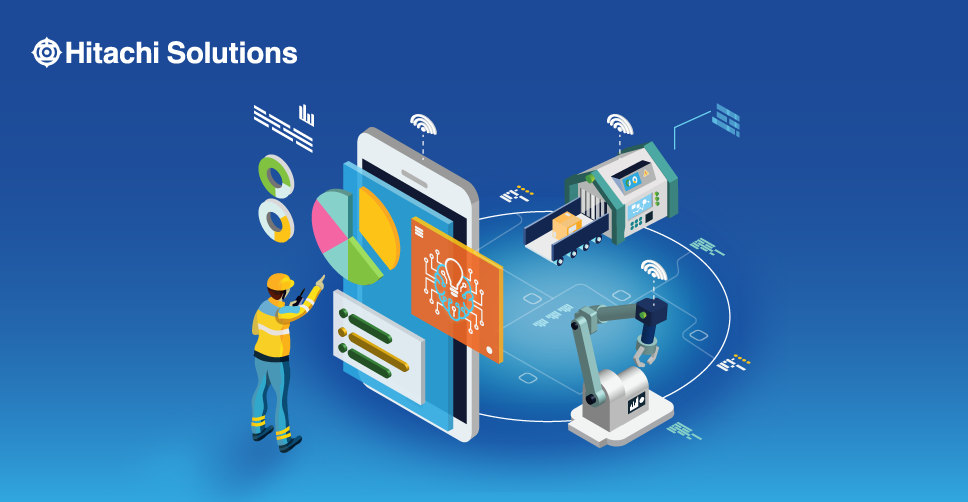
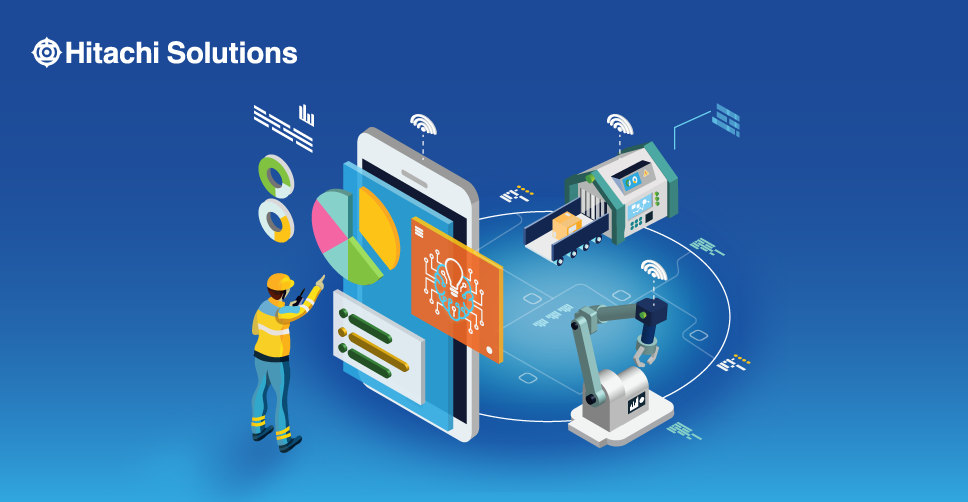
Smart Supply Chains Start with Smart Maintenance
An expert manufacturing perspective from Hitachi and Microsoft.
Download the WhitepaperFrom the COVID-19 pandemic to geopolitical events to natural disasters, recent events have exposed major vulnerabilities in the global supply chain. Though these may seem like dark storm clouds, there’s actually a silver lining: Ongoing supply chain volatility has motivated suppliers, manufacturers, retailers, shippers, and carriers alike to identify and resolve long-standing issues and create a stronger supply chain for the future.
With all of that said, not all threats to the global supply chain are external. Unplanned downtime — downtime that occurs unexpectedly, often due to equipment failure — can bring manufacturing production to a screeching halt. This can, in turn, have negative downstream impacts on the entire supply chain.
Fortunately, thanks to major technological advancements and the emergence of the smart factory, smart maintenance has made it possible to predict, plan for, and even avoid unexpected downtime.
The State of Maintenance in 2022
The manufacturing industry has undergone major changes over the past few years, including a change in perception.
According to Ali Aksut, the worldwide lead for Dynamics 365 supply chain and manufacturing at Microsoft, “Manufacturers are increasingly looking at assets as customers rather than cost centers to improve overall equipment effectiveness and other metrics.”
In a podcast interview, Aksut also stated that the events leading up to 2022 have shed new light on the importance of remote monitoring and diagnostics, leading to an uptick in manufacturers using industrial internet of things (IIoT) and telemetry to engage in proactive maintenance and make more informed decisions.
LISTEN TO THE PODCAST: Smart Supply Chains Start with Smart Maintenance >>
Maintenance departments have come to the forefront of people’s attention in recent years, as maintenance plays a vital part in ensuring the uptime of equipment and plants. And so, manufacturers and CPG brands are seeking to integrate maintenance more intentionally into their supply chain.
Smart maintenance provides manufacturers with a unique opportunity to optimize maintenance management, increase supply chain resiliency, and better navigate unexpected disruptions.
“Smart maintenance uses telemetry and sensor data from equipment to align and optimize maintenance schedules in conjunction with production schedules,” said Aksut. “As a result, you don’t cause self-inflicted disruptions in your own supply chain, you minimize equipment downtime and maximize its availability, and you can ramp up production without any issues.”
Another major change in the industry? An ongoing labor shortage compounded by a skills gap.
According to data from the National Association of Manufacturers (NAM), approximately 1.4 million U.S. manufacturing jobs were lost during the early days of the COVID-19 pandemic. Although the manufacturing job market has since rebounded, companies now struggle to fill vacant roles, with 77% of manufacturers reporting ongoing difficulties in attracting and retaining workers. All told, NAM predicts that as many as 2.1 million manufacturing jobs could go unfilled by 2030. Smart manufacturing — and, by extension, smart maintenance — aims to rectify this by leveraging predictive models and analytics to identify opportunities to optimize existing workflows, and then continuously automate processes so that companies can make the most of their existing headcount
What is Smart Maintenance?
So, what is smart maintenance, exactly?
Smart maintenance pairs wireless IIoT devices, such as sensors and gauges, with an end-to-end supply chain management application that uses artificial intelligence and machine learning to remotely monitor, analyze, and assess equipment performance. In doing so, smart maintenance enables manufacturers to proactively administer maintenance to machinery at the first sign of a problem, rather than after the problem — and downtime — has occurred. Smart maintenance allows for greater control over maintenance management, which, in turn, enhances equipment productivity and performance.
INFOGRAPHIC: How a Manufacturing Service Organization Uses Smart Maintenance >>
Smart maintenance can optimize any maintenance strategy from time-based preventative maintenance to run-to-failure, where equipment is deliberately operated until breakdown before maintenance takes place. With this degree of visibility and insight into equipment performance, maintenance managers are able to better predict asset failure and identify the next steps to prevent unplanned downtime.
Last, but certainly not least, smart maintenance offers organizations the ability to remotely manage the entire lifecycle of an asset from acquisition to retirement for more accurate cost analysis and ROI calculations.
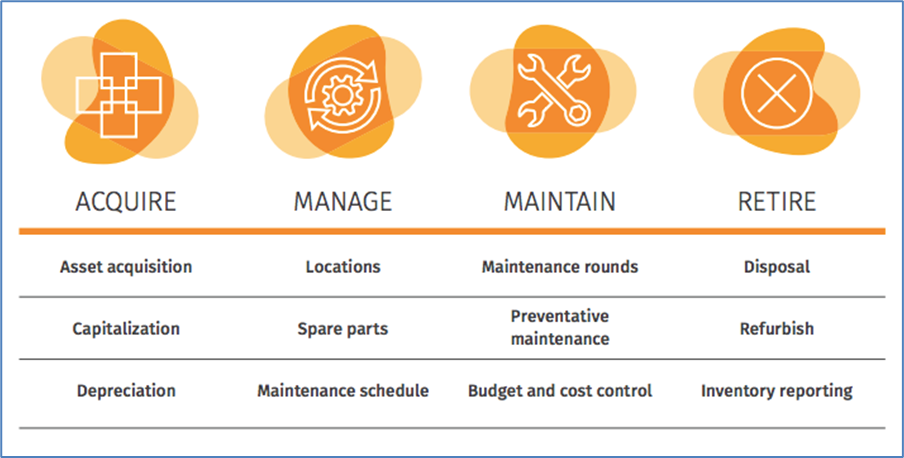
Is Smart Maintenance Right for Your Organization?
The simple answer is that smart maintenance is right for every manufacturing organization. Process manufacturers, discrete manufacturers, original equipment manufacturers, original design manufacturers, and more — manufacturing facilities of all kinds can benefit from the improved equipment uptime, enhanced productivity, and reduced maintenance costs smart maintenance has to offer.
10 Benefits to Implementing Smart Maintenance Technology
There are myriad benefits to introducing smart maintenance technology to any manufacturing facility. Smart maintenance can:
1. Prevent unplanned downtime. By using smart maintenance to access data-driven insights into equipment performance, managers can more accurately predict whether a machine is likely to malfunction and administer the necessary repairs to prevent downtime. In fact, according to McKinsey, smart maintenance can reduce equipment downtime by 30%–50% and increase equipment longevity by 20%–40%.
For a real-world example of how smart maintenance prevents unplanned downtime, look no further than Clean Energy Fuels, a natural gas distribution company. In a recent conversation with Hitachi Solutions, Group Vice President Bart Frabotta had the following to say:
“[With smart maintenance, we’re] looking at the predictive failure model now, with machine learning and AI, so now we’re working towards identifying issues before they actually fail. This will be a game-changer for us because now we can get a technician out there to repair the compressor before it goes down and take the pressure off them to get it back up.”
2. Eliminate unexpected costs. According to Aberdeen, unplanned maintenance downtime costs manufacturers an average of $260,000 per hour — that’s over $4,000 per minute! By enabling manufacturers to avoid unplanned downtime, smart maintenance can significantly reduce overall operating costs.
Cost savings aren’t the only way manufacturers benefit from smart maintenance — they also experience significant time savings. By introducing automation, manufacturers can eliminate tedious and time-consuming manual tasks, freeing up employees for more strategic work and making the most of their existing headcount.
3. Maximize equipment availability and efficiency. Being able to predict when a piece of equipment requires attention makes it possible to automate self-healing or proactively initiate work orders, saving on repair-associated time and costs. Based on research from Supply Chain Dive, smart factory strategies improve asset efficiency by 20% on average.
4. Improve workplace safety conditions. COVID-19 has accelerated the need to monitor operations and provide remote assistance. Smart maintenance enables maintenance managers to safely do their job without ever having to go onsite. Post-pandemic, smart maintenance will help facilitate better safety, faster training, and higher quality workmanship with intelligent tools and applications.
5. Increase production, quality, and uptime. According to Supply Chain Dive, smart factory strategies such as smart maintenance have been shown to improve indirect value drivers like product quality by 30%.
“Uptime is key. You get to a station, and that station has to get fuel in the truck. By having this visibility [into available resources], we’re able to go from alert to repair in a short time frame. Some of [our] service level agreements are sub-30 minutes, so reducing the amount of time that you’re getting the right person on the site to fix it or being able to alert the right technical team from a corporate perspective that can fix the issue is hugely impacted by [a smart maintenance] program.”
6. Act as a competitive differentiator. Again, according to Supply Chain Dive, 86% of U.S. manufacturers believe that smart factory initiatives — including smart maintenance — will be a main driver of competitiveness over the next five years.
7. Align maintenance schedules with production schedules. Too often, maintenance is isolated from production. Smart maintenance breaks down silos between the two, creating opportunities to plan maintenance around production demands. This enables manufacturers to more consistently meet deadlines and prevent supply chain disruption in the process.
8. Uncover asset performance and reliability insights. The ability to view an asset’s usage, issues, and repair history improves maintenance management and enables manufacturers to optimize spare parts inventory management.
9. Empower technicians to be more productive. Armed with a comprehensive and accurate view of equipment performance, usage, diagnostics, and other essential information, service technicians are able to make more informed decisions and problem-solve at a more rapid rate. Not only does this support technician productivity — it also eliminates pressure, creating a better work experience and enabling them to excel at their jobs.
This has certainly been true for the technicians at Clean Energy Fuels, who are “ecstatic” about their company’s smart maintenance program. Frabotta elaborates:
“What we’re now doing is not just creating a work order, assigning it to them, and then they drive there and do the diagnostics — with the IoT platform and full automation … that data goes straight from the source, which is the IoT order, all the way to the work order.
So, by the time they get to that station, they know what the alarm is, and they know what the three or four recommended solutions can be … They’re actually arriving on-site with the information they need to correct the problem quickly, and they have the resources back at corporate who are really looking at the system and guiding them through the process. So, we’re really shortening the time on-site when we are repairing things.”
10. Scale over time. Smart maintenance investment doesn’t need to happen all at once. In fact, gradually building a smart maintenance foundation enables manufacturers to better manage investment costs and build a solid business case for investment.
12 Tips to Start Your Smart Maintenance Initiative
For any manufacturer interested in taking advantage of smart maintenance, here are a few tried-and-true tips from the experts to help you get started:
- Conduct multiple proofs of concept to understand how different aspects of your organization can benefit from smart maintenance, and how best to scale your smart maintenance implementation.
- Develop a new mindset in which you treat maintenance and key assets like customers.
- Commit to moving from a break-fix or reactive maintenance model to a proactive one.
- Design a roadmap that aligns maintenance to your Industry 4.0 vision. This will help you develop an initiative that generates quick wins and additive capabilities and that secures execute buy-in.
- Find a solutions partner that not only brings technical expertise and smart maintenance implementation experience to the table, but that also understands what you’re trying to achieve and offers the flexibility to adjust your roadmap as needed.
- Implement IIoT-enabled sensors and start collecting data on equipment performance.
- Invest in condition-based or basic IIoT telemetry to improve remote monitoring and diagnostic capabilities.
- Adopt composable architectures from Microsoft to build a proactive maintenance model over time.
- Use the Microsoft Power Platform to enable real-time data gathering and streamline equipment maintenance.
- Utilize data to improve production scheduling, inventory management, quality, on-time deliveries, and other objectives.
- Leverage Dynamics 365 guides, machine learning algorithms, and Microsoft templates to create predictive maintenance capabilities.
- Be willing to face challenges head-on and change course as needed.
The Future of Smart Maintenance
Much of the technology behind smart maintenance is so advanced that it may seem like science fiction — but what’s next for this exciting field?
According to research from Market Research Future, the predictive maintenance market is projected to reach $111.34 billion USD in value by 2030, at a compound annual growth rate of 26.2%. From a tech perspective, the underlying technologies that make smart maintenance possible will become more sophisticated as they mature, as well as more affordable and accessible. This accessibility and availability will make smart maintenance a mainstay within the manufacturing sector, and we expect to see it go from a competitive differentiator to an industry standard.
Finally, as the technology behind smart maintenance continues to advance, we expect to see an industry-wide shift from predictive maintenance to predictive resolution. Predictive resolution takes the concept of predictive maintenance one step further, not only enabling technicians to identify anomalies in equipment performance and determine their root cause through data analysis but also offering them insights on how to resolve those issues with greater certainty.
To learn more about predictive resolution, and what’s in store for the manufacturing industry as a whole, we encourage you to read our blog post, 10 Trends That Will Dominate Manufacturing in 2023.
Mobilize Smart Maintenance with Hitachi Solutions & Microsoft
Ready to kickstart your own smart maintenance initiative? Hitachi Solutions is here to help. After over 10 years serving the manufacturing industry and with over 40 Microsoft Partner of the Year Awards to our name, we have both the industry and solutions experience to help manufacturers take advantage of Microsoft’s smart maintenance technology.
Bart Frabotta can attest firsthand to the benefits of partnering with Hitachi Solutions:
“Working with vendors directly, Hitachi Solutions has been a great partner. They actually have that relationship with our selected vendor, Microsoft, and we’ve broken through some ceilings we thought we’d reached, got some resolutions, and really refined the whole process.”
Get the full story behind how Clean Energy Fuels partnered with Hitachi Solutions to make fueling faster and more efficient in this on-demand webinar.
Watch It NowFrequently Asked Questions
Q: What is smart maintenance?
A: Smart maintenance is a maintenance strategy in which manufacturers leverage cutting-edge technologies such as the industrial internet of things, artificial intelligence, machine learning, and advanced analytics to remotely monitor, analyze, and assess equipment performance.
Q: How can manufacturers benefit from smart maintenance?
A: Smart maintenance offers a wide variety of benefits, chief among them that it enables manufacturers to proactively administer maintenance at the first sign of a problem, rather than after the problem — and equipment downtime — has occurred. Manufacturers that implement smart maintenance strategies also enjoy greater control over maintenance management, enhanced equipment productivity and performance, reduced operational costs, and the ability to monitor an asset throughout its lifecycle.
Q: How does smart maintenance improve supply chain resiliency?
A: In addition to preventing unplanned downtime, which can lead to downstream supply chain disruption, smart maintenance enables manufacturers to plan maintenance around production demands. By aligning maintenance schedules with production schedules, manufacturers can more consistently meet deadlines, again preventing downstream disruption.
Q: What technologies do you need to implement smart maintenance?
A: In order to reap the rewards of smart maintenance, manufacturers must invest in IIoT systems, AI, data analytics, mobile applications, and supply chain management solutions.