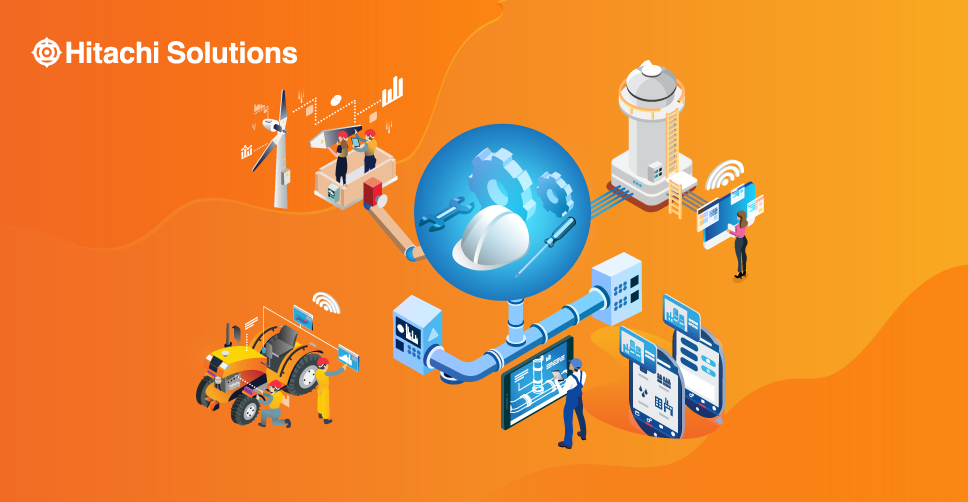
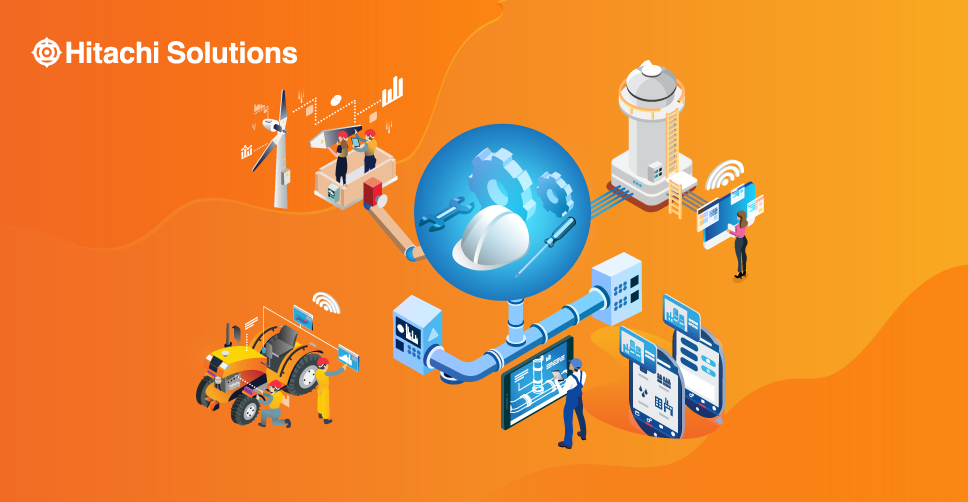
Personalize Care With Field Service
Get hands-on with Hitachi Solutions Home Health application, powered by Microsoft. Learn how organizations in the healthcare industry can get the most value out of our app, by improving the Home Health experience.
Watch the On-Demand WebinarAs the head of a field service company, your primary objective is to provide customers with fast, efficient, and effective repairs, but the usual way of doing business took an unexpected turn in 2020 due to COVID-19.
In the blink of an eye, companies had to restrict — or in some cases, pause entirely — in-person field service visits. The global pandemic caused a massive disruption in the field service industry, and since then, every field service company has likely reevaluated its business model in some way. Some have embraced the idea of contact or remote service, while others are investing in predictive maintenance.
As we continue to navigate COVID-19 and look toward the future, let’s examine these eight field service trends for 2022. This will help you get an idea of what best practices and technologies you should consider implementing to reposition your field service company for growth and opportunity.
1. Customer Self-Service Portals
Whether the issue they’re reporting is as serious as a piece of business-critical equipment breaking down or as minor as an air conditioning unit malfunctioning on a hot summer day, customers don’t want to call into schedule service, only to be put on hold. Unfortunately, that’s often the reality for customers, as labor shortages have stretched service organizations’ already thin call center resources even thinner.
In light of these challenges, customer self-service portals have gained significant traction in the field service industry and are a trend to watch in 2022. These portals put power in the customer’s hands, enabling them to report issues, schedule service appointments based on their availability, specify what type of service they’d like to receive (in-person vs. remote), monitor the status of repairs in real-time, complete payments, and share feedback. Some customer self-service portals even allow customers to choose which technician they’d like to work with, which is especially appealing if customers have consistently had positive experiences with a particular technician.
Customer demand for self-service options is well-founded and continuously growing: Data from Statista shows that 88% of customers say they expect organizations to have a self-service portal. Likewise, a report from Mordor Intelligence predicts that the self-service software market, which was valued at $7.2 billion in 2020, will register a compound annual growth rate of 20.94% from 2021 to 2026.
2. Remote & Contactless Service
The idea of remote service isn’t new, but it took on new significance in 2020 as field service technicians sought ways to limit exposure between themselves and customers, and it remained a leading trend throughout 2021. Advances in artificial intelligence (AI), augmented reality (AR), the Internet of Things (IoT), and other related technologies helped make this possible, enabling customers to act as the eyes and ears of remote technicians, and for technicians to guide customers through self-administered repairs.
Both customers and service organizations enjoy the benefits of remote service: By eliminating the need for technicians to physically travel to a job site, service orgs can reduce technician labor costs, travel time, and vehicle expenses.
In situations where remote service is not possible, contactless service — that is, in-person service that minimizes field interaction — has become the norm.
Contactless service enables technicians to receive job alerts from their mobile devices, dispatch from their own homes, check in once they’ve arrived at the job site, and complete necessary repairs. On the other side of the equation, customers can check to see that technicians are in route and monitor their location, get real-time status updates on repairs, and pay for service. All of this takes place without the customer or technician ever having to meet face-to-face.
According to Customer Think, an online community dedicated to customer-centric business strategy, changing consumer expectations in the face of new, pandemic-influenced realities driving the demand for remote and contactless:
“A new study examining consumer expectations of technical support and technician visits during the COVID-19 pandemic found that while most still expect their providers to resolve service and equipment issues as quickly and effectively as before the pandemic, 75% do not want technicians in or around their homes unless strictly necessary.”
Customers aren’t the only ones who benefit from remote and contactless service:
3. The Implementation of New Processes & Technologies
In the past, customers may have dismissed remote service visits as a waste of time, thinking that it was easier for a technician to make a site visit. But now, due to COVID-19, customers are embracing the idea of new technologies, meaning that companies can evaluate new processes and procedures with the long-term goal of making these permanent options.
For example, a technician can use AR and virtual reality (VR)-based applications and tools to access information about the device they’ve been sent to fix, including repair history and diagnostics, without having to take it apart. This remote access is made possible through integration between AR/VR applications, field service software, and/or customer relationship management software. Certain AR software even offers step-by-step repair instructions when imposed over the image of a device, making it possible for customers to perform minor fixes on their own equipment.
AR and VR can save your business time and money with remote assistance. Rather than perform repairs on-site, technicians can use wearables such as smart glasses to see what the customer sees and provide live customer service remotely. This technology is also useful in situations when a technician has been dispatched but runs into issues or requires a second opinion — rather than dispatch a second team, your company can use augmented glasses to connect the first technician with a secondary team operating at a central location.
“We’re going to see people use these technologies to keep their guests safe, to keep their customers safe,” said Harry Patz, Senior Vice President and General Manager of Samsung Electronics America’s Display Division, in a USA Today article about how businesses have turned to technology to cope with COVID-19. “And we think it’s just the tip of the iceberg. This is going to be a change to our way of life in kind of the same way that 9/11 forever changed airport security nearly 20 years ago.”
4. Predictive Maintenance Visits
Predictive maintenance refers to the idea of using artificial intelligence (AI), machine learning, and analytics to predict equipment failures or challenges before they happen. Predictive maintenance enables you to take the appropriate preventative measures in order to avoid unexpected failure and decrease maintenance costs.
Field service companies are now looking to predictive maintenance as the way of the future. Rather than peer into a crystal ball to see what malfunctions are on the horizon, technicians can use IoT-enabled tools to proactively monitor equipment health, and set up alerts, which are sent to an operator console in the event of a behavioral change, and execute predetermined actions to mitigate potential damage. Some tools even use cloud integration to simulate normal device behavior so that technicians can test out potential fixes in a secure environment before actually implementing them.
Predictive maintenance relies on predictive analytics, which uses historical data to match current behavior with past behavior and make an assessment. For example, if a piece of equipment is under the same conditions as the last time it failed, it will likely fail again. This will automatically prompt a work order schedule; companies can opt for remote service, first and send a technician, second.
The concept of predictive maintenance also enables companies to predict when it’s safest to do work, which means they can schedule appointments in such a way that they mitigate contact with other people.
5. Overhauling Risk Management Processes
Field service technicians have never had to worry about where they — or their customers — had been, but now, organizations are taking appropriate measures to ensure in-person site visits are as safe as possible.
Field service organizations are creating pre-screening questions that their technicians can use to gauge the risk of exposure for different jobs, especially those in high-risk populations, such as nursing homes or hospitals. This will likely be a risk management trend for the foreseeable future.
Pre-screening questions will typically ask technicians whether they’ve traveled to certain areas/states within a number of days or whether they’ve been in contact with anyone who has COVID-19. Companies can access the Centers for Disease Control & Prevention (CDC) Facilities COVID-19 Screening checklist online for additional guidance.
6. Contact Tracing
The CDC defines close contact as “any individual who was within 6 feet of an infected person for at least 15 minutes starting from 2 days before the illness onset (or, for asymptomatic patients, 2 days prior to positive specimen collection) until the time the patient is isolated.”
Since field service technicians often go from one place to another, it’s important to see where they’re going and where they’ve been. Microsoft PowerApps, for example, can track interactions and support contact tracing efforts. That way, if a technician does get sick or is exposed, you can easily determine who that person has been in contact with.
7. Investing in Experimental Technology
In general, COVID-19 has provided field service organizations with opportunities to redefine how they do business and has made them more likely to invest in experimental technology.
According to Field Service Digital:
“Digital transformation, whether in the form of accelerated implementation of new initiatives, or the innovative use of existing technology, has allowed service organizations to provide a measure of business continuity to their customer while at the same time containing operating costs and minimizing risks associated with deploying employees to the field.”
8. Product as a Service
We conclude with what we expect to be the biggest field service trend for 2022: Product as a Service.
Product as a Service — also known as PaaS or Servitization — represents a major shift from selling equipment as capital expenditure to an ongoing expense model with value-added services built in. Essentially, PaaS empowers manufacturers to supplement their existing product offerings with things like subscription-based maintenance programs, emergency services, and so on.
This business model enables manufacturers to grow aftermarket value streams and capture revenue throughout the equipment lifecycle and enables customers to buy only what they actually need. It also gives manufacturers access to usage data, which they can leverage to optimize long-term product performance and the overall customer experience.
It’s easy to see how manufacturers and end consumers benefit from PaaS, but what does it mean for service organizations? We expect PaaS to radically change the way field service is managed: IoT will become more important than ever before, with IoT-enabled devices acting as the primary source for usage data. Field service departments and technicians will become revenue generators rather than cost centers. Customer service and support will become even more robust, with organizations upping their investment in mobile solutions and experimental technology to optimize their first-time fix rate and increase customer satisfaction scores.
All told, Product as a Service will make service organizations — already an important component of any business — absolutely indispensable.
Empower Growth & Opportunity with Hitachi Solutions
Field service is no longer reactive — it’s proactive. If your goal is to empower technicians, increase customer engagement, and transform field service into a profit-generating arm of your business, these growing field service trends can help you pivot in the wake of COVID-19. The next step is to look into a comprehensive solution that can provide you with the capabilities necessary to put these trends into action.
Hitachi Solutions’ Extended Field Service, which is built on Microsoft Dynamics 365, is a holistic management solution that includes an extensive feature set to improve every aspect of field service operations, including customer assets, work order management, predictive maintenance, and more.
If you’d like to learn more about these and other field service trends or how your business can gain from a Dynamics 365 implementation, don’t hesitate to contact the qualified experts at Hitachi Solutions today.