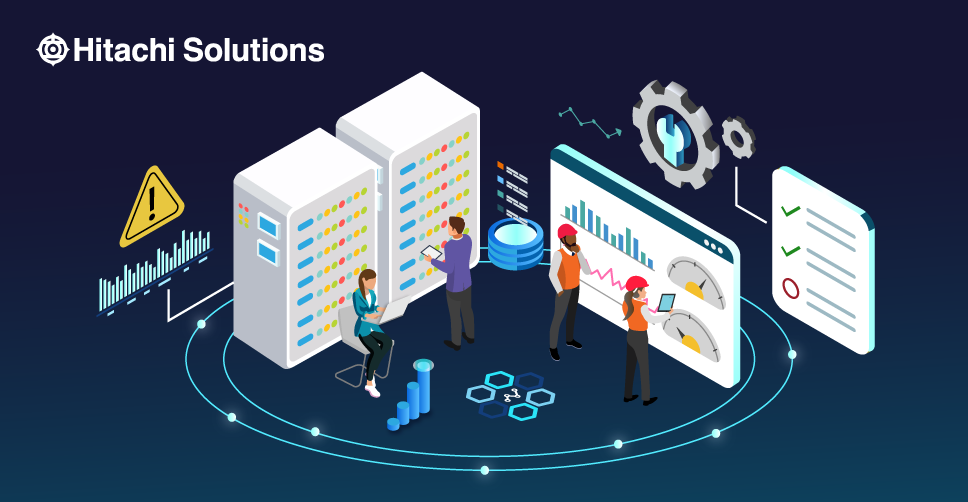
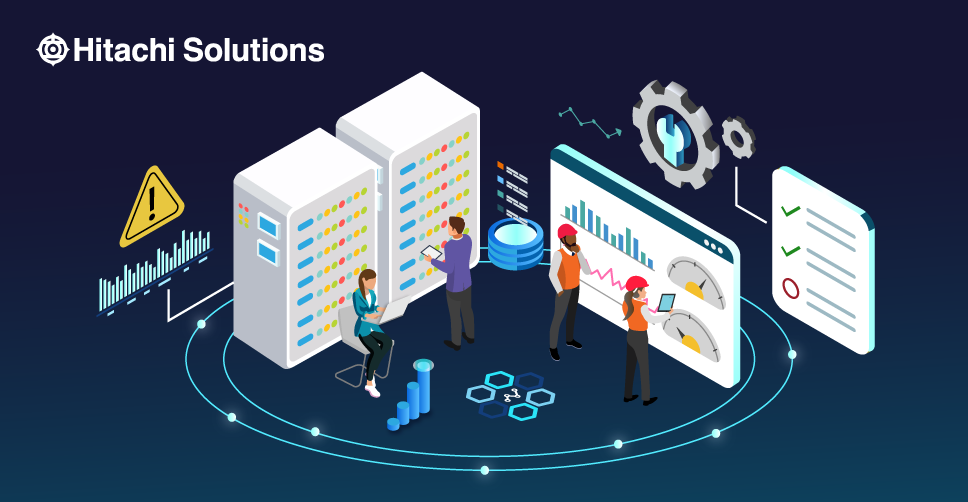
How Manufacturers Can Move to Predictive Maintenance
Five stages for making an incremental and successful transition
Download the EbookIn today’s uber-competitive environment, manufacturers need to optimize operations, and be agile and responsive, to scale and grow. Predictive maintenance has become an increasingly popular way to do this.
Data-driven, Outcome-based is The Future
Predictive maintenance leverages IoT, AI, ML, and the cloud to monitor system performance for potential issues. Technicians are notified ahead of equipment failure ensuring a quick response — often before a customer even knows there’s a problem. Also, the data that is collected can be used to provide diagnostic insights into how the equipment works and when it might fail. This is invaluable, saving time, money, and resources.
The transformative effects of predictive maintenance have been solidly established for manufacturers. Some of the top benefits include:
- Reduces unplanned outages and downtime, extends machinery life
- Improves problem diagnosis and resolution
- Improves service quality and customer satisfaction
- Helps monetize services and create new revenue streams
Experts Advise a Phased Approach
While predictive maintenance programs are becoming more widespread, it’s not always easy transition to this model. That’s because it involves more than just replacing technology — you also have to change the way you think, work, and operate. It can become complex and costly if not done right.
At Hitachi Solutions, we guide and advise companies through digital transformation. We’ve been doing it for almost two decades and seen it all — the good, the bad, and the ugly! One of the most important things we’ve discovered over the years, is that to follow these steps goes a long way to help simplify and speed the move to a predictive maintenance model.
5 Steps to Ease Your Way Towards Predictive Maintenance
Before you even start a move to predictive maintenance, though, you need to shift your mindset and culture to one that embraces digital technologies, processes, and competencies. You’ll also want to make sure you have c-suite sponsorship, strong leadership, expert advisors, and the right people in place to support the effort.
With this as your organizational foundation, you are ready to start your smart maintenance journey. To help you on your path, here’s an overview of what we feel are the five incremental steps for successful transition:
Step 1: Gain visibility into your data
The first step is to review your operations and identify your current systems and processes, and what data you are generating. Do you have access to the necessary volume and quality of asset and activity data to support a transition to predictive maintenance? For some, this will require transitioning from outdated legacy systems and manual and paper-based processes.
Migrating to the cloud, mobilizing applications, automating processes, arming employees with collaboration and communication tools, and designing processes and systems to generate data insights are some of the ways to prepare for a transition to predictive maintenance.
Step 2: Analyze and remediate data gaps
Every organization has different gaps and needs. Most customers we see have a need to supplement existing data. Others need to leverage structured and non-structured data. Still, others need to combine historic and real-time telemetry, from IoT-connected sensors and equipment.
The good news is, there are increasingly quick and easy ways to supplement and complement data. Hitachi Solutions has helped companies make this substantially easier. One way is through modern data management, which allows us to digitize large amounts of data to quickly pave the way for analysis and learning.
Step 3: Learn quickly — Analyze and understand key trends
Predictive maintenance requires a whole new level of domain expertise — to understand the latest technology and data models, collect and analyze the data, create new reporting and spot the trends, apply the learnings, and more. While there are pre-built machine learning models and algorithms to make it easier and speed up the learning process, most companies simply don’t have the in-house resources or skills to figure out how they work or how to manage the data. A lot of time, effort, and investment can be wasted trying to do this yourself.
Companies that are most successful at adopting and deploying predictive maintenance don’t do it alone. They leverage data and analytics experts — who have done it all before — to help get them up to speed quickly, boost time to benefit, and scale for maximum value.
Step 4: Prepare to pilot your organization for predictive maintenance
Predictive maintenance is best viewed as an organizational capability rather than a technology. What parts of your business, processes, and systems do you need to change to support predictive maintenance? Which workloads will need to be reviewed and changed? How does sales, service, billing, etc. need to adapt? These are all daunting questions to be sure.
We’ve found that when it comes to predictive maintenance, it’s much better to start small. Taking a proof of concept approach — targeting a specific product or service, stakeholders, and operations and processes — makes it easier to begin and measure success. But don’t take our word for it, VP Bart Frabotta from Clean Energy Fuels cites this as his number one piece of advice for organizations starting their predictive maintenance journey. Watch his Predictive Maintenance in the Real World on-demand webinar or read theHow Touchless Predictive Maintenance Drives Results blog to learn directly from Bart — he has a lot of other great insights to share as well!
Step 5: Measure and position for expansion
Piloting projects also makes it easier to measure the success of your predictive maintenance initiatives. By developing rigorous KPIs, benchmarks, and monitoring protocols, you’ll be able to quantify the benefits. This is important if you want to maximize ROI and scale your efforts to other plants and locations.
By measuring the right things and demonstrating the value to the company, you’ll be able to “sell” the program, gaining more buy-in from corporate sponsors — with hopefully deep pockets — so you can continue to land and expand a predictive maintenance model enterprise-wide.
Data is The Key
The beauty of predictive maintenance is data, and the more data the better! It gives you insights and helps you discover opportunities for improving your services and business. So to make your move to smart service, you’ll need to be cloud-enabled and implement a modern data platform. You’ll also need to incorporate the right blend of artificial intelligence (AI), machine learning (ML), and advanced analytics tools to collect, ingest, and operationalize the data to develop diagnostics, trends, and frequent maintenance scenarios.
The five steps above also set the stage for evaluating your real-world data usage and identifying and delivering new concierge services for customers — such as remote monitoring, self-service portals, and other high-performance services. These value-added solutions are compelling to customers because they promote accessibility, ease of doing business, and peace of mind. This not only attracts new customers but creates stickiness and customer loyalty for long-term relationships.
Ready to Embrace Predictive Maintenance?
If you’d like to take a deeper dive into our predictive maintenance insights, check out our recent ebook: How Manufacturers Can Move to Predictive Maintenance. It’s a simplified guide to understanding predictive maintenance, its features and benefits, how it compares to preventive maintenance, the challenges, and much more. It also has other tips for a successful transition.
No matter where you are on the path to predictive maintenance, Hitachi Solutions can help.
We know digital transition is a whole new world, and we’re able to provide you with the right expertise, tools, and technology to keep you on track. Contact us with any questions or to learn more about how we can help you.