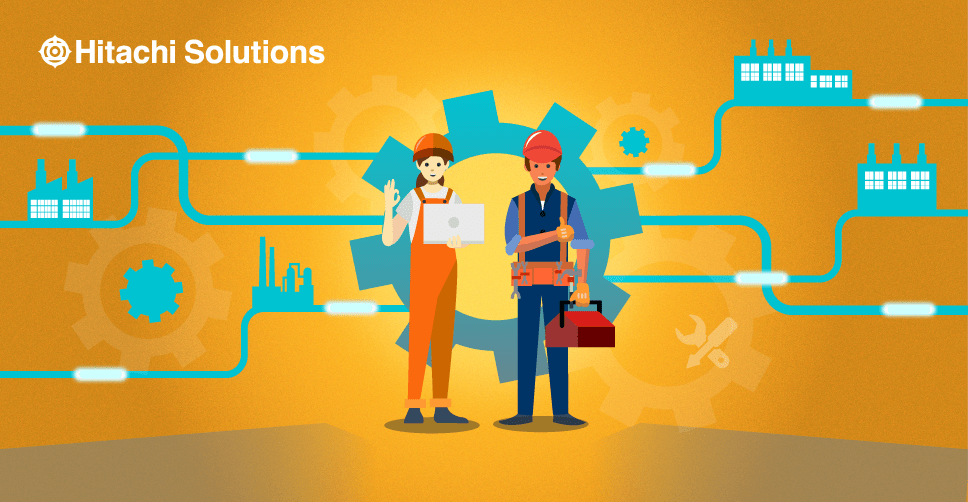
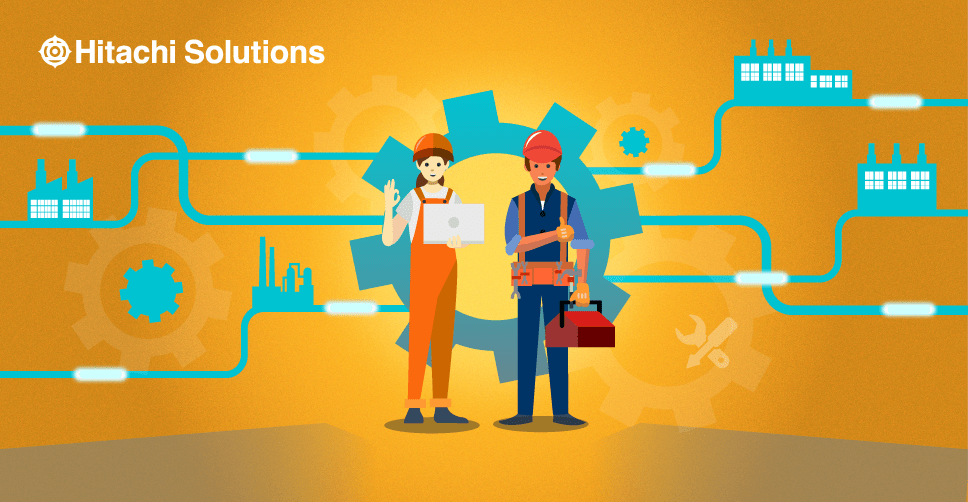
There’s nothing spare about spare parts.
Corny jokes aside, although it might seem like small potatoes, quality spare parts inventory management is imperative to the success of any manufacturer or maintenance team. After all, poor control and planning can lead to inefficient inventory storage and a shortage of parts when you need them most, which causes unplanned downtime and unforeseen costs. Therefore, for the overall success of your business, it’s in your best interests to invest in optimized spare parts inventory management, starting with these nine tips.
- Choose a Method for Labeling Critical Components
Though it might seem obvious, it’s still worth stating: The first step to managing your spare parts inventory is to clearly label each component so there’s no question as to what’s what. This is especially important for critical components — that is, spare parts reserved for machinery critical to business operations. There are two popular methods for inventory categorization and labeling: ABC analysis and XYZ analysis.
According to the Association of International Certified Professional Accountants (AICPA), ABC analysis “is an approach for classifying inventory based on the items’ consumption value,” wherein the consumption value is “the total value of the item consumed over a specified time period.” As you can easily infer, A parts have the highest consumption value, B parts have an intermediate consumption value, and C parts have the lowest consumption value. ABC analysis subscribes to the Pareto principle, or the 80/20 rule, in that 80% of the consequences come from 20% of the causes. As a result, A parts account for the largest percentage of parts used but the lowest percentage of inventory stock, while C parts account for the smallest percentage of parts used but the highest percentage of inventory stock.
Again, according to the AICPA, XYZ analysis is used “to classify inventory items according to the variability of their demand.” X parts offer very little variation and can be reliably forecast, Y parts offer some variation, but their variability is still relatively predictable, and Z parts offer the greatest degree of variation and are difficult to forecast. Like ABC analysis, XYZ analysis also subscribes to the Pareto principle, where X parts account for the largest percentage of inventory value but the lowest percentage of inventory stock, while Z parts make up the minority of inventory value but the largest percentage of inventory stock.
- Balance Inventory Volume With Sawtooth Diagrams
One of the most important spare parts inventory management system best practices to follow is to maintain a balanced inventory volume, though this is often easier said than done. Implementing ABC and XYZ analyses for categorization is a start, but a sawtooth diagram can help you contextualize how your inventory stock is depleted and replenished over time.
The Y-axis of the diagram should represent the inventory level, while the X-axis should represent time. The lines that make up the “saw teeth” should represent the steady decrease of inventory over time. Each peak represents the maximum inventory level, and the distance between each peak represents the amount of time between shipments, otherwise known as the cycle time. Additional markers within your sawtooth diagram should represent the reorder point and lead time.
In order for your sawtooth diagram to be an accurate reflection of your spare parts inventory volume, you must first establish minimum and maximum inventory levels for each spare part.
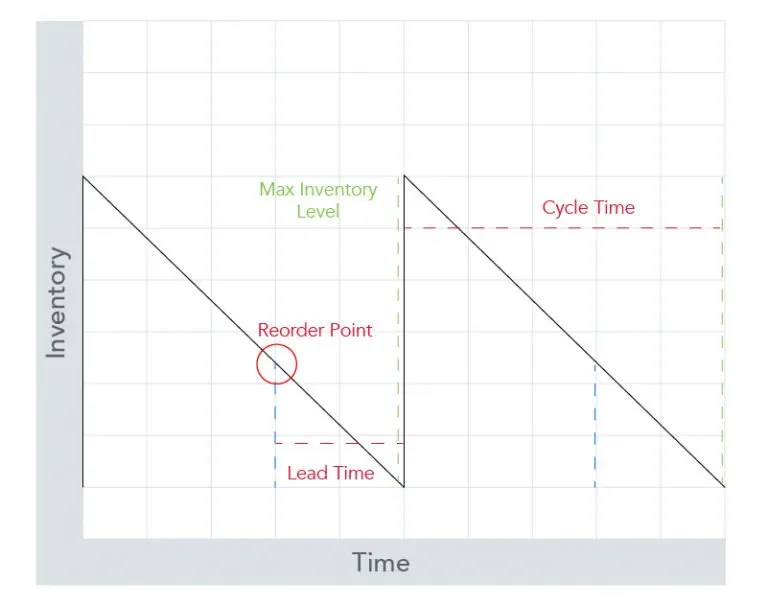
Keep Your Bill of Materials up to Date
Your bill of materials (BOM) is the winning formula for manufacturing an end product that’s light-years ahead of its competition. As a result, it’s vital that you keep your BOM up to date in order to prevent inventory inaccuracies and shortages of spare parts and to better plan for preventative maintenance or servicing. Take time to review your BOM on a regular or semi-regular basis to add or remove parts from it as needed.
- Calculate Optimal Economic Order Quantity
According to Investopedia, economic order quantity (EOQ) “is the ideal order quantity a company should purchase for its inventory given a set cost of production, a certain demand rate, and other variables,” and “is done to minimize inventory holding costs and order-related costs.”
You can use EOQ to determine the quantity of spare parts you need to order based on annual demand by using the following formula:
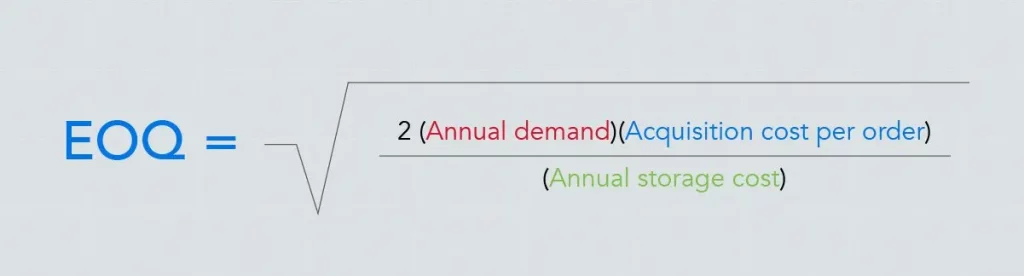
Develop a Standard Work Order Process
Manufacturers will sometimes store excess parts in an infrequently used section of their warehouse without bothering to label them in the centralized inventory management system. Other times, employees will forget to file a formal work order before removing an item from inventory to repair or service equipment. Such oversights can lead to inaccuracies in your records, which could cause issues further down the line. Therefore, it’s important to implement — and enforce — a standard work order process for greater accuracy.
There are a few things you can do to make your work order process more efficient:
- Hold employees accountable for following standard procedures
- Define consequences for failure to file a formal work order
- Introduce automated systems to reduce manual paperwork
- Simplify your process wherever possible
- Invest in quality employee training
Which takes us to the next item on our list …
Focus on Inventory Control During Employee Training
You can’t reasonably expect your employees to follow all processes and procedures pertaining to spare parts inventory management to the letter if they weren’t adequately trained to do so. That’s why it’s important that you invest in thorough, evaluative training for any employee — at any level of business — who interacts with spare parts. From online courses to seminars, there are any number of training programs to choose from; it’s in your best interest to select one that covers both standard processes and procedures, as well as any technology your business might use to optimize management.
- Perform Cycle Counts on a Regular Basis
One of the best ways to ensure inventory accuracy within your warehouse is to conduct cycle counts (audits of specific product groupings) throughout the year. Cycle counts are more convenient than total counts because they don’t interfere with normal business operations, which means they can be performed on a more frequent basis.
In order to ensure a successful cycle count, set the following parameters:
- Which inventory group do you need to cycle count (A, B, or C)?
- How many SKUs do you need to cycle count?
- Who will be responsible for the cycle count?
- How many people will be responsible for the cycle count?
- How frequently do you need to perform cycle counts for the inventory group in question?
- Make Spare Parts Easily Accessible
Make it easy for your employees to submit work orders and pull parts from warehouse shelves by storing spare parts within a centralized inventory system. With a clear idea of where everything is located within your warehouse, you can better guarantee overall accuracy.
- Invest in a Quality CMMS
A computerized maintenance management system (CMMS) can make it easier to implement some of the best practices listed above, as well as to analyze spare parts, optimize reorder points, and more. The real challenge, however, is to find a CMMS that can do it all.
Fortunately, there’s always Hitachi Solutions Parts Forecasting. Parts Forecasting is a CMMS designed to achieve optimal inventory levels in order to reduce parts overages and shortages. Parts Forecasting extends Hitachi Solutions’ core Field Service offering with advanced data and analytics and uses enterprise resource planning, intelligent machine learning, and IoT to provide accurate spare parts inventory and demand forecasts.
With Parts Forecasting, you can:
- Improve spare parts inventory turn time
- Reduce inaccuracies and shortages
- Eliminate service delays due to out-of-stock items
- Reduce inventory costs
- Increase service satisfaction and first-time fix rates
- And more
Hitachi Solutions Parts Forecasting is backed by the power of Microsoft, meaning users have access to Azure AI, Machine Learning, and Cognitive Services, as well as Connected Field Service for Dynamics 365. Best of all, by making Parts Forecasting your CMMS of choice, you’ll gain valuable support from the Hitachi Solutions team, which boasts decades of experience in the manufacturing industry.
To find out why Hitachi Solutions is so much more than just a solutions provider, contact us today.